Passage au chargement modulaire dans les exploitations de poulets à griller de l’Ontario
Apprendre comment fonctionnent les systèmes de chargement modulaire et comment effectuer la transition vers le chargement modulaire dans les élevages de poulet à griller. Ces renseignements techniques sont destinés aux éleveurs de poulet à griller de l’Ontario.
ISSN 1198-7138, Publié février 2020
Introduction
Le chargement modulaire est un système éprouvé de manipulation des volailles, utilisé pour transporter ces dernières, de l’exploitation avicole aux établissements de transformation (figure 1). Ce système a déjà été mis en œuvre avec succès dans de nombreux États ou provinces d’Amérique du Nord et ailleurs dans le monde. Le chargement modulaire améliore l’efficacité du chargement, le bien-être des volailles durant la manipulation et le transport, ainsi que la qualité et la salubrité de la viande. La sensibilisation croissante du public aux questions de bien-être animal incite l’industrie avicole à adopter ce nouveau système.
La présente fiche technique explique le fonctionnement des systèmes de chargement modulaire ainsi que les exigences physiques requises pour l’utilisation de ce matériel. Elle explique également les modifications qui pourraient devoir être apportées aux installations existantes pour vous aider à effectuer les changements nécessaires afin d’utiliser ce matériel. Si vous planifiez construire un nouveau poulailler, la présente fiche technique contient aussi des détails dont vous devriez tenir compte dans votre planification afin d’accommoder le chargement modulaire.
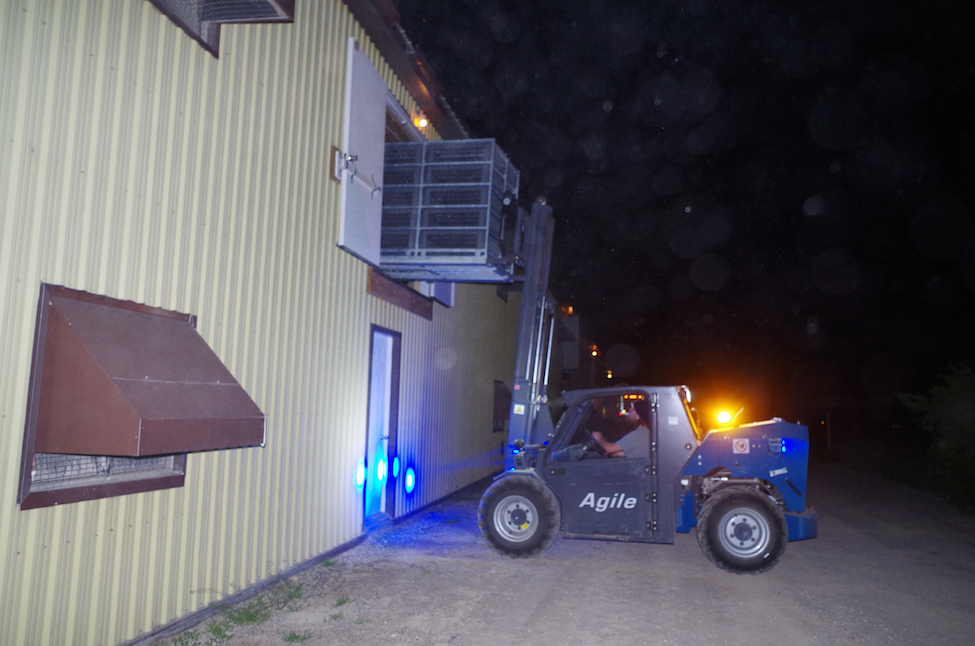
Systèmes de chargement modulaire
Les modules sont en fait une série de tiroirs en plastique moulé placés dans un châssis métallique tubulaire soudé. La plupart des entreprises utilisent des châssis de métal galvanisé ou d’acier inoxydable qui résistent à la corrosion, étant donné que le matériel doit être lavé quotidiennement après utilisation. Chaque module est soulevé du camion avec un chariot élévateur et placé dans le poulailler où les équipes de ramassage les attrapent et placent les oiseaux directement dans les tiroirs. Dans l’ancien système de chargement des cageots, les équipes de ramassage devaient attraper les oiseaux et les transporter dans le poulailler, où ils étaient passés à d’autres membres du personnel, à l’extérieur du camion de transport, pour être placés dans les cageots. L’ouverture sur le dessus des tiroirs est beaucoup plus large que celle des cageots à volaille habituels actuellement utilisés, ce qui permet de considérablement atténuer l’inconfort associé à la mise en cage des volailles et de réduire la durée du chargement. La manipulation réduite des poulets, conjuguée à la plus grande ouverture des tiroirs, réduit les risques de blessure aux oiseaux (figures 2 et 3). Une fois que tous les tiroirs sont remplis, le chariot élévateur rapporte le module jusqu’au camion.
Les systèmes modulaires permettent aux établissements de transformation d’intégrer le processus d’étourdissement au gaz dans la zone de réception des oiseaux avant l’accrochage. Cela signifie que les volailles vivantes ne sont manipulées qu’une fois de la capture à l’accrochage, ce qui améliore leur confort, de même que la qualité et la salubrité de la viande.
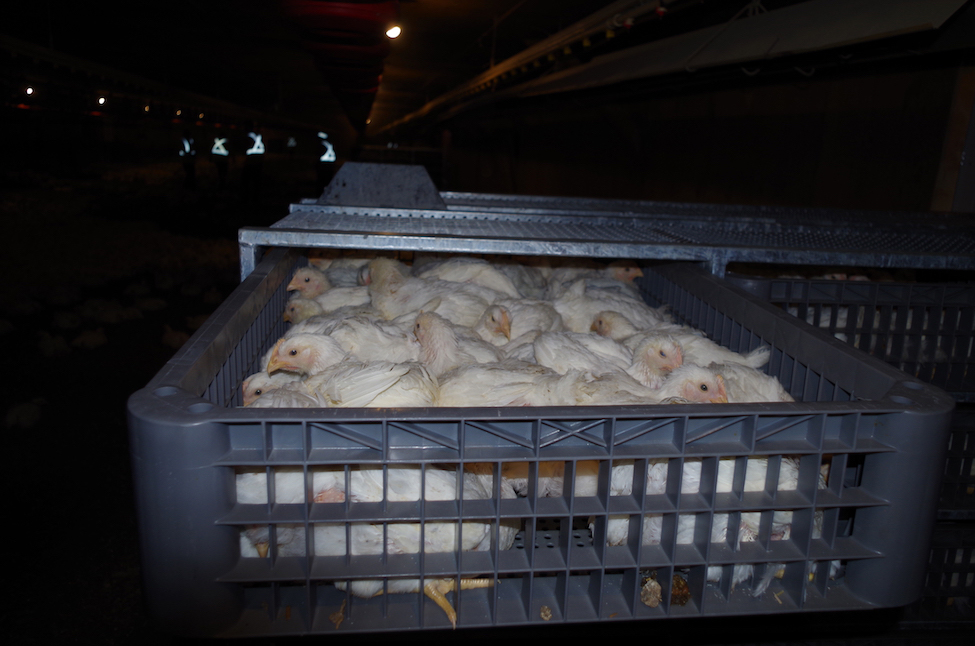
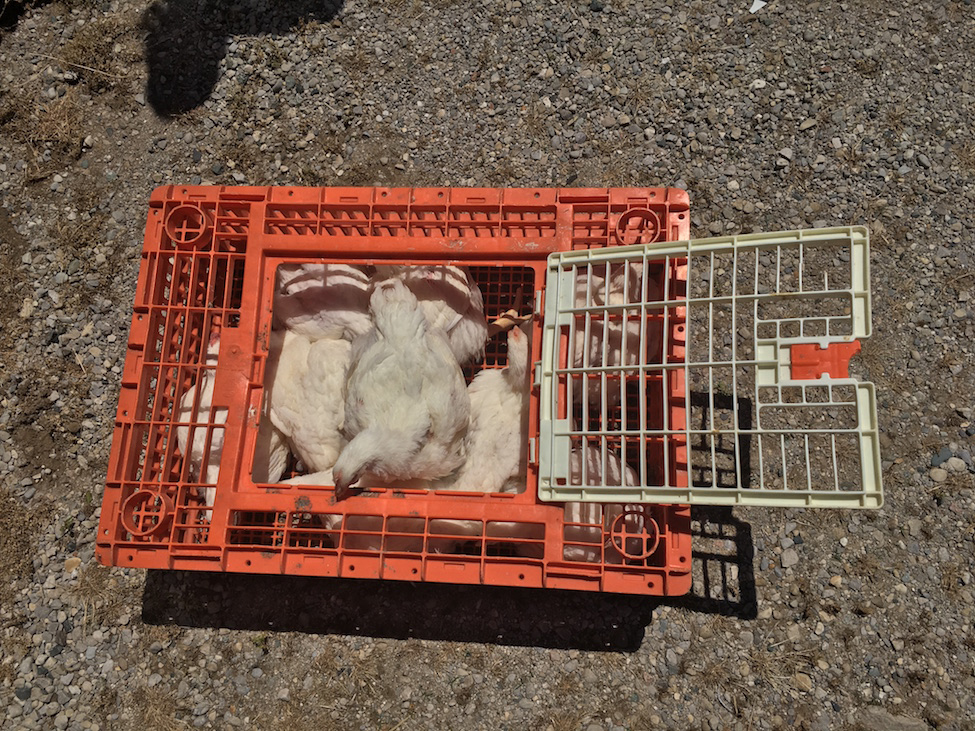
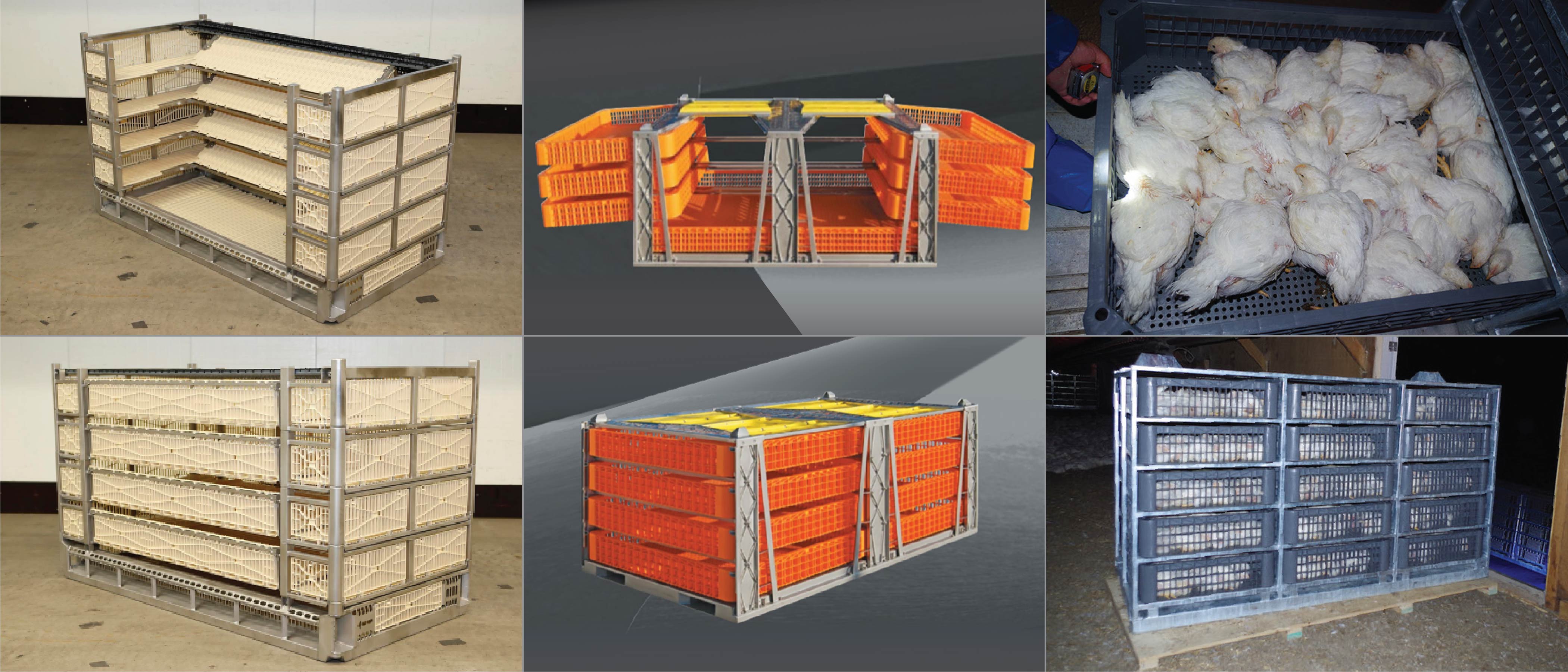
Modules
Plusieurs entreprises offrent des modules à l’industrie du poulet à griller, dont Anglia Autoflow, Bright Coop Ltd., Marel-Stork Poultry Processing, Meyn Food Processing et CM2A. La figure 4 présente des exemples de ces modules. À noter que ces fabricants sont mentionnés à titre d’exemple seulement et comme sources pour effectuer des recherches additionnelles sur le sujet. Le Ministère de l'Agriculture, de l'Alimentation et des Affaires rurales (MAAARO) ne cautionne ni ne recommande aucun de ces fabricants de modules en particulier.
Bien qu’il y ait de légères différences entre le matériel offert par chaque fabricant, comme le nombre de tiroirs, la hauteur du module, le poids à vide, etc., il existe aussi certaines similitudes, puisqu’il s’agit de matériel qui est transporté sur des remorques routières assujetties à des dimensions règlementaires. Le tableau 1 présente une comparaison entre des modules d’une hauteur de cinq tiroirs pour une remorque de pleine largeur, offerts par trois des entreprises mentionnées plus haut.
Pour la mise à jour du présent document, le module double de marque Meyn Maxiload d’une hauteur de cinq tiroirs a été choisi pour établir les charges de plancher prévues, car il s’agit du plus lourd des systèmes utilisés en Ontario.
Fabricant | Marel-Stork | Meyn Maxiload double | CM2A |
---|---|---|---|
Nombre de tiroirs | 5 | 10 | 15 |
Longueur du châssis | 2 430 mm (95,7 po) |
2 435 mm (95,9 po) |
2 438 mm (96,0 po) |
Largeur du châssis | 1 200 mm (47,3 po)
|
1 350 mm (53,1 po) |
1 165 mm (45,9 po) |
Hauteur du châssis | 1 415 mm (55,7 po) |
1 445 mm (56,9 po) |
1 497 mm (58,9 po) |
Poids à vide (châssis + tiroirs) |
342 kg (754 lb) |
486 kg (1 069 lb) |
427 kg (939 lb) |
Poids en charge maximum (châssis + tiroirs + volailles) |
1 122 kg (2 468 lb) |
1 441 kg (3 170 lb) |
1 225 kg (2 695 lb) |
Poids des volailles/tiroir | 160 kg (352,0 lb) |
95,5 kg (210 lb) |
53,2 kg (117,3 lb) |
Données relatives aux bâtiments d’élevage
Une étude réalisée en 2010 a montré que le nombre et la diversité des poulaillers en Ontario constituent en fait la plus grande contrainte à la mise en place de systèmes de chargement modulaire. En 2018, on comptait environ 2 100 poulaillers de poulets à griller en Ontario. Parmi ceux-ci, environ 48,5 % sont des bâtiments à un étage, 47,2 % ont deux étages et 4,3 % en ont trois ou plus. Il peut s’agir de nouvelles constructions comme de poulaillers bâtis il y a plus de 40 ans.
Les dimensions des bâtiments de même que les techniques et les codes de construction ont évolué avec les ans afin de refléter les progrès technologiques et les changements dans les méthodes utilisées (comme l’utilisation de plus gros tracteurs pour nettoyer le fumier). Un poulailler à deux étages construit il y a 30 ans est considéré comme étant une utilisation dérogatoire autorisée; il n’avait cependant pas été conçu initialement pour soutenir les charges de plancher qui figurent dans les codes de construction plus récents.
L’utilisation de modules chargés sur un plancher déjà existant au deuxième étage d’un poulailler exige une évaluation de la structure par un ingénieur. Il peut aussi être nécessaire de renforcer cette dernière afin de s’assurer que le bâtiment est en mesure de soutenir les charges prévues en toute sécurité.
Les entreprises responsables du ramassage des poulets exigent la production d’un rapport d’ingénieur signé lorsque les travaux de conversion sont terminés. Ils sont ainsi assurés que toutes les précautions raisonnables ont été prises pour protéger leurs travailleurs d’une défaillance de la structure. Cette vérification offre aussi au producteur une garantie que le poulailler ne sera pas endommagé en raison du poids des modules chargés.
Données relatives au chariot élévateur ou au télémanipulateur
Les caractéristiques du matériel requis pour déplacer les modules sur le site de l’exploitation sont assez précises (figures 5 et 6). Il doit être suffisamment bas (hauteur de mât, hauteur de la cabine) pour pouvoir pénétrer en toute sécurité dans le poulailler sans heurter le matériel ou la structure. Il doit être très facile à manœuvrer (court rayon de braquage) afin de pouvoir être utilisé dans des endroits restreints. Le chariot doit aussi offrir une capacité de levage qui lui permet de déplacer des modules entièrement chargés ainsi qu’une portée suffisante pour placer les modules dans les ouvertures du deuxième étage.
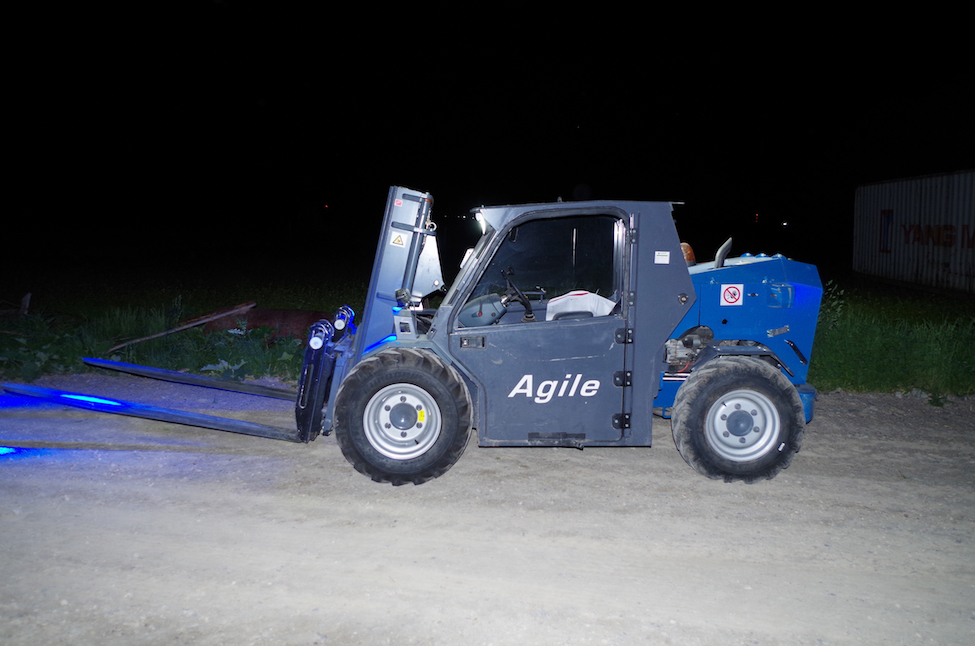
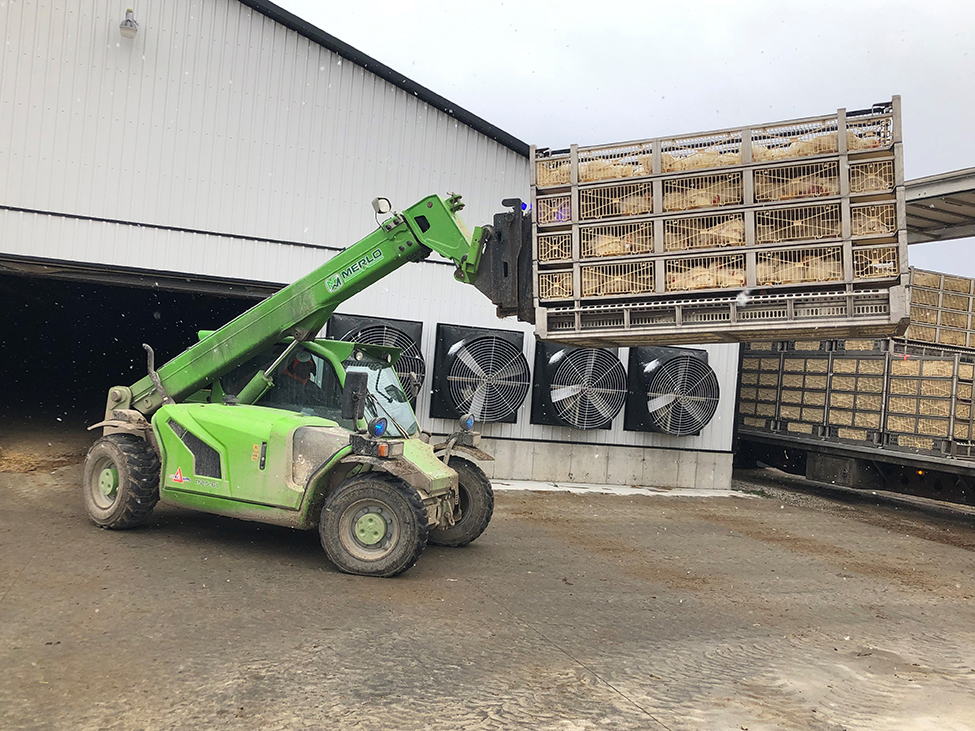
Modèle idéal de nouveau poulailler avec chargement modulaire
Les nouveaux poulaillers à un étage dont le plafond est à une hauteur minimale de 2,7 m (9 pi) sont ceux qui permettent de mieux tirer parti de la technologie du chargement modulaire. L’absence de poteaux de soutien intérieur et la hauteur du plafond facilitent les manœuvres du chariot élévateur. Les opérateurs peuvent placer les modules vides à une faible distance des poulets, ce qui permet aux ramasseurs de charger ces derniers sans trop avoir à marcher. Avec une équipe de six ramasseurs et un chariot élévateur, on peut charger une remorque de 16,2 m (53 pi) en une heure ou moins à partir d’un poulailler d’un seul étage.
Le plafond à 2,7 m (9 pi) donne un dégagement d’au moins 2,4 m (8 pi) entre la litière et le matériel suspendu (conduites d’alimentation, conduites d’eau, capteurs de température et d’humidité, etc.). Idéalement, le matériel fixe comme les conduites de gaz et les appareils de chauffage ou les ventilateurs de recirculation doivent aussi disposer d’un dégagement de 2,4 m (8 pi) vers le bas ou être placés de manière à ne pas nuire au passage du chariot. On doit aussi y apposer du ruban hautement réfléchissant pour en améliorer la visibilité.
Le chariot élévateur est généralement utilisé durant la nuit et dans des conditions de faible luminosité, ce qui complique la visibilité du matériel suspendu. La distribution non homogène de la litière pour également faire rebondir le chariot élévateur lors du transport des modules.
L’entrée de porte du mur du fond doit être d’au moins 2,4 m de hauteur × 3,0 m de largeur (8 pi de hauteur × 10 pi de largeur) afin de faciliter l’accès du chariot. Les poulaillers plus longs que 91,5 m (300 pi) doivent être dotés d’une seconde porte d’accès de mêmes dimensions à l’extrémité opposée du bâtiment. Cette deuxième porte permet de réduire la distance de déplacement du chariot élévateur durant le chargement étant donné que la moitié du bâtiment peut être chargée à partir de chaque extrémité. Le camion doit alors être déplacé à l’autre extrémité du poulailler pour la deuxième partie du chargement. L’opérateur du chariot doit suivre de près le travail de l’équipe de ramassage et apporter les modules vides au bon moment afin que les ramasseurs ne perdent pas de temps à attendre. L’exécution des tâches requiert plus de temps si les distances à franchir sont élevées (>106 m [>350 pi]) ou s’il y a trop de manœuvres à effectuer, ce qui réduit l’efficacité du processus de chargement. L’option de procéder au chargement à la moitié du poulailler est discutée plus loin dans le présent document comme une autre méthode pour réduire les distances à franchir pour le chariot élévateur.
Prévoir une aire de chargement dont la surface dure et de niveau (en béton ou en un matériau équivalent) mesure au moins 16,8 m × 16,8 m (55 pi × 55 pi) pour un poulailler d’une largeur de 15,2 m (50 pi) et qui est immédiatement adjacente à la porte, afin que le chariot élévateur puisse se déplacer et effectuer ses virages durant le chargement des modules dans la remorque et leur déchargement (figure 7). La plate-forme doit excéder le côté du poulailler de 1,5 m (5 pi) afin que la remorque soit stationnée assez loin pour ne pas heurter les ventilateurs de recirculation qui font saillie sur le côté du bâtiment.
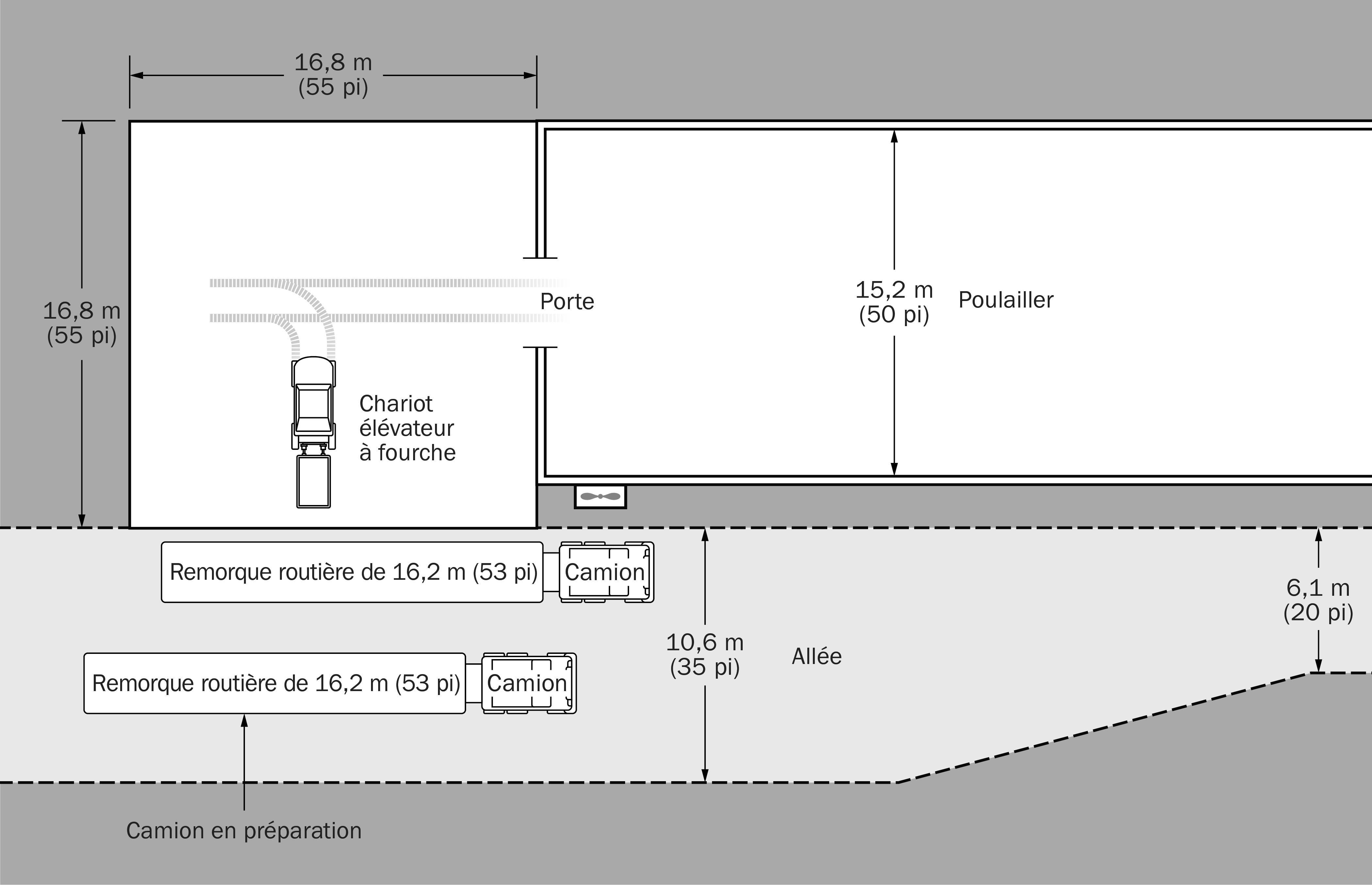
La surface de la plate-forme variera en fonction de la largeur du poulailler. Le tableau 2 présente les dimensions minimales recommandées. Les surfaces qui apparaissent au tableau 2 sont la surface libre exigée pour le déplacement du chariot élévateur et excluent les surfaces utilisées pour empiler la litière des poulets à griller. Le passage entre cette aire de chargement et l’intérieur du bâtiment doit se faire en douceur (c’est-à-dire sans seuils de porte ou dénivellations soudaines), afin de ne pas faire rebondir les modules durant le déplacement du chariot vers l’intérieur ou l’extérieur du bâtiment. Si l’aire de chargement est située à la même extrémité du poulailler que la zone d’entreposage du fumier solide, il peut être nécessaire d’agrandir la plate‑forme afin de s’assurer que la surface sur laquelle le chariot peut effectuer ses déplacements (celle qui ne contient pas de tas de fumier) respecte les minimums mentionnés plus haut.
Largeur du poulailler m (pi) |
Largeur minimale de la plate-forme m (pi) |
Longueur minimale de la plate-forme m (pi) |
---|---|---|
12,2 (40) | 13,7 (45) | 16,8 (55) |
15,2 (50) | 16,8 (55) | 16,8 (55) |
18,2 (60) | 19,8 (65) | 16,8 (55) |
21,3 (70) | 22,9 (75) | 16,8 (55) |
24,4 (80) | 25,9 (85) | 16,8 (55) |
Si l’aire de chargement est faite de gravier compacté, l’entretien de celle-ci est essentiel au déplacement efficace du chariot élévateur. Il ne doit y avoir aucune zone d’accumulation d’eau ni aucun nid de poule, puisque cela réduira grandement la vitesse du chariot élévateur. L’ensemble de la remorque doit être parfaitement de niveau durant le chargement des modules afin que le chariot élévateur puisse s’approcher perpendiculairement de la remorque et placer efficacement le module sur les doigts de positionnement du châssis ou sur le dessus du module inférieur (figure 8).
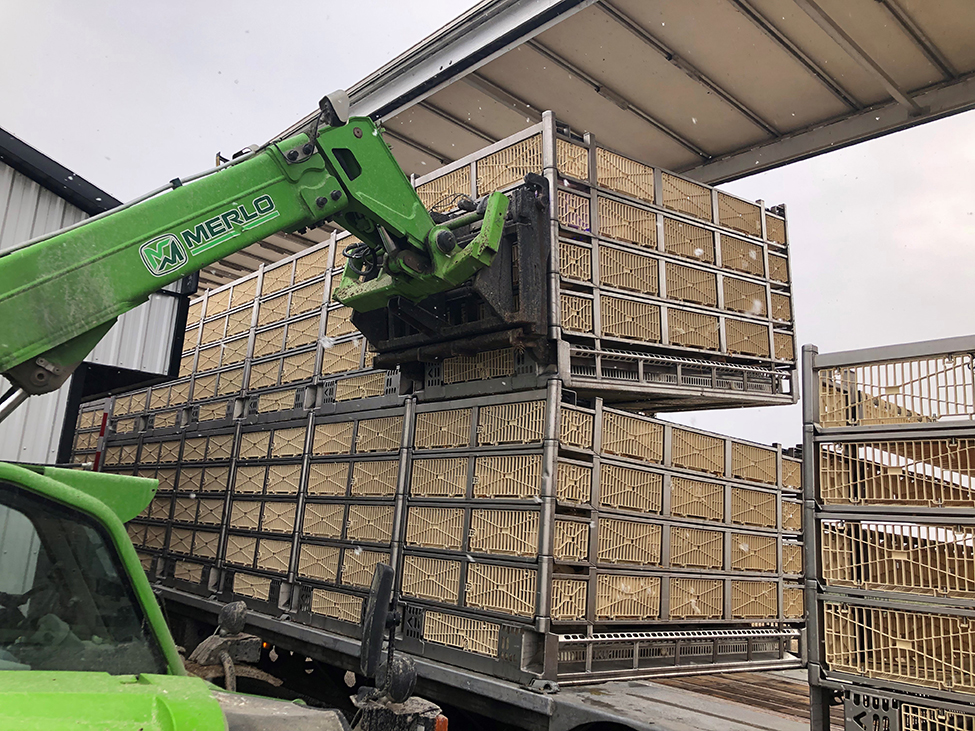
Procéder au chargement à la moitié du poulailler
Dans le cas des poulaillers d’une longueur supérieure à 91,5 m (300 pi), il est possible, au lieu d’installer des portes de chargement avec des aires de chargement à chaque extrémité, d’installer une grande porte au milieu du poulailler sur un des murs du côté. Les dimensions minimales de la porte sont de 3,6 m (12 pi) de long × 2,4 m (8 pi) de haut et il y doit avoir une aire de chargement mesurant 21,3 m (70 pi) de large × 45,7 m (150 pi) de long (voir la figure 9). La taille de la plate-forme doit permettre au chariot élévateur ou au télémanipulateur de virer de 180 degrés lorsqu’il prend un module sur la remorque afin que le conducteur ne remette pas de modules vides dans le poulailler sombre (puisque les lumières sont éteintes durant le chargement nocturne). La longueur de la plate-forme permet à la remorque que l’on charge d’avancer d’une distance équivalant à un module complet afin de minimiser le déplacement latéral du chariot élévateur. Un autre avantage est que cela permet de préparer la remorque derrière celle qui est actuellement chargée afin qu’une fois celle-ci chargée, le chariot élévateur puisse commencer à retirer des modules vides de la prochaine remorque, ce qui minimise les arrêts dans la procédure de chargement. L’allée destinée aux remorques doit être suffisamment large pour permettre à deux remorques de passer l’une à côté de l’autre (afin que la remorque chargée puisse quitter les lieux pendant le chargement de la suivante).
Cette configuration de l’aire de chargement est avantageuse pour les poulaillers avec une ventilation tunnel (avec ou sans blocs refroidisseurs par évaporation), puisqu’elle ne réduit pas la surface du mur d’extrémité disponible pour placer le matériel de ventilation étant donné qu’il n’y a pas de larges portes.
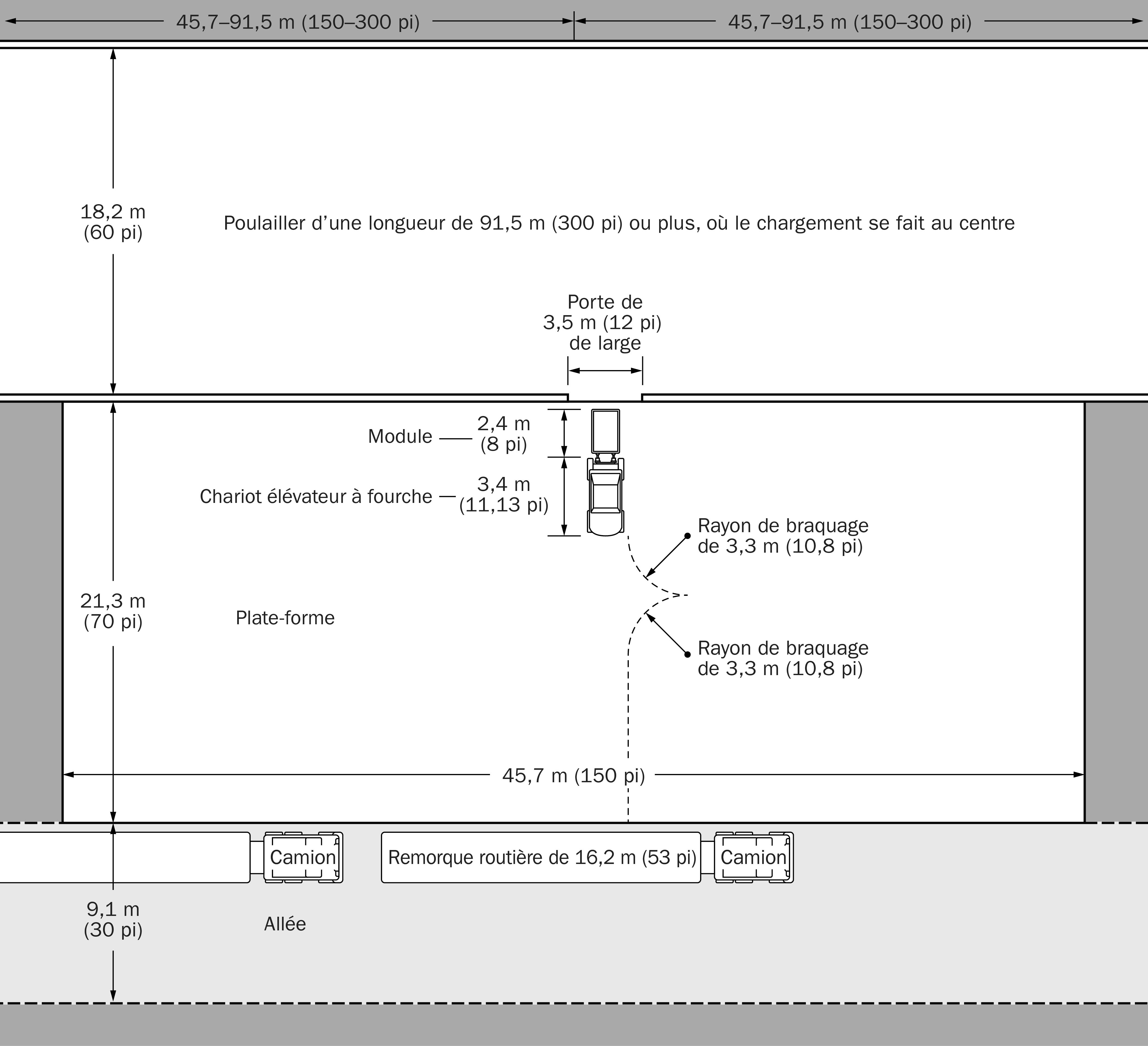
Rénovation de poulaillers afin de pouvoir utiliser le chargement modulaire
Poulailler à seul étage ou rez-de-chaussée de poulaillers à plusieurs étages
Bon nombre de poulaillers plus anciens à un seul étage ont été construits avec des plafonds de 2,4 m (8 pi) de hauteur, offrant ainsi un dégagement de 2,1 m (7 pi) entre la litière et tout le matériel suspendu. Vérifier la hauteur de mât du chariot ainsi que la hauteur de la cabine avant le premier chargement afin de s’assurer qu’il y a suffisamment d’espace libre. La hauteur des chariots élévateurs peut varier selon les marques et les modèles; si on change de chariot, il est donc nécessaire de revérifier l’espace libre disponible.
L’entrée de porte du mur du fond doit être d’au moins 2,4 m de hauteur x 3,0 m de largeur (8 pi de hauteur x 10 pi de largeur) pour faciliter l’accès du chariot. Les poulaillers plus longs que 91,5 m (300 pi) doivent être dotés d’une seconde porte d’accès de mêmes dimensions à l’extrémité opposée du bâtiment ou envisager d’ajouter une porte de chargement au milieu du poulailler sur un des murs de côté. Cette deuxième porte permet de réduire la distance parcourue par le chariot durant le chargement.
Prévoir une aire de chargement dont la surface dure et de niveau (en béton ou une surface équivalente) mesure au moins 16,8 m x 16,8 m (55 pi x 55 pi) et qui est immédiatement adjacente à la porte, afin que le chariot élévateur puisse se déplacer et effectuer ses virages durant le chargement des modules dans la remorque et leur déchargement (figure 7). Le passage entre cette aire de chargement et l’intérieur du bâtiment doit se faire en douceur, c’est-à-dire sans seuils de porte ou dénivellations soudaines, afin de ne pas faire rebondir les modules durant le déplacement du chariot vers l’intérieur ou l’extérieur du bâtiment.
Malheureusement, certains poulaillers ne pourront jamais utiliser le matériel de chargement modulaire en raison de restrictions touchant les lieux ou du coût prohibitif de leur rénovation.
Au rez-de-chaussée des poulaillers ayant plusieurs étages, la circulation se fait habituellement au milieu du bâtiment entre les rangées de poteaux. En situation idéale, les poteaux sont suffisamment espacés pour que l’opérateur du chariot puisse introduire les modules dans les ouvertures entre les poteaux sur les côtés opposés à l’allée de passage (figure 10). Si l’espacement entre les poteaux ne permet pas cette manœuvre, il faudra avoir recours à une autre façon de fonctionner.
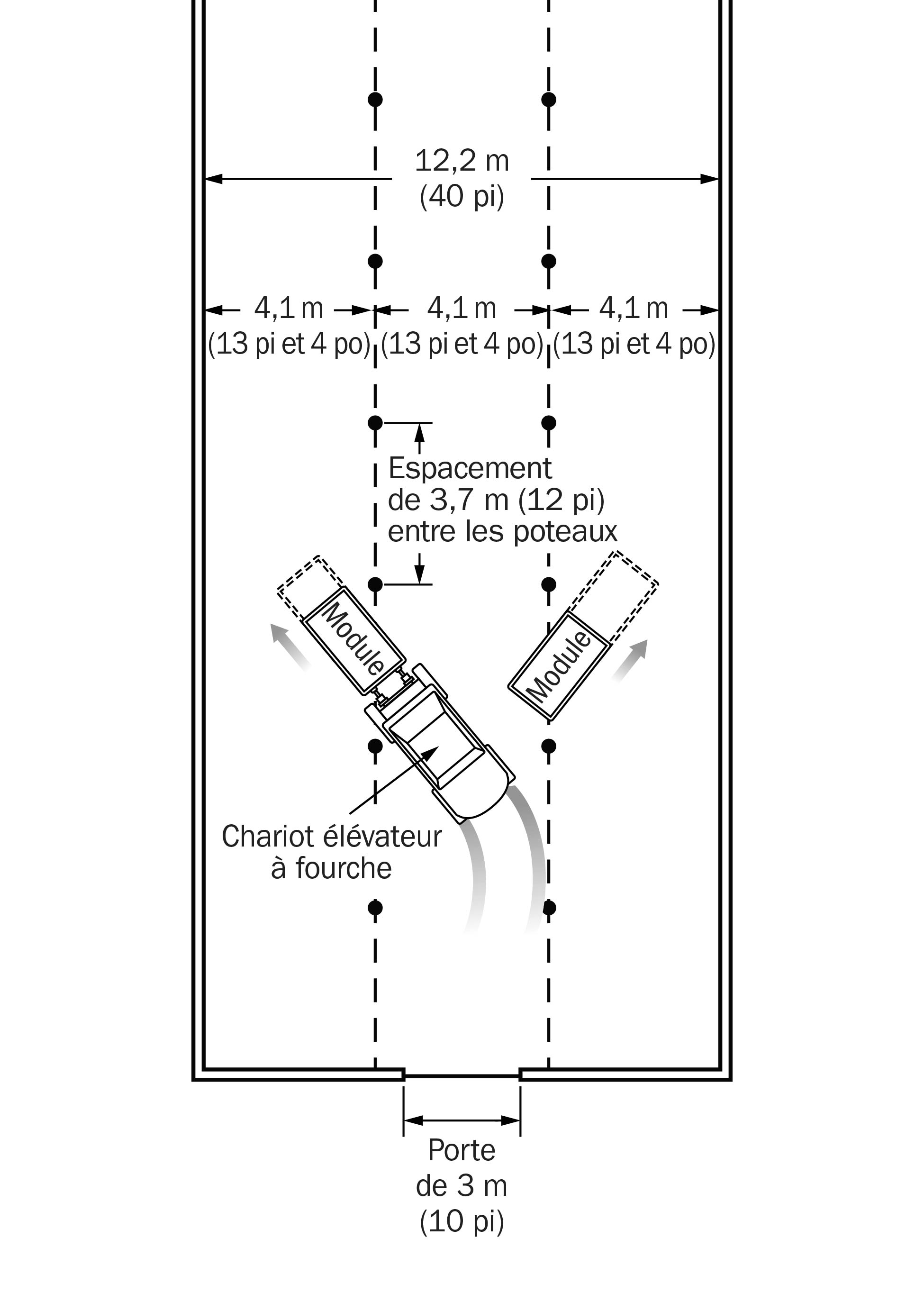
Deuxième étage – Chargement par une porte latérale
Pour effectuer le chargement des modules par une porte latérale, on doit élargir et aménager l’allée extérieure le long d’un côté du poulailler (sur l’axe le plus long). Cette allée de 10,7 m (35 pi) de largeur, où les camions peuvent circuler en toute saison, est nécessaire pour que le chariot élévateur ou le télémanipulateur dispose de suffisamment d’espace pour effectuer ses manœuvres. Le chariot ou le télémanipulateur doit être en mesure d’arriver à la porte du poulailler en droite ligne afin de placer le module dans l’entrée sans heurter les côtés de la porte (figure 11). Cette allée devra être entretenue toute l’année et aménagée avec une pente en vue d’empêcher la formation de flaques d’eau; par ailleurs, la neige devra être retirée pour que le chariot ou le télémanipulateur puisse fonctionner dans toutes les conditions météorologiques.
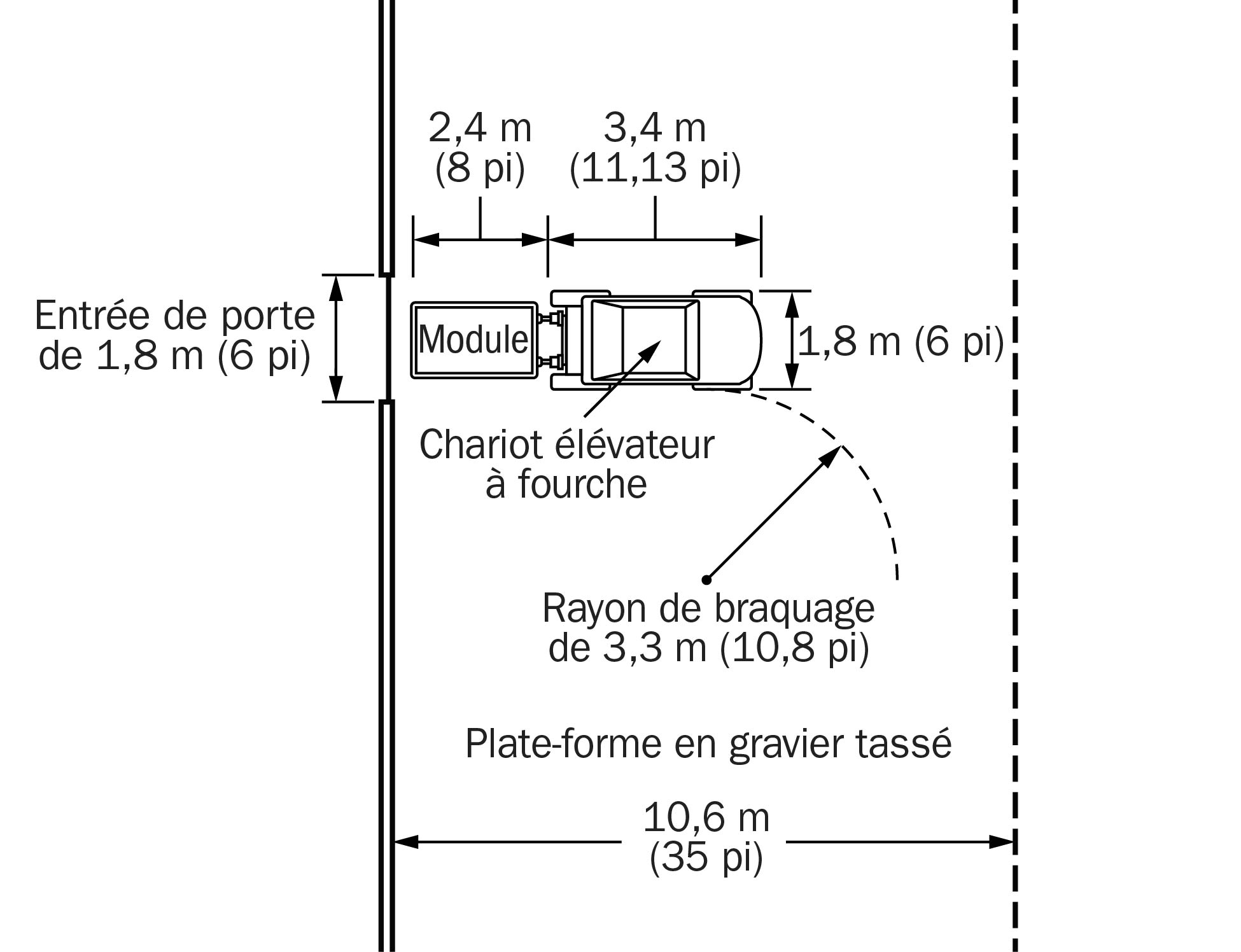
Pour effectuer le chargement par une porte latérale, on doit retirer les rampes de chargement en place à l’extérieur du poulailler et agrandir les portes existantes pour qu’elles mesurent au moins 2,1 m de hauteur x 2,1 m de largeur (7 pi de hauteur x 7 pi de largeur). Cela permet au chariot ou au télémanipulateur de placer les modules au deuxième étage en maintenant l’espace existant de 15,2 m (50 pi) entre les portes. L’élargissement de l’entrée de porte peut exiger une relocalisation ou une modification du matériel de ventilation (ventilateurs d’évacuation ou bouches d’entrée d’air) selon l’aménagement du poulailler. Évitez d’installer des garnitures métalliques autour du bas des portes puisque les chariots pourraient les endommager durant la manipulation des modules du deuxième étage. Considérez cette porte comme s’il s’agissait d’un quai de chargement. Envisagez aussi d’installer des bordures de trottoir au niveau du sol pour empêcher les roues avant du chariot élévateur ou du télémanipulateur de s’approcher de trop près du poulailler et d’endommager le bardage.
Il est préférable qu’il n’y ait pas de seuils dans le bas des entrées de porte afin de ne pas nuire au déplacement des modules qui sont chargés ou déchargés au deuxième étage. Dans le cas contraire, il sera peut-être nécessaire d’ajouter un panneau temporaire de contreplaqué renforcé sur la plate‑forme afin que le module soit suffisamment haut pour que les chariots puissent avoir accès aux fentes sur le module (figure 12).
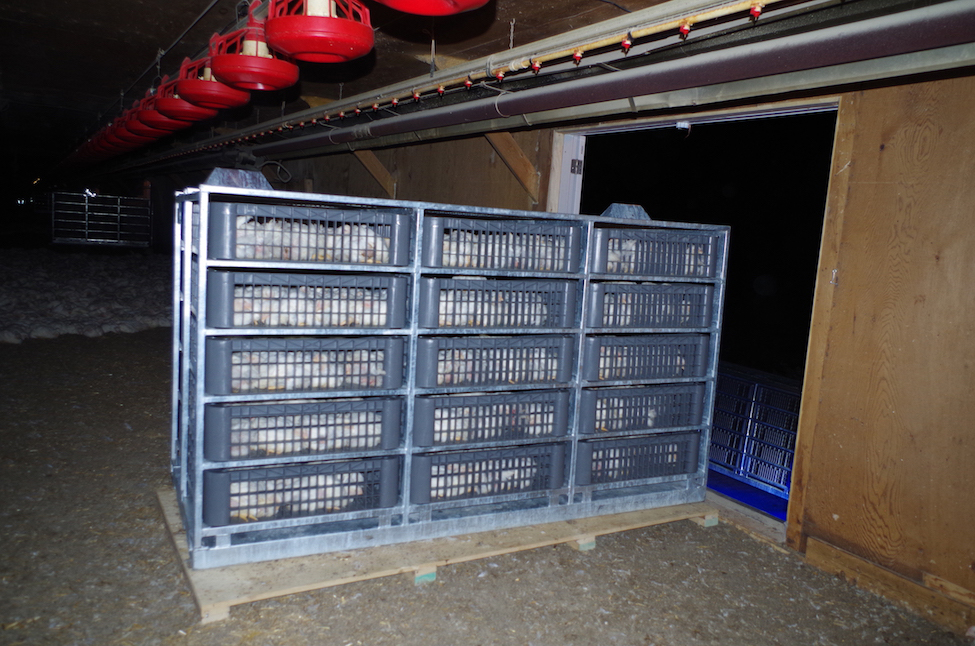
La structure du plancher du second étage, dans le voisinage immédiat des portes de chargement, devrait être inspectée par un ingénieur spécialisé en structure. Toutes les réparations ou améliorations doivent être effectuées avec l’objectif de soutenir une charge répartie mobile minimale de 4,30 kPa (90 lb/pi2). Cela représente le poids maximal en charge du module double de marque Meyn Maxiload placé sur le plancher, ce qui correspond à une charge de plancher considérablement plus élevée que ce qui est actuellement requis par le Code national de construction des bâtiments agricoles, 1995, pour le tracteur effectuant le nettoyage plus la litière.
Autres facteurs concernant le site
Parc de stationnement pour le camion du personnel et la remorque du chariot élévateur — Ces éléments sont beaucoup plus larges que les anciennes fourgonnettes pour le chargement des cageots. Les exploitations devront conserver un parc de stationnement pour accommoder un camion gros porteur supplémentaire qui ne nuit pas aux camions de transport de la volaille qui arrivent ou quittent les lieux durant le chargement.
Zone de préparation pour les camions de transport de la volaille qui attendent d’être chargés.
Les camions de transport doivent entrer en avançant sur le terrain de l’exploitation. Il est interdit de faire marche arrière. n devrait avoir une zone de préparation permettant d’accueillir au moins une remorque de transport, afin que le chauffeur puisse retirer les sangles et commencer la préparation de la remorque. Les chauffeurs ne devraient pas avoir à se stationner sur le bord de la route la nuit pour des raisons de sécurité.
Selon la configuration du bâtiment, la cour ou l’allée doit être suffisamment large pour permettre à des remorques de 16,2 m (53 pi) d’effectuer un virage sur le terrain de l’exploitation afin qu’elles puissent sortir en marche arrière lorsqu’elles sont chargées. Il devrait y avoir suffisamment d’espace pour manœuvrer au moins deux camions en même temps sur la propriété.
Résumé
La mise en place d’un système de chargement modulaire dans le poulailler relève de l’entreprise de transformation qui fait affaire avec l’exploitant. C’est elle qui décidera du bon moment pour passer à ce système et qui choisira le matériel. La présente fiche technique explique les modifications qui pourraient devoir être apportées aux installations existantes pour vous aider à comprendre les changements nécessaires afin d’utiliser ce matériel. Si vous planifiez construire un nouveau poulailler, la fiche technique contient aussi des détails dont vous devriez tenir compte dans votre planification afin d’accommoder le chargement modulaire.
Références
Plan d’activités et de transition : Manipulation modulaire des poulets dans l’industrie du poulet de l’Ontario. Association of Ontario Chicken Processors (2010).
Cette fiche technique a été rédigée par Al Dam, spécialiste provincial de l’aviculture, MAAARO, Guelph; Daniel Ward, ingénieur, équipement et structures pour volailles, MAAARO, Stratford; Sabrina McDonald et Amanda Bordin, adjointes de recherches, secteur de l’aviculture, MAAARO, Guelph.