On-farm generators for emergency use
Learn how to plan and size a generator system, purchase a suitable generator and how to operate a generator to produce high-quality power. This is technical information for Ontario producers.
ISSN 1198-712X, Published June 2020
Introduction
We all depend on a constant supply of electricity and often take this for granted — until a power outage occurs. Farmers with cows to milk, livestock to feed or crops/produce in storage can face significant economic loss if power is lost. Protect your farm with an emergency back-up power system for when the lights, and everything else, goes out.
Every farm can benefit from an emergency generator. A generator helps prevent economic loss and protects valuable production by ensuring a stable power supply in emergencies. Whether the farm has livestock, crops/produce in storage, or production needing power to operate (e.g., milking machines), a generator should be a critical part of every emergency management plan.
Use this factsheet to plan and size a generator system, purchase a suitable generator and operate the generator to produce high-quality power.
This factsheet is not intended to replace specific information or professional advice supplied by manufacturers, distributors and licensed electrical contractors, nor does it supersede the Ontario Electrical Safety Code.
Be disaster ready
Ontario’s electricity system is usually reliable. However, extreme events can happen. The ice storm in December 1998 and the blackout in July 2003 cut power to millions of people for days and even weeks, leaving many farmers in the dark.
Prepare for these extreme events by creating a farm-wide emergency management plan. Review each operation on the farm and determining the impact of a power outage. What will happen if power is lost:
- for one hour?
- for one day?
- for one week?
- in the dead of winter?
- in the heat of summer?
Will livestock get their feed and/or water, or have enough heat and/or ventilation to survive? Will products in storage (e.g., feed, grain, produce) start to spoil? Will there be damage to buildings (e.g., frozen pipes)?
Minimize these risks by installing a generator. Many insurance companies require permanently installed generators for certain types of farm operations (e.g., poultry, swine).
Types of generators
Two main types of generators are used on farms, driven either by a self-contained diesel, gasoline or natural gas engine, or powered by a tractor PTO (power takeoff).
A self-contained engine-driven generator (Figure 1) is:
- usually permanently installed, but can be portable
- quiet and fuel-efficient
- able to be switched on quickly (usually, automatically)
- able to operate for long, continuous periods
- often sized for all the electrical loads on the farm - known as a full electrical load system
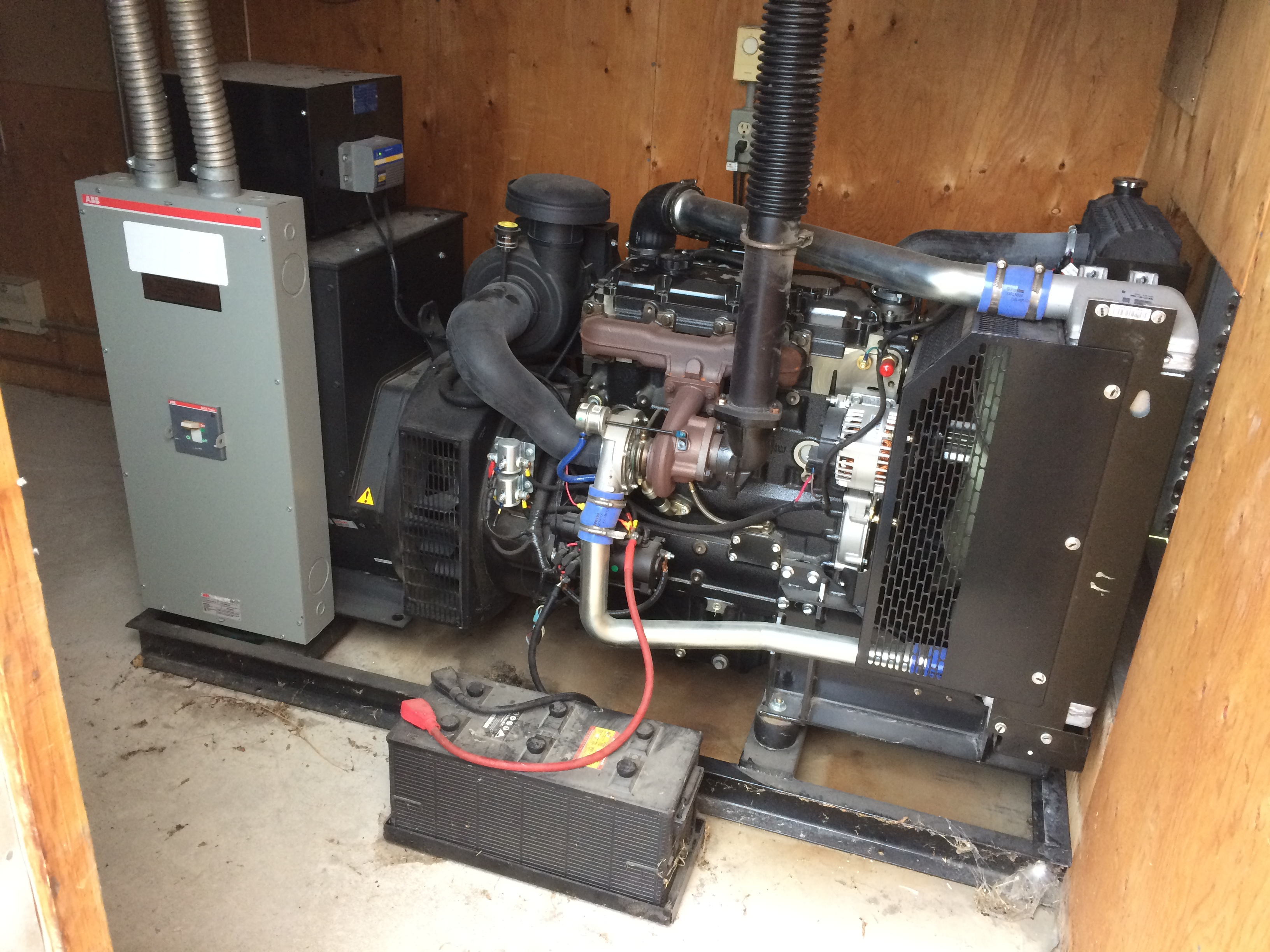
A portable, tractor PTO–driven generator (Figure 2) is:
- lower cost (approximately half the price per kilowatt of output power)
- easier to maintain
- able to be moved to different locations
- often sized for only critical equipment (e.g., milking equipment, heaters, fans) — known as a part electrical load system.
- must be manually connected and started during a power failure
- may not be accepted by insurance companies
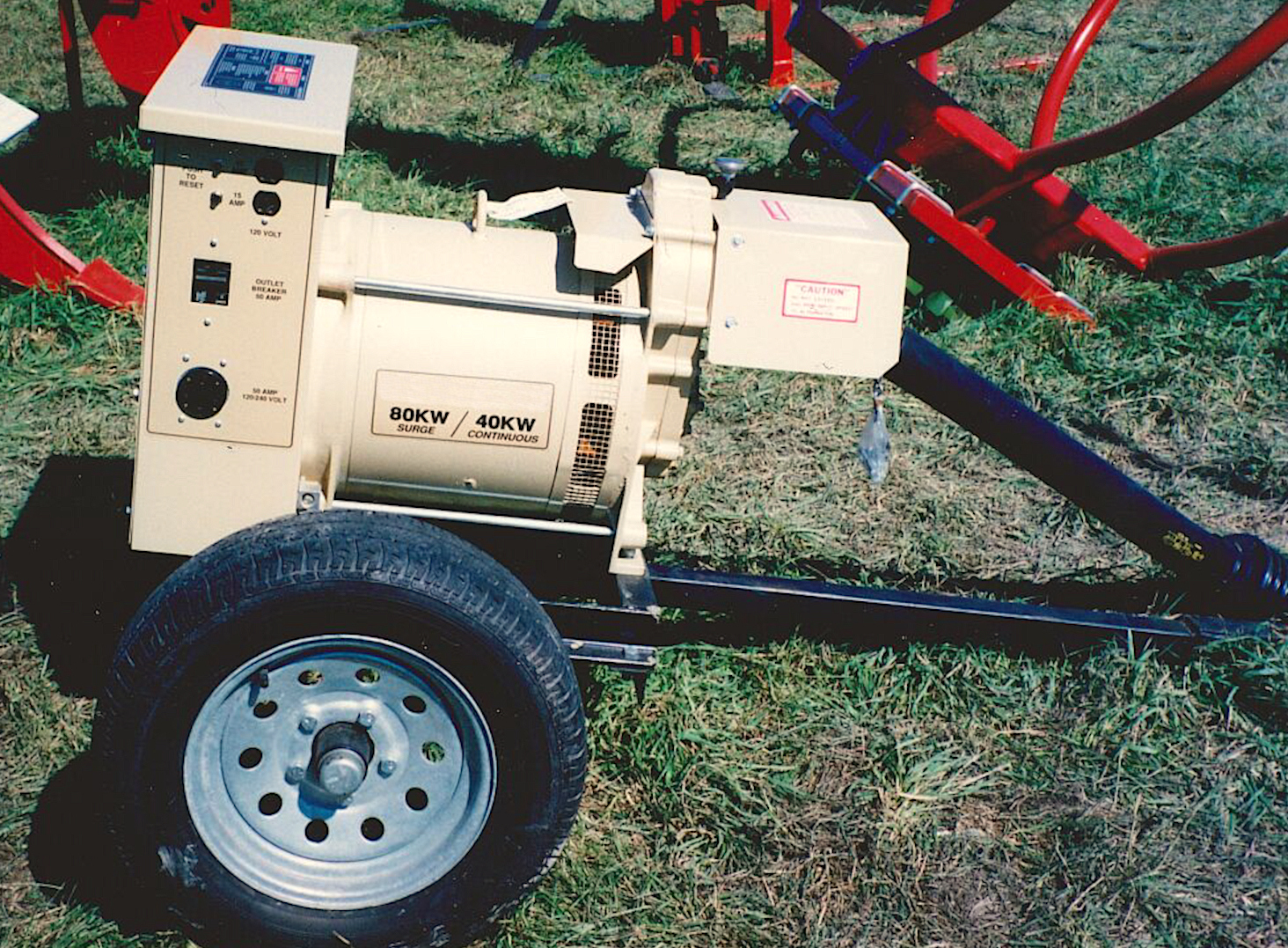
Assess the critical operations on the farm to determine whether a permanent or portable generator and whether a full load or part load system are needed. Be sure to speak with your farm insurance company; their requirements may dictate the type of system needed.
Sizing the generator
Generator sizing method
To estimate the size of generator needed, follow these four steps:
- Make a list of all motors and electrical devices that will be powered by the generator.
- For a full electrical load system, list everything connected to the power system.
- For a partial electrical load system, list only the critical loads that need to be powered by the generator.
- For each motor and electrical device, write down both the operating and start-up loads, in watts (see Table 1 to convert from horsepower). Check motor nameplates for this information and/or consult with a licensed electrician.
- For motors, use at least four times the operating watts to determine the start-up watts. This can range from two to twelve times in extreme cases. For example, a silo unloader buried in silage or a stable cleaner buried in manure will require more start-up power than if each is free and clear of materials.
- For heaters and lights, start-up watts are equal to operating watts.
- Add up all the operating loads in the list. Separately, add up all the start-up loads.
- If any motors or devices will never run at the same time, only include the largest load(s) (e.g., a silo unloader and stable cleaner may never run at the same time, so include only the largest load).
- For a partial electrical load system, determine in what order the loads will be started. In order, add the start-up watts for the next load to the operating watts of the loads already running. Whichever step has the highest peak will determine the maximum load.
- Add 20% for future expansion. Round the final totals up to the nearest 5 kW.
Choose a generator with a continuous rating larger than the total operating load and a peak rating or surge rating larger than the total start-up load. Often, the start-up load (not the operating load) will dictate the final generator size.
Motor size | Start-up watts (assumed 4x operating) | Typical operating watts |
---|---|---|
1⁄2 HP | 2,300 W | 575 W |
3⁄4 HP | 3,200 W | 800 W |
1 HP | 4,300 W | 1,075 W |
2 HP | 7,400 W | 1,850 W |
3 HP | 12,300 W | 3,075 W |
5 HP | 18,200 W | 4,550 W |
71⁄2 HP | 27,000 W | 6,750 W |
10 HP | 36,000 W | 9,000 W |
Compiled by Enertech Solutions Inc. for the Ice Storm Recovery Assistance Program 1999.
Generator terminology
Generators are available from a number of manufacturers, in many sizes, with a wide range of features. Always review features with the generator supplier and a qualified electrician to ensure the generator meets the farm’s requirements.
Common generator terms and features
- Continuous rating
- The amount of wattage the generator can supply on a continuous basis (a few hours at a time, not 24 hr/day indefinitely). Generators built to higher quality standards (e.g., heavy duty) would be expected to run for longer periods of time.
- Peak rating
- The amount of wattage the generator can supply for short periods (from 2 or 3 seconds up to 5 or 10 minutes every hour)
- Surge rating
- The amount of wattage the generator can supply for a very short time (e.g., when starting an electric motor). Smaller portable generators often do not quote or support a surge rating.
- Run time at specified load
- An estimate of how long the generator will run at the specified load (e.g., 8 hr @ 50% load).
- Voltage regulator
- Maintains the output voltage as the load and/or engine speed (frequency) change. Voltage regulation is stated as ± (plus/minus) a percentage above or below the rated voltage. Without this, voltage can vary by ±15% to 20%. If there will be significant variation in loads, sensitive electrical equipment or long generator running time, voltage regulation in the ±2% to 5% range may be worth the extra cost.
- Voltmeter
- Measures generator output to ensure the voltage produced is within acceptable range. Electrical equipment can be damaged by voltage too high or too low.
- Frequency meter
- Measures frequency in Hertz (Hz). Adjust generator speed to keep frequency at or close to 60 Hz for optimum voltage output.
- Governor
- Keeps the engine at or near the correct speed to maintain electrical power at 60 Hz and produce proper voltage levels.
- Automatic idle control
- Reduces engine speed to conserve fuel when all electrical loads have been turned off. Attention: review usage and monitor voltage carefully before activating this feature. Motors can be damaged when starting if the generator does not respond quickly enough. Small electrical devices (e.g., thermostats, clocks) may not draw enough power to initiate the generator.
- Insulation class
- Identifies the maximum allowable operating temperature of the windings. Generators and engines produce considerable heat and units built to higher insulation ratings will usually carry a premium price. Ventilate the generator properly to stay within the proper operating temperature.
Installing an emergency generator
Install and secure the generator
Permanently installing a generator provides a secure, protected system that will operate reliably for a long time.
- Anchor the generator on a 150-mm (6-in.) thick concrete pad.
- Use rubber bushings between the generator and the concrete pad.
- Operate in a dry location with shelter from direct and/or driving rain or snow.
- Have a licenced electrical contractor install all electrical connections.
- Incorporate a transfer device to automatically activate the emergency generator during a power failure.
- Provide sufficient ventilation to prevent generator over-heating. Install inlet and outlet air openings of at least 500 cm2 or 0.5 ft2 for each 1 kW of generator capacity.
- Direct all exhaust fumes outdoors.
- Keep generator motor exhaust away from flammable materials.
- Keep the generator fuelled up at all times.
Portable generators must be moved and connected to the power system every time there is a power outage.
- Park the generator in a convenient and easy-to-access place while in storage.
- Do not position the tractor and generator near flammable materials.
- Use a tractor with 2 brake horsepower per 1 kW of generator electrical output.
- Keep the tractor fuelled up at all times. Remember that both the on-farm fuel tank pump and the block heater may not operate in a power failure.
- Use a wide trailer with strong axle(s) to prevent the generator flipping under load.
- Use only the PTO shaft purchased with the generator.
- Ensure the PTO shaft is straight, proper length and strong enough to transmit the required horsepower.
- Operate with the PTO shaft as short as possible.
- Align the PTO shaft correctly (Figure 3).
- Keep all PTO shields in place and in good repair.
- Direct the tractor exhaust outdoors, if running inside a building.
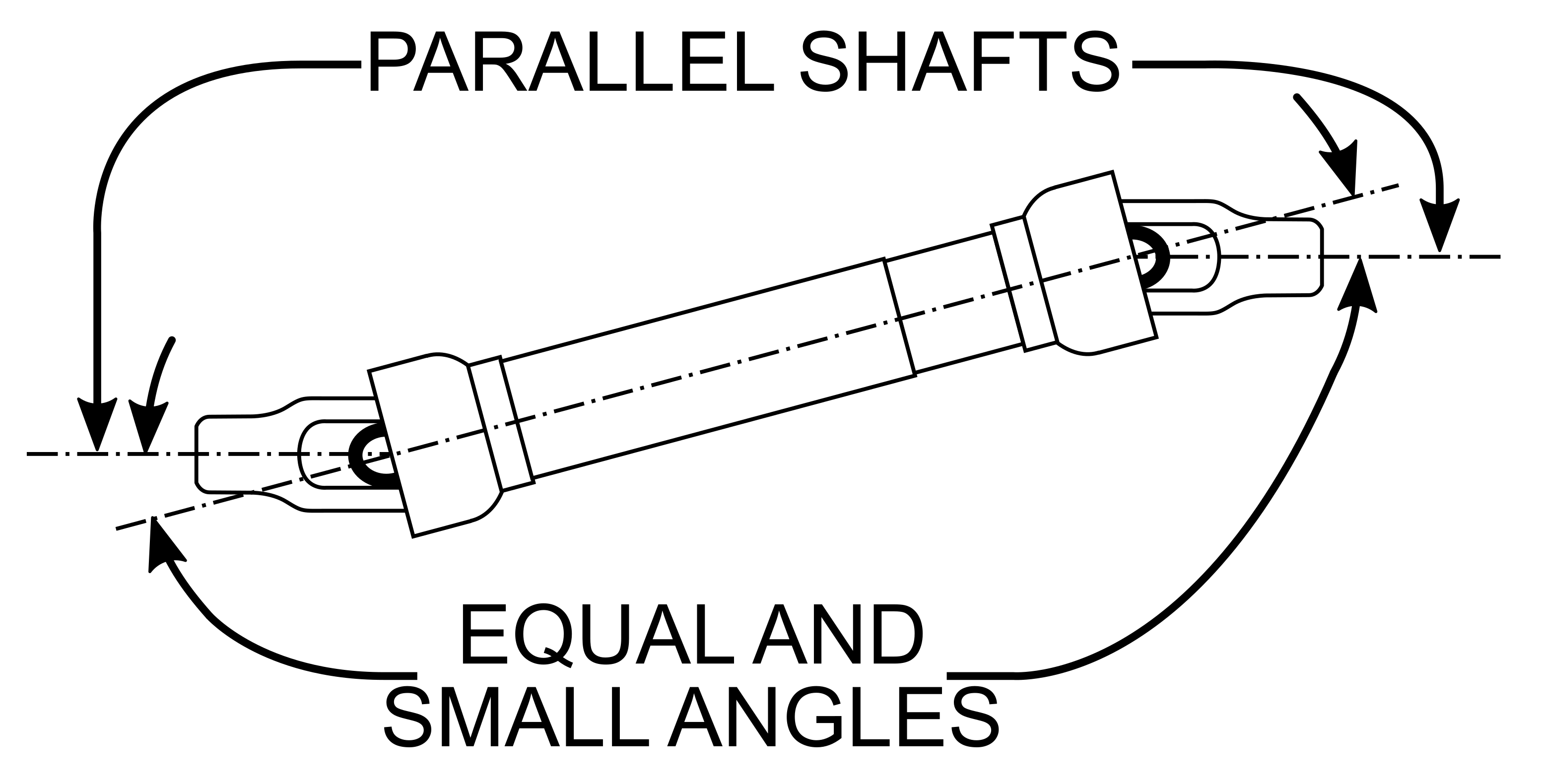
Connecting to the power system
Always use qualified personnel to initially connect and test generators. Use a properly sized cable based on generator size and cable length. Contact the generator supplier or an electrical contractor for the proper equipment and always have a licensed electrician install the generator.
Use a transfer device
Always use a qualified electrician to install and connect the transfer device. A transfer device or transfer switch must be used to disconnect the farm power system from the power lines, when the generator is in use (Figure 4). Transfer devices must be sized according to the Electrical Safety Code. These devices prevent:
- feedback into the power supply line from the generator
- accidental re-energizing of the farm or home service system
- burnout of the generator, when regular service is restored
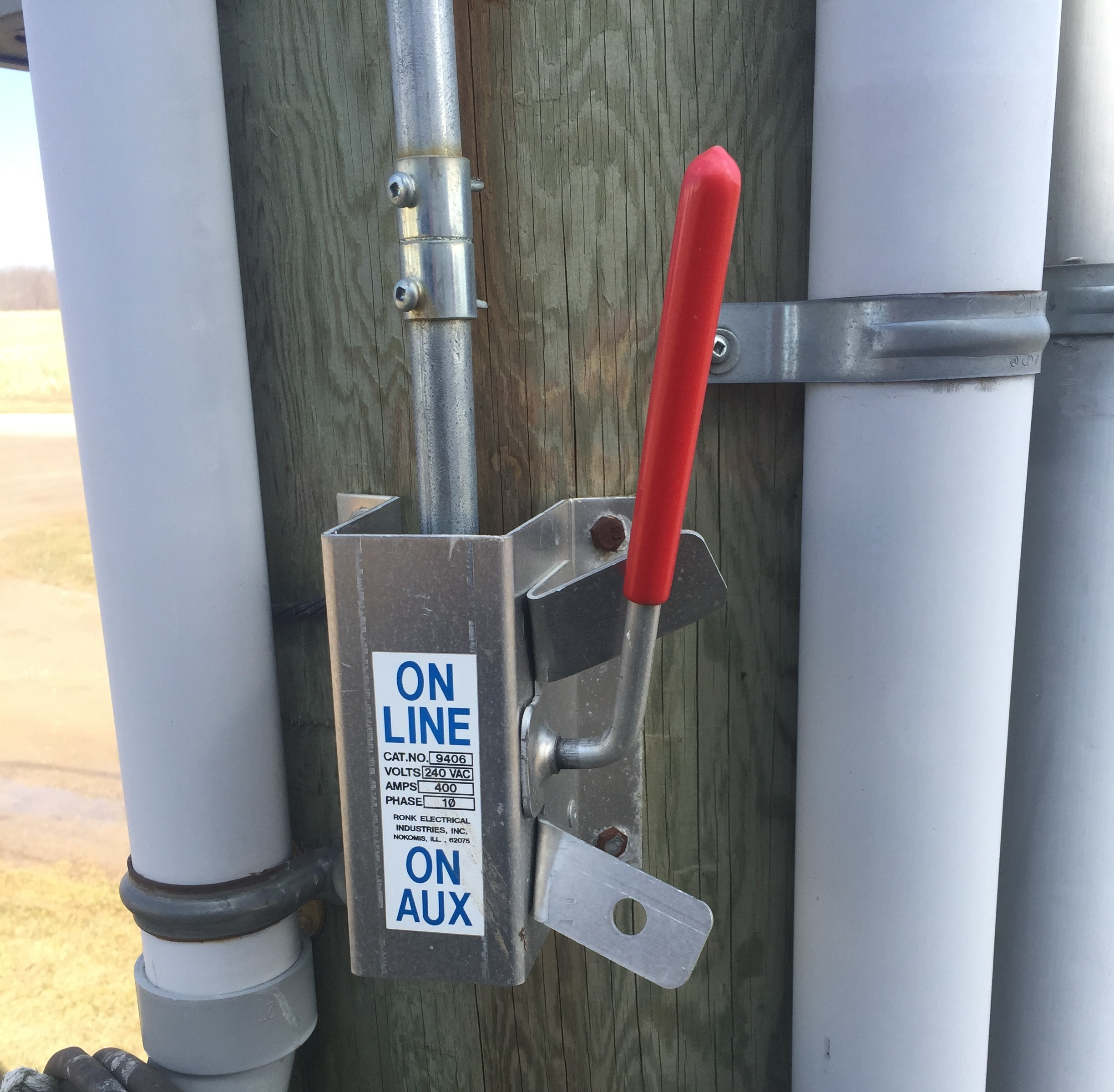
Operating an emergency generator
Starting the generator
Follow these steps to ensure the generator starts safely and will operate smoothly:
- clearly identify all circuits on all electrical panels
- follow the generator manufacturer’s instructions (see owner’s manual; may also be listed on the side of the generator)
- disconnect or turn off all loads before starting the generator (e.g., all motors, lights, hot water heaters, heating cables and heated water troughs)
- once the generator is running, turn on motors one at a time
- reconnect other loads slowly after essential motors are running
Operating the generator
Generators operate best under constant load (e.g., not switching motors on and off frequently).
- Run the system at 80% capacity or less, if possible.
- Generators may handle short-term heavy loads, but not for long periods.
- If the circuit breaker on the generator trips, reduce the loading.
- Monitor voltage and adjust speed to maintain voltage at the generator.
- Check total loading with an amp-meter and compare it to the generator’s specifications.
- Keep fuel on hand for at least 72 hr. (During the 1998 Ice Storm, farmers reported using an average of 160 L of fuel daily, with some as high as 400 L.)
For tractor PTO–driven generators:
- don’t assume the tractor’s tachometer is correct. Calibrate with a hand-held tachometer or through a tractor dealer
- know the engine rpm required to deliver 540 (or 1,000) PTO rpm and set to that reading
- monitor the tractor for coolant leaks, oil leaks or fan belt breakage
- use automatic shutdown systems (e.g., Murphy switches) to prevent damage in case of: high coolant temperature, low coolant level, low oil pressure, low oil level
- always shut off the tractor and generator when lubricating, checking connections or fueling
- make sure the generator gearbox and grease joints have proper lubrication
Producing high-quality power
Power quality problems appear when voltage, current or frequency are unstable. This leads to failure or mis-operation of equipment. Wiring issues within the facility itself (especially grounding and bonding) are almost always to blame. Have a licensed electrician inspect all wiring and ground connections annually.
Use an independent voltage and frequency meter to monitor generator power output. If the generator has one on board, make sure it works. In testing, 20% of portable generators had no meter or a non-working meter and over 85% had no frequency meter (Table 2).
For PTO-driven generators, follow these steps to improve power quality:
- adjust tractor speed to maintain a frequency between 60 and 62 Hz
- ensure the throttle is free enough to make fine adjustments, but firm enough to hold for hours of unattended operation
- set high-idle to the correct value to maintain proper speed at full loads
- check throttle and governor linkage for wear. Excessive wear can affect high-idle settings and governor response to load changes
- turn off the cab air conditioning when operating a generator. The compressor can change the frequency by ±1%
- running a generator faster will not produce more power, but it may damage it
Identify power quality issues
In the aftermath of the 1998 ice storm, OMAFRA completed testing and evaluation of 84 tractor PTO–driven generators. A portable load cell simulated typical farm electrical power loads. Table 2 lists the most commonly identified issues.
Problem identified | Results (% of tests) |
---|---|
No generator operator’s manual | 31.0% |
Tractor tachometer not working | 7.1% |
Tractor tachometer not accurate | Actual PTO speed varied by up to 16% |
Tractor throttle issues | 7.1% |
PTO hook-up issues | 8.3% |
Improper generator running locations | 7.1% |
No generator voltage meter | 9.5% |
Generator voltage meter not working | 6.0% |
Generator voltage meter variation >10% | 3.6% |
No generator frequency indicator | 85.7% |
Never operate at half engine speed
Tractor engines produce optimum horsepower and torque at a specific engine speed. Never operate a tractor with a 1,000-rpm PTO at half engine speed to run a 540-rpm PTO generator. The torque will be unstable, and the tractor may stall or the speed may cycle erratically up and down.
Maintaining an emergency generator
Service the generator regularly to ensure it is ready to operate in an emergency. Consult the generator owner’s manual for regular maintenance items and schedules. See the OMAFRA factsheet, On‑Farm Generators: Operating Safely, for a detailed maintenance plan.
Cover all openings into the generator with 5-mm (1⁄4-in.) galvanized wire mesh to prevent damage by mice or rats while not in use.
Before each use, inspect the generator for:
- loose or broken wires
- defective connections
- missing, corroded or damaged fasteners and other hardware
- low oil levels and/or oil leaks in gearbox
- general appearance and cleanliness
At regular intervals, have a qualified generator servicing business perform periodic inspection and maintenance, checking for:
- condition and operation of brushes
- defective internal wires, connections and other components
- effectiveness and adjustment of voltage regulation
- accuracy of meters
Every 3 months, operate the generator under at least 50% load. This ensures the generator works when needed, keeps components dry with the heat produced and eliminates flat spots on the bearings. Measure voltage, amps and frequency, and keep records of these tests. See the OMAFRA factsheet, On-Farm Generators: Operating Safely, for a detailed log sheet to record regular tests.
On generators with self-contained engines, replace or use the fuel supply every 3 months to prevent moisture condensation in the tank. Add fuel stabilizer/conditioner to prevent fuel deterioration. Keep the fuel tank full at all times - emergencies happen when least expected.
Generator safety
Working with electricity can be dangerous. Generators can pose serious safety hazards to people and livestock. Mistakes happen when people are tired, in a hurry or under stress. Mistakes can be fatal to those using the generator and to those working on the power lines. Always follow all safety instructions provided by the manufacturer and required by the Ontario Electrical Safety Code and other relevant safety standards.
- Never use portable generators indoors where people reside or work, because of the risk of carbon monoxide poisoning.
- Keep children and others away from the generator.
- Keep flammable materials away from the generator, exhaust pipes and tractor (if used) during operation.
- If the generator is used inside a building:
- provide sufficient air for ventilation of excess heat
- direct all exhaust piping outdoors
- keep exhaust pipes at least 15 cm (6 in.) away from combustible materials
- Do not remove radiator caps when engines are running.
- Tractor-driven PTO generators must be securely mounted; a PTO can produce enough torque to spin the whole generator.
- Always keep PTO shields in place.
- Keep an eye on the tractor’s gauges and use an automatic shutdown system.
Summary
Safely operated emergency generators prevent economic loss from power outages and protect production, workers and infrastructure. Assess the farm’s risk from power loss, especially for livestock or sensitive products. Prepare a farm-wide emergency management plan to deal with extended power outages and consider whether a generator is the right solution.
Always hire a licensed electrical contractor to install and wire the generator system properly, and ensure the system meets all Electrical Safety Code requirements. Read the generator operator’s manual and understand how to safely operate and maintain the system. Follow all maintenance requirements and exercise the generator every 90 days to ensure it is ready for the next power outage.
This information has been compiled from data and observations collected during on-farm testing and in consultation with the generator industry. It is not intended as a substitute for the professional advice from manufacturers, licensed electrical contractors or generator suppliers.
This factsheet was revised by James Dyck, P.Eng., Engineering Specialist, Crop Systems and Environment, OMAFRA, Vineland, and Steve Clarke, P.Eng., Engineering Specialist, Energy and Crop Systems, OMAFRA, Kemptville, and reviewed by John Van de Vegte, P.Eng., Engineering Specialist, BMP Technical Integration and Transfer, OMAFRA, Elora, and Jim Zyta, Vice President Loss Prevention, Heartland Farm Mutual, W