Constructing an earthen liquid nutrient storage facility for agricultural source materials
Learn about the legal requirements and factors to consider when expanding or constructing a permanent liquid nutrient storage facility made of earth for agricultural source materials. This technical information is for Ontario livestock producers.
ISSN 1198-712X, Published December 2021
Introduction
A permanent liquid nutrient storage facility made of earth, also referred to as an earthen liquid nutrient storage facility, is a relatively inexpensive way of storing liquid agricultural source material (ASM) if the soil conditions at the site are suitable.
Under the Nutrient Management Act, 2002 (NMA), new and expanding liquid nutrient storage facilities on farm units that generate more than 5 nutrient units of manure annually must meet minimum siting and construction standards as specified in Part VIII of O. Reg. 267/03 (the regulation).
This fact sheet provides a general description of the legal requirements under the regulation and other key factors to consider when expanding or constructing a permanent liquid nutrient storage facility made of earth for ASM. Figure 1 shows an example of an earthen storage facility.
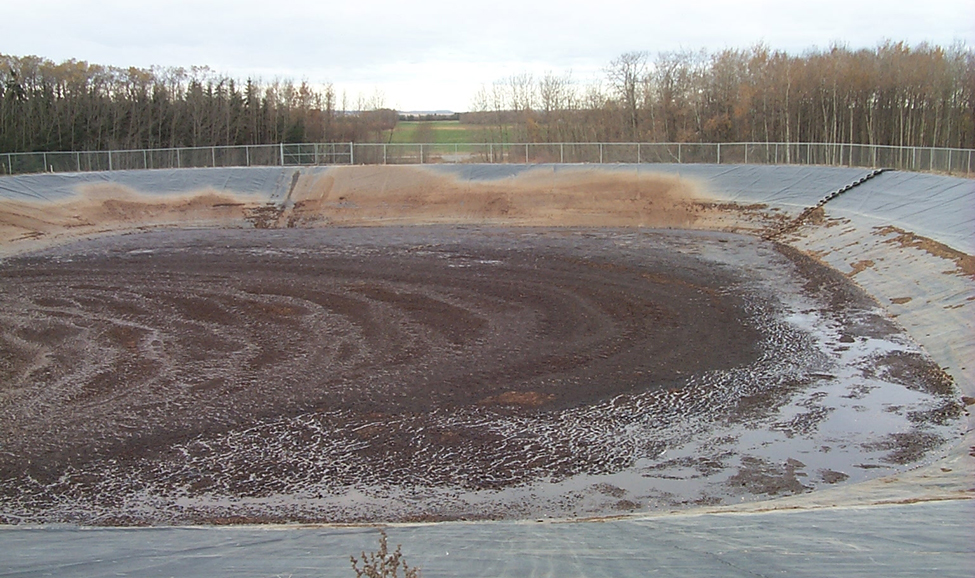
Under the regulation, permanent liquid nutrient storage facilities are structures that have:
- 14 or more days of storage capacity, or
- a depth of liquid nutrients of 100 mm or more
Liquid nutrients include agricultural and non‑agricultural source materials that have a dry matter content of less than 18% or have a slump of more than 150 mm using the slump test referenced in the regulation. ASM include:
- manure produced by farm animals
- runoff from animal yards and solid manure storages
- washwater from agricultural operations that have not been mixed with human waste
Non-agricultural source materials (NASM) include:
- pulp and paper biosolids
- sewage biosolids
- materials that are not from agricultural sources that can be applied to land as a nutrient, such as washwater and organic residues from food processing plants
Anaerobic digestion material is a liquid nutrient that can be an agricultural source material or non‑agricultural source material, depending on the material treated in the digester. Anaerobic digestion material that meets all the following criteria is considered an agricultural source material:
- the anaerobic digestion materials were treated in a mixed anaerobic digestion facility
- at least 50%, by volume, of the total amount of anaerobic digestion materials were on-farm anaerobic digestion materials
- the anaerobic digestion materials did not contain sewage biosolids or human body waste
Construction standards for a new or expanding permanent liquid nutrient storage facility for NASM are similar to ASM, with some exceptions. In addition to this factsheet, see the OMAFRA fact sheet, Storage of Non-Agricultural Source Materials (NASM) in a Permanent Nutrient Storage Facility, for more details.
Key considerations
Before building an earthen liquid nutrient storage facility on an operation that generates more than 5 nutrient units of manure annually, consider the following:
- All expanding and/or new earthen liquid nutrient storage facilities must be designed by a professional engineer in accordance with Part VIII of the regulation titled Siting, Construction and Storage.
- A professional engineer must perform a general review of the construction to ensure that the facility is built in accordance with the engineer’s design specifications.
- A building permit from the municipality may be required if concrete structure(s) are incorporated in the storage facility.
- You must have a nutrient management strategy (NMS), prepared by a certified nutrient management consultant and approved by OMAFRA, before starting construction or expansion of an earthen liquid nutrient storage facility.
- All new earthen liquid nutrient storage facilities must meet all the required setback distances from wells, surface water and tile drains that are specified in the regulations.
- All expanding and/or new earthen liquid nutrient storage facilities must have a minimum of 2.0 m of hydraulically secure soil between their bottom and bedrock or the uppermost identified aquifer. In most cases, a liner is also required.
Note: Hydraulically secure soils must have a maximum hydraulic conductivity of 1 × 10–8 m/sec. - Include other components not referred to in the regulation in the engineer’s design to protect the integrity of the structure and human health.
Sizing the storage structure
The size of the earthen storage facility depends on several factors:
- the amount of material generated at a time (daily, weekly)
- whether other materials, such as runoff and washwater, will be stored in the storage
- the number of days (or weeks) the facility has to store the material
- the net amount of precipitation entering the storage facility. For an uncovered earthen storage facility, the amount is based on the number of days of storage required by the operation and the specified allowance of 0.83 m/year (that is, 2.27 mm per day of storage) referenced in Table 5.2 of the Nutrient Management Protocol.
- the freeboard requirements (0.3 m for an earthen storage facility)
Note: Freeboard is an additional depth of storage required to deal with wave action due to wind and agitation and to provide a safety factor to address unexpected circumstances (such as excessive rainfall, leaks in water system). It is added to the calculated depth required for manure production and precipitation.
Amount of material generated
The amount of manure generated by farm animals varies between operations due to differences in herd management, including the amount of material used for bedding.
Determine the amount of manure from a livestock by taking measurements, or estimate it based on values provided in the regulation. For example, measure the amount of manure generated by an existing operation during clean-out of barns and existing storage facilities. If estimating the amount, refer to the Nutrient Management Tables associated with the regulation and the OMAFRA AgriSuite software for values of daily manure production for various livestock.
Size the storage facility based on the greater amount of manure measured at the farm or referenced in the regulation, unless several years of reliable records of manure production indicate lower manure production.
Storage capacity required
Under the NMA, farm operations subjected to the regulation because they are expanding or building a permanent nutrient storage facility or a structure to house livestock must provide a minimum storage capacity of 240 days for all nutrients generated and intended for storage at the farm (such as manure, washwater and runoff), with the following exceptions:
- Where a farmer sends some agricultural source material, generated on the farm, to a broker, the combined storage capacity provided by the broker and the farmer must total 240 days.
For example, a layer chicken operation that has an agreement with a broker who can provide 60 days of storage would only need a manure storage with a capacity of 180 days. - Where the period of use of the barn is less than 240 days.
For example, a beef feeder operation that houses the animals for 180 days from November 1 until they go to pasture on May 1 would only need a manure storage with a capacity of 180 days. - Where a farmer’s nutrient management plan (NMP) provides for the land application of nutrients to land on a schedule that reduces the storage requirements.
For example, an operation with an NMP providing for land application of manure more often than every 240 days would not require a storage with a capacity of 240 days.
Note: This is used for liquid manure storages, if the number of farm animals on the farm unit has not increased since September 30, 2003. - Where the farmer’s NMS includes transfers out of the farm unit.
For example, a dairy farm that transfers its manure off-site every 3 months to another farm unit, only requires a manure storage with a capacity of 3 months.
Also, take into consideration the storage capacity of all prescribed material received on the farm unit that is not directly applied to land (such as manure from other agricultural operations, NASM).
Siting
When siting a new storage facility, or an expansion of an existing one, consider the potential impacts to surface and groundwater as well as neighbours. Setbacks to surrounding features must be respected. Refer to the fact sheet, Siting requirements for permanent nutrient storage facilities to understand setbacks prescribed under the regulation, Minimum Separation Distance (MDS) to neighbouring properties and other considerations.
Using a qualified person
Before expanding or constructing an earthen liquid nutrient storage facility, a NMS, prepared by a certificate holder under Part X of the regulation and approved by OMAFRA, is required.
The regulation also has the following engineering requirements for new and expanding earthen liquid nutrient storage facilities:
Engineer’s Commitment Certificate — the professional engineer(s) must sign the Engineer’s Commitment Certificate prior to expanding or constructing an earthen liquid nutrient storage facility [O. Reg. 267/03, s. 71 (1)]. This is to ensure that the project conforms to the engineering requirements under the regulation, where applicable. Get the standard form for the Engineer’s Commitment Certificate from the Forms Repository.
Design — a professional engineer must design the construction or expansion, including any monitoring system. [O. Reg. 267/03, s. 71 (1)] Where required, incorporate provision for a liner and transfer system in the design and specifications. For example, if a pipe associated with a transfer system enters the nutrient storage facility, the design and specifications must include special considerations such as a reinforced opening and required flexible watertight gasket. The engineer who designs the storage facility should confirm whether a transfer system will enter the facility. If the design of a storage facility and the transfer system are not assigned to the same engineer, both engineers should communicate to ensure that the design of the storage facility takes into consideration the transfer system requirements under the regulation.
Site investigation — a professional engineer or geoscientist must carry out a site characterization study to verify that the soil conditions at the site are suitable for an earthen storage facility. [O. Reg. 267/03, s. 64]
Site review — a professional engineer must perform a general review of the construction or expansion project. This review process ensures that the liquid nutrient storage facility is built in accordance with the drawings and specifications of the engineer. [O. Reg. 267/03, s. 71 (1)]
Specific engineering criteria required by the regulation
Site investigation: All new or expanding permanent liquid manure or nutrient storage facilities require a site characterization. This involves a minimum number of test holes to identify soil types and the presence of any aquifer or bedrock to determine the suitability of a site for a storage facility and any specific design requirements under the regulation. For more details, read the OMAFRA fact sheet, Site characterization study for the construction of permanent nutrient storage facilities and the regulation. [O. Reg. 267/03, s. 65, 67, 68]
General design: The storage facility, including any associated plumbing systems used to transfer manure or liquid nutrients, must be designed to minimize leakage, minimize corrosion and be structurally safe and sound. (O. Reg. 267/03, s. 71).
All earthen liquid nutrient storage facilities must be sited over a minimum of 2 m of hydraulically secure soils. Note: Hydraulically secure soils must have a maximum hydraulic conductivity of 1 × 10–8 m/sec.
Types of storage facilities
Under the regulation, there are two types of earthen liquid nutrient storage facilities (O. Reg. 267/03, s. 65):
Type 1 — Storage for liquid agricultural source materials (excluding manure)
It must satisfy the criteria specified in Figure 2. The regulation includes details regarding interior surface treatment, soil anomalies and above-ground berm construction.
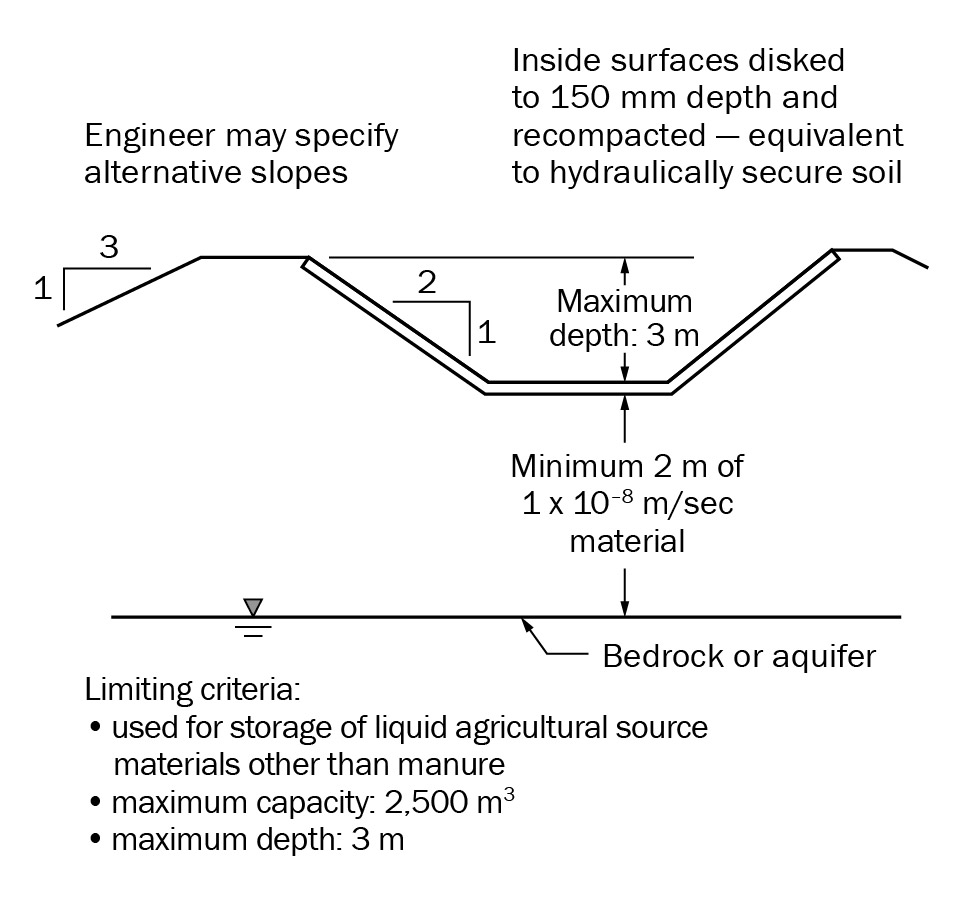
For example, the soils that form the inner surface must be disked to a depth of 150 mm and recompacted to meet a hydraulic conductivity of no more than 1 × 10–8 m/sec. Above-ground berms must be made of material that can be compacted with a saturated hydraulic conductivity of no more than 1 × 10–9 at 95% of modified Proctor density according to accepted engineering test criteria.
Type 2 — Storage for liquid agricultural source materials (including manure) and NASM
Must satisfy the criteria as specified in Figure 3. In addition to the 2 m of hydraulically secure soil, this option requires the installation of a compacted soil or synthetic liner. Some construction details for earthen facilities are presented in sections 65 and 79 of the regulation.
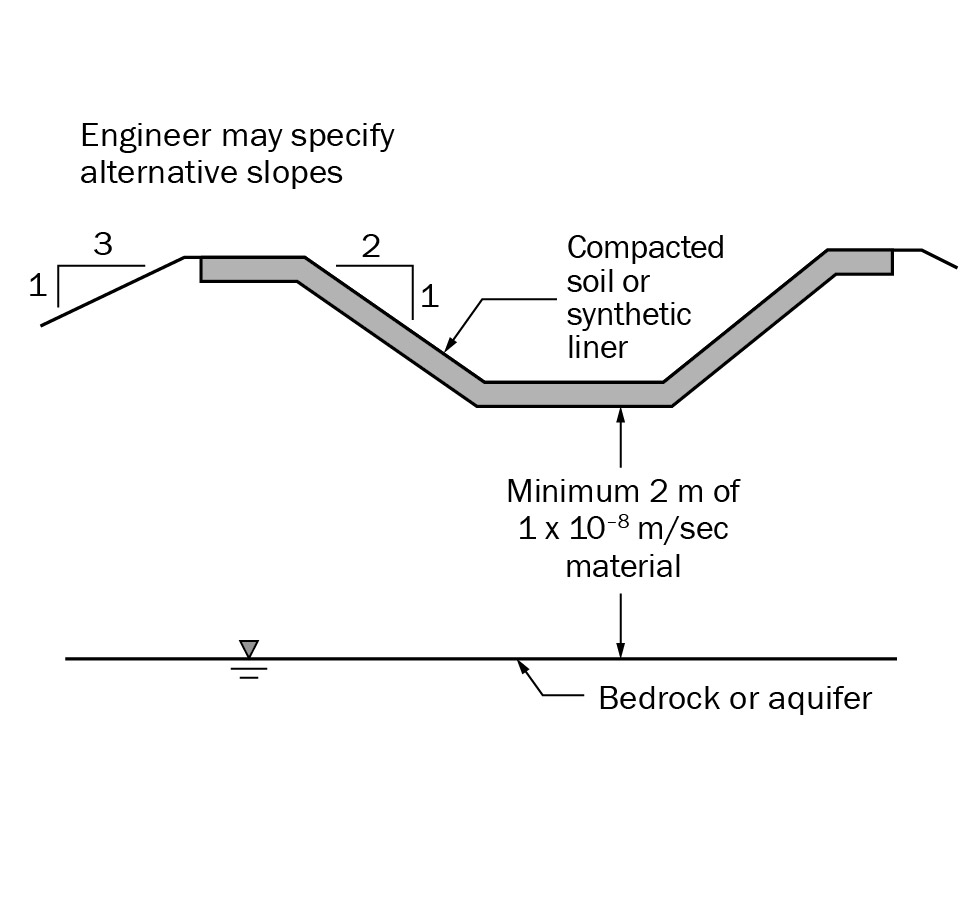
Liners
Earthen facilities must also include a liner, unless they are for the storage of liquid agricultural source material other than manure, and do not exceed the maximum capacity and dimensions shown in Figure 2.
Synthetic liners are defined in the regulation as geomembrane liners or geosynthetic clay liners. Geomembrane liner is a synthetic membrane with very low permeability, whereas a geosynthetic clay liner is a liner that consists of high swelling sodium bentonite between two layers of geotextile fabric having a saturated hydraulic conductivity of 1 × 10–9 m/sec or less. Both types of synthetic liner are used to control fluid migration in a nutrient storage facility. Section 74 of the regulation provides more details about the installation of synthetic liners.
Compacted soil liners are defined in the regulation as liners that are composed of hydraulically secure soil that is compacted to 95% of modified Proctor density at the optimum moisture content to meet a maximum saturated hydraulic conductivity of not more than 1 × 10–9 m/sec.
Liner details are presented in sections 73 to 75 of the regulation. Section 75 of the regulation specifies how to construct a compacted soil liner. For example, it must be constructed:
- using a minimum of 6 layers of 150 mm thick material on the inside sloping surfaces, and
- using a minimum of 4 layers of 150 mm thick material on the floor surface
Secondary containment
If the liquid level in the storage facility is partially or wholly above the surface of the surrounding soil, the following options apply:
- a professional engineer can determine that the storage and landscape features around the facility are adequate to ensure that a secondary containment system is not required; or
- the designer includes a secondary containment system, with a capacity of 110% of the above-ground portion of the volume of material stored
Ventilation
All covered storage systems must have a ventilation system that is either a powered or natural ventilation system to prevent the accumulation of corrosive or noxious gases.
Transfer systems
A nutrient storage facility often includes a liquid nutrient transfer system. A transfer system includes the sump pit, pump and associated piping to move manure from a barn to a storage facility. This system can also be used to transfer other agricultural source material (such as washwater, runoff) or NASM. All liquid transfer systems, other than floor transfer systems as defined in the regulation, must be designed by a professional engineer.
Transfer systems rely on gravity or mechanical devices (such as pumps and piping) to move the material. Regardless of the conduit used, it is important to make secure connections.
Rubber gaskets and bell and spigot connections are commonly used to make sure that the transfer piping is watertight. Proper connectors ensure that the integrity of the system is maintained. Figure 4 shows a PVC transfer piping system being assembled during barn construction.
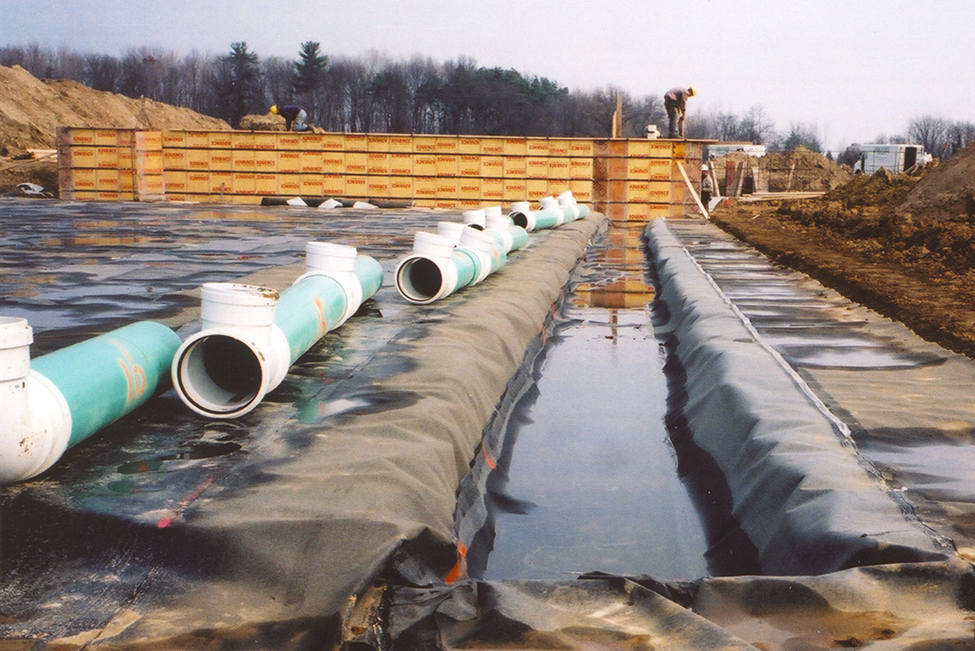
The regulation states that no person shall construct or expand a liquid nutrient transfer system when constructing a permanent liquid nutrient storage facility unless:
- the system is designed and constructed or expanded in accordance with Part VIII of the regulation
- a professional engineer designs the construction or expansion
- a professional engineer performs a general review of the construction or expansion to ensure that it is done in accordance with the engineer’s design specification and Part VIII of the regulation
All connections in a liquid transfer system must be installed using specifically designed fittings and gaskets that are compatible with the pipe material (O. Reg. 267/03, s. 87):
- All pipes entering a liquid nutrient storage facility must have a flexible, watertight gasket or membrane installed between the pipe and the floor or wall of the storage structure to serve as an anti-seepage collar.
- Any transfer system having an opportunity to backflow to the pump or pump-out chamber must have both a primary and secondary shutoff valve.
For more information on transfer systems, read the OMAFRA fact sheet, On-farm liquid nutrient transfer systems and the regulation.
Additional requirements
The regulation specifies minimum site conditions and construction standards, but consider the following items in the design and construction of a liquid nutrient storage facility made of earth:
- Safety fence — An earthen liquid nutrient storage facility should be equipped with a permanent safety fence extending a minimum of 1.5 m above adjacent grade. Gates should be latched to deter access by children and livestock.
- Final cover — Berms/side walls should be covered to prevent erosion and preserve their integrity.
- Warning signs — Post signs around the storage facility to warn people about its presence and their safety. Maximum and minimum levels of liquid in the storage facility should also be marked and posted for those managing the facility to prevent causing a spill and damage to the facility.
Contact the local municipality to verify if additional requirements apply to your project.
Optional features
Think about features such as an agitation pad or tractor access ramps. These systems should be properly incorporated into the earthen storage to ensure safety, structural integrity and leakproof construction. Features judged to be a structure require building permits. Features such as a tractor access ramp can add a large surface area, increasing rainfall amounts that must be stored and land applied.
Disclaimer
The information in this fact sheet is provided for informational purposes only and should not be relied upon to determine legal obligations. To determine your legal obligations, consult the relevant law. If legal advice is required, consult a lawyer. In the event of a conflict between the information in this fact sheet and any applicable law, the law prevails.
This fact sheet was originally written by Don Hilborn, P. Eng., (retired), OMAFRA, and John Johnson, P. Eng., (retired), OMAFRA. It was revised by Benoit Lebeau, P. Eng., OMAFRA, and Richard Brunke, P. Eng., OMAFRA.