Disposal vessels for on-farm deadstock
Learn how to use disposal vessels for managing on-farm deadstock according to the Nutrient Management Act, 2002. This is technical information for Ontario livestock and poultry producers.
ISSN 1198-712X, Published October 2023
Introduction
Under O. Reg. 106/09 of the Nutrient Management Act, 2002, disposal vessels are one of the permitted options for the disposal of dead farm animals (deadstock). This fact sheet describes what disposal vessels are and how to install, operate and decommission them.
This fact sheet does not cover all requirements contained in the regulation. Consult the regulation to determine all requirements.
What is a disposal vessel
A disposal vessel is a scavenger-proof, leak-proof container installed under, partially, or above ground, into which deadstock are placed to decompose. Figure 1 shows a steel disposal vessel used in a 5-year research trial at an Ontario sheep farm.
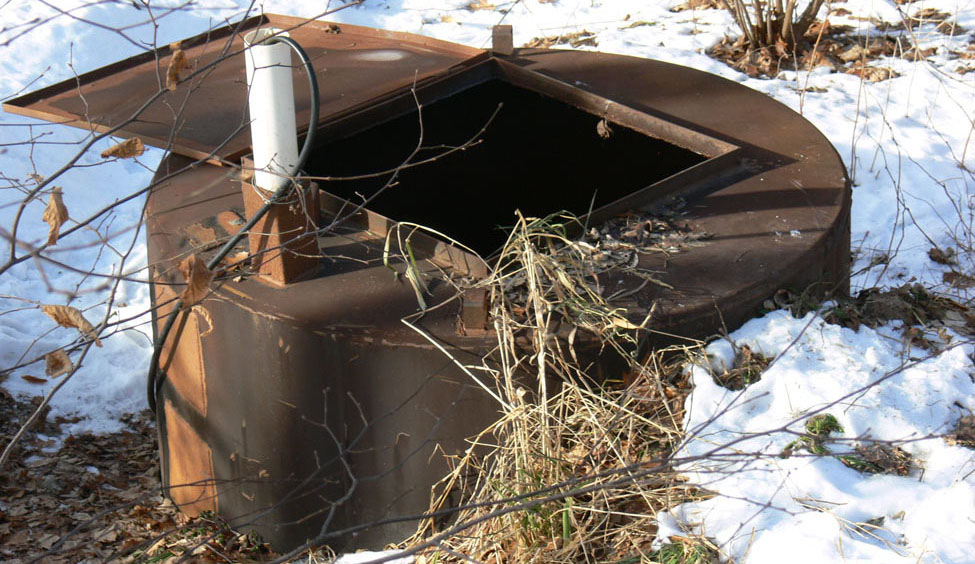
Disposal vessels allow year-round burial. Decomposition occurs in a variety of ways:
- aerobic and anaerobic breakdown by microorganisms
- consumption by insects such as blow flies
- evaporation of water
- release of gases such as carbon dioxide
Disposal vessels — also known as disposal units, burial pits, dead pits and mortality pits — were used in the past in North America for dead poultry. The former Canada Plan Service described them as “aerobic disposal with limited air pollution.” However, these disposal vessels had no bottoms, allowing leachate released during decomposition to drain downward with little regard for groundwater quality.
In soils with aquifers close to ground level, groundwater was also able to rise into the vessel, then back out again — clearly an undesirable situation. Localized groundwater problems were reported in literature
How and why disposal vessels work
There are many things that happen when deadstock is placed in a disposal vessel. Deadstock flesh is opened by insects, exposing it to microorganisms. Decomposition occurs aerobically on top of the pile but also anaerobically to the material buried under other deadstock. Air temperatures in the vessel will fluctuate over the day, the season and when deadstock is added. The rate of water evaporation and release of gases fluctuates. Although the mass of deadstock placed in a vessel can be measured, it is difficult to measure how much mass exits the system through evaporation of water, movement of insects and microorganisms, and exchange of gases.
Carcass decomposition is faster during warm weather than cold. However, if vessels are installed mostly underground, decomposition continues during the cool fall or early spring because air temperatures inside the vessel remain high enough (usually above freezing) throughout the year.
Figures 2a, 2b and 2c show what happens inside a disposal vessel over time. Figure 2a shows virtually no decomposition of recently placed deadstock. Figure 2b shows prolific maggot activity occurring some time later, particularly during hot summer weather. Figure 2c shows a tough, flat, mat-like crust, which results after considerable decomposition has occurred and no more deadstock have been added for some time. Snow was sprinkled on the pile for this picture for visual effect.
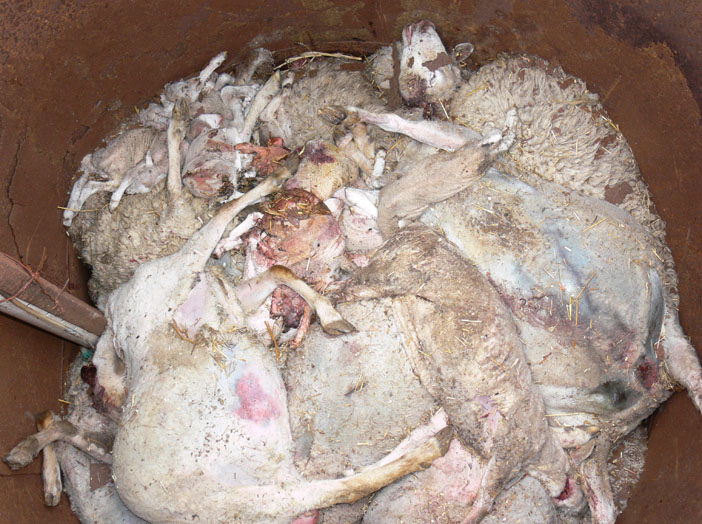
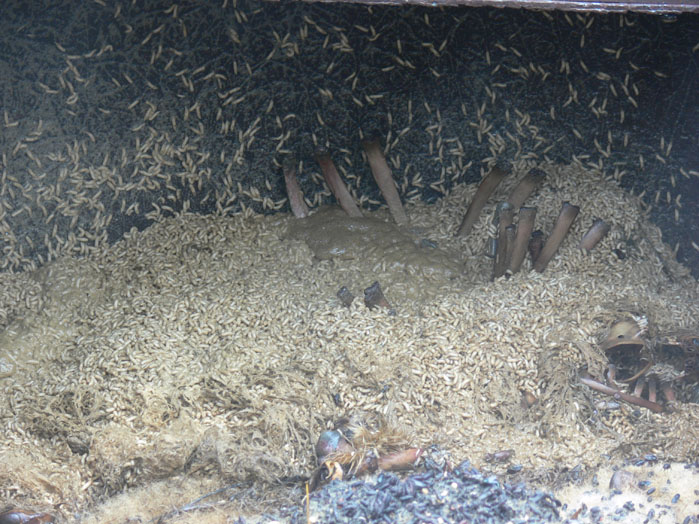
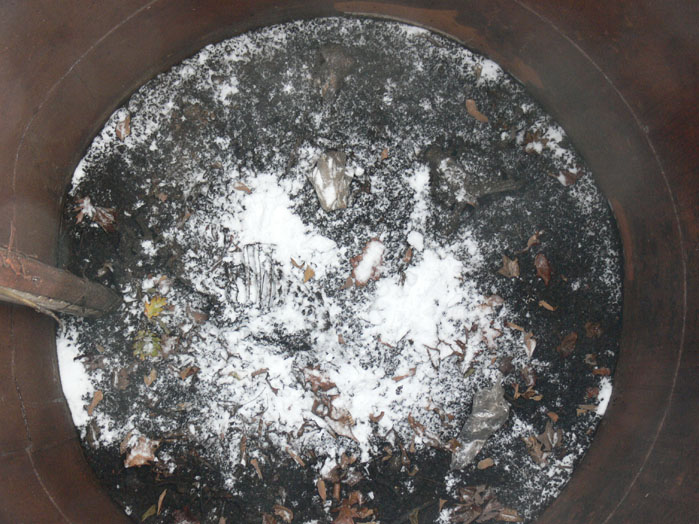
Advantages of disposal vessels
The advantages of disposal vessels include:
- acceptable when few other viable options exist
- simple and practical to use
- environmentally friendly if done in accordance with the regulation
- relatively inexpensive to install and operate
- good for biosecurity, by keeping deadstock on farm
Disadvantages of disposal vessels
The disadvantages of disposal vessels include:
- impractical to empty when full, so vessels must be decommissioned as required in regulation
- sometimes challenging to site properly with respect to water table/bedrock as required in the regulation
- difficult to fill and to decommission when installed mostly above ground
- inclined to “float like a boat” if not installed properly
- sometimes complex to install — installing disposal vessels deeper than 1.2 m (4 ft) requires taking certain precautions
Deadstock suitable for disposal vessels
Disposal vessels will work with any type or size of deadstock, but they make more sense for operations with dead farm animals that individually weigh up to about 75 kg in size, such as: sheep, goats, poultry, smaller swine, calves and furbearing animals. The smaller carcass size allows these animals to decompose quickly.
Feathers do not decompose quickly, so avoid disposing of poultry in a disposal vessel. One of the other allowable disposal options for poultry, such as composting or storing them in a large chest freezer for periodic pick-up by a licensed deadstock collector, might be more practical and cost effective.
Disposal vessels also make more sense for operations with a maximum of approximately 65 kg of deadstock per week to manage. Biological activity fluctuates in a vessel, but adding too many deadstock at once can overwhelm the system, slow decomposition and cause odours. For example, this could occur if large volumes of fur-bearing deadstock were disposed of all at once in a vessel, after fall pelt harvest.
Research
Some types of livestock operations have few viable deadstock options, such as on sheep or goat farms (Figure 3):
- Licensed deadstock collectors rarely want to collect sheep or goats for economic reasons.
- Burying in winter is impossible because of frost in most areas or because the operation is located on soil that is shallow to bedrock.
- Composting does not generate high enough temperatures to destroy proteins responsible for scrapie, a fatal brain disease. Producers do not want to spread the resulting compost on fields because of the possible spread of this disease.
- Incineration is more difficult because of the wool in sheep, and it is a very costly option.
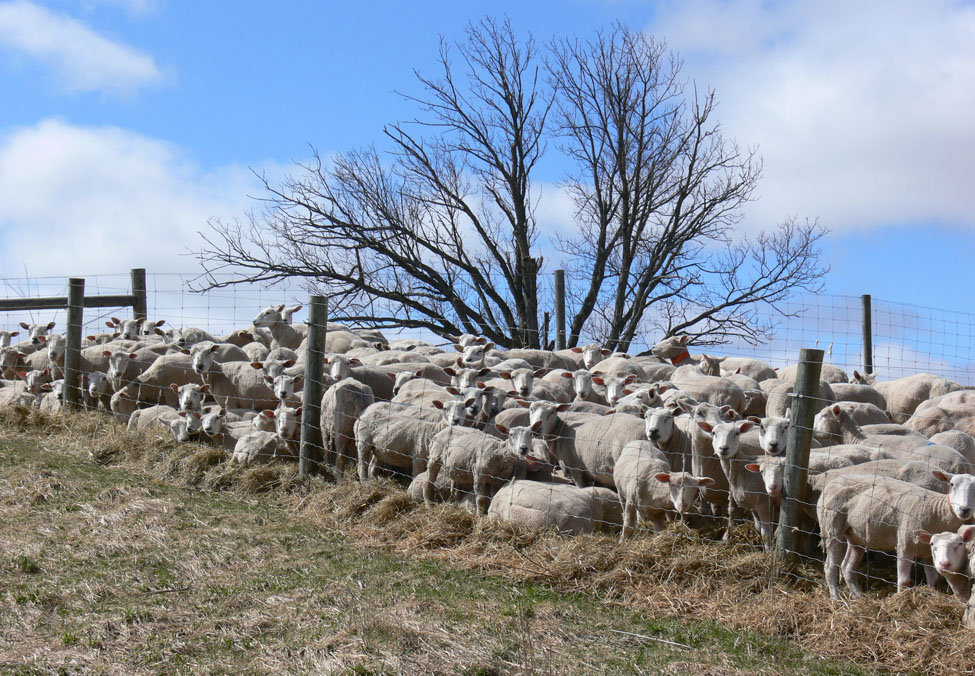
Installing disposal vessels
The options for installing disposal vessels (Figure 4) are:
- above the ground on a supporting structure
- on the ground, or slightly below ground
- partially, or fully below ground
Installing a disposal vessel above the ground on a supporting structure is not recommended for the following reasons:
- the vessel requires a supporting structure specifically designed to withstand the full and possibly unbalanced weight of materials inside
- above-ground installation would be costly
- placing deadstock inside an above-ground vessel is difficult and hazardous
- decommissioning above-ground vessels is time consuming and possibly hazardous
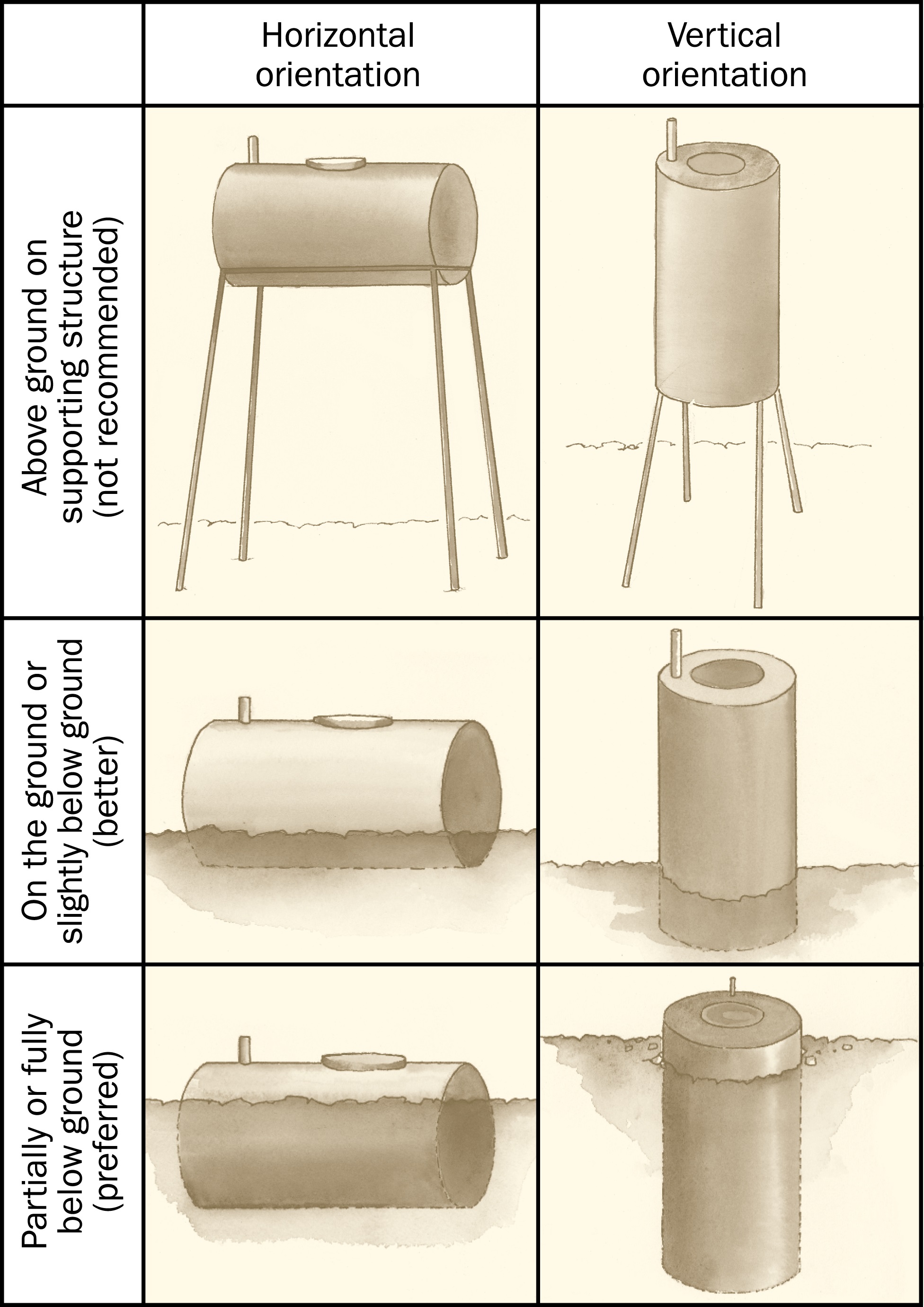
Installing a disposal vessel on the ground or slightly below ground is better and may be the only viable option if there is shallow bedrock or aquifer in the area. The regulation requires the lowest point of a disposal vessel that is partially or fully below ground to be at least 0.9 m (3 ft) above the top of the uppermost identified bedrock layer or aquifer, unless the disposal vessel is placed on an impervious pad.
However, the further out of the ground a disposal vessel is, the more difficult it is to place deadstock inside and the more difficult it is to decommission. If possible, place at least part of the vessel below ground to help anchor it.
Installing a disposal vessel partially or fully in the ground is preferred for the following reasons:
- Lifting deadstock into the vessel is easier, especially if the access hatch is about 0.6 m (2 ft) above ground. Hatches more than 1.2 m (4 ft) above ground are not recommended.
- Heat from the surrounding soil keeps the vessel warmer in winter, which aids in the decomposition.
- Decommissioning the vessel is easier and less costly because it is already mostly underground. Place a flag near below-grade disposal vessels to warn people they are there. Be sure to take into account the possible depth of snow around the vessel in winter.
Disposal vessel materials
Disposal vessels can be made from steel, concrete, plastic, fibreglass or other materials (Figure 5). They must be designed for external soil pressures when installed below grade, internal carcass pressures when installed above grade or both. Vessels must be impervious and leakproof (other than the duct) when the hatch is closed to comply with the regulation.
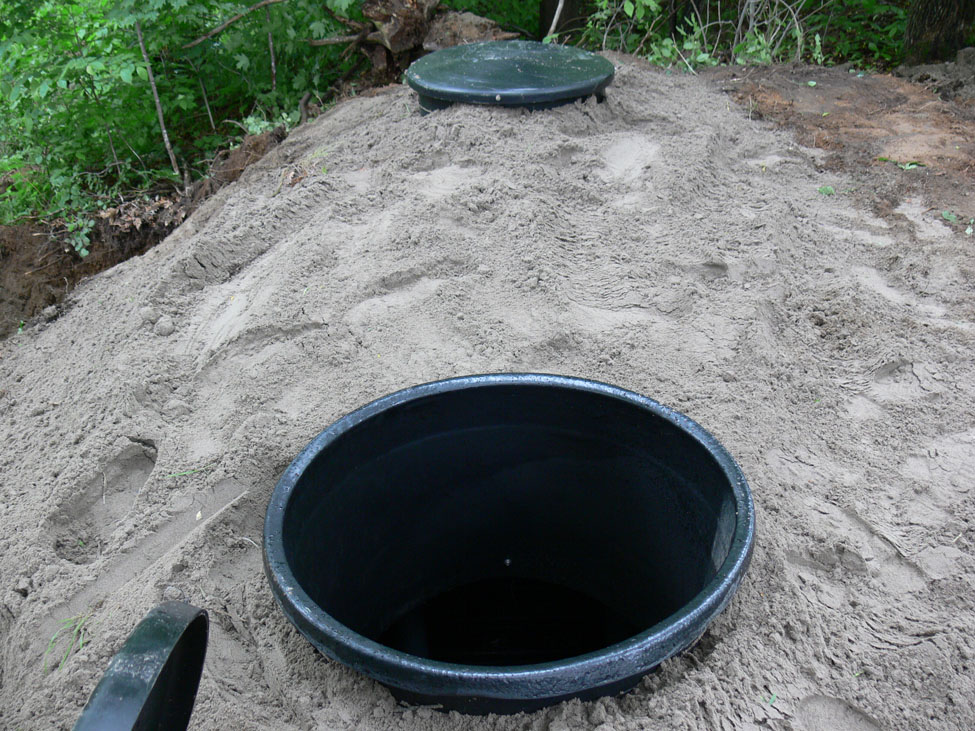
Purchasing new disposal vessels, regardless of material type, could be cost-prohibitive. Normally, producers will obtain previously used vessels, such as cylindrical steel fuel tanks, for this purpose, provided they are thoroughly emptied and cleaned of residual fuels because of the environmental risk and safety concerns of fire and/or explosion.
It is important that once a disposal vessel is installed, it be filled to capacity and decommissioned properly because a partially filled underground vessel could deteriorate and cave in over time, posing a safety risk. Over time, the vessel contents become a mass of bones and organic materials no different than if many deadstock were simply buried in the soil at one time.
Where possible, plan the vessel size to correspond with your projected disposal needs over a few years, remembering that the regulation requires the interior volume of a vessel to not exceed 10 m3 (353 ft3).
Siting
Disposal vessels do generate some odours and flies when in use. They represent a potential threat to surface and groundwater if they leak or overflow. To minimize potential nuisance complaints from neighbours and any potential threat to water quality, select the proper setbacks when locating a vessel. Table 1 shows the setbacks for disposal vessels required by the regulation.
Feature | Setback |
---|---|
Highway | 30 m |
Lot line of land on which vessel is located | 15 m |
Flow path to the top of the bank of the nearest surface water or tile inlet | 100 m |
Field drainage tile | 15 m |
Lot line of land with an industrial or parkland use | 100 m |
Lot line of land in a residential area, or from land with a commercial, community or institutional use | 200 m |
Municipal well | 250 m |
Drilled well with depth of at least 15 m and watertight casing to depth of at least 6 m | 50 m |
Any other well (such as a gas well) | 100 m |
Livestock housing facility, outdoor confinement area and residential structure (neighbour’s house) located on land not part of the land on which the disposal vessel is located | 100 m |
Another disposal vessel on the same parcel of land | 15 m |
Areas subject to flooding every 100 years | Not allowed |
Organic soil or hydrologic soil group AA and/or A | Allowed |
Orientation
Recent Ontario on-farm research has compared the advantages of vertical versus horizontal orientation of equally sized, cylinder-shaped disposal vessels.
Advantages for below-ground vertical or horizontal cylinder-shaped disposal vessels
Below-grade vertical
- deeper, therefore warmer soil, helping decomposition in colder weather
- easy to install one large hatch on flat end
- easier to fill vessel as deadstock distribute more uniformly
Below-grade horizontal
- shallower, therefore better suited to sites with shallow bedrock or aquifer
- room for more, but likely smaller, access hatches along long top of vessel
- less excavation = lower installation costs
Access hatch and air vent
At least one access hatch is needed, but more may be necessary on long, horizontally oriented disposal vessels to ensure the entire vessel gets filled. The hatch needn’t be airtight, since loosely fitting ones encourage entry of flies and insects. Hatches 0.9 m (3 ft) square will fit 75‑kg (165-lb) animals. However, large steel hatches are very heavy. Install all-weather hinges and large handles for easier opening. Lock hatches between uses (Figure 6).
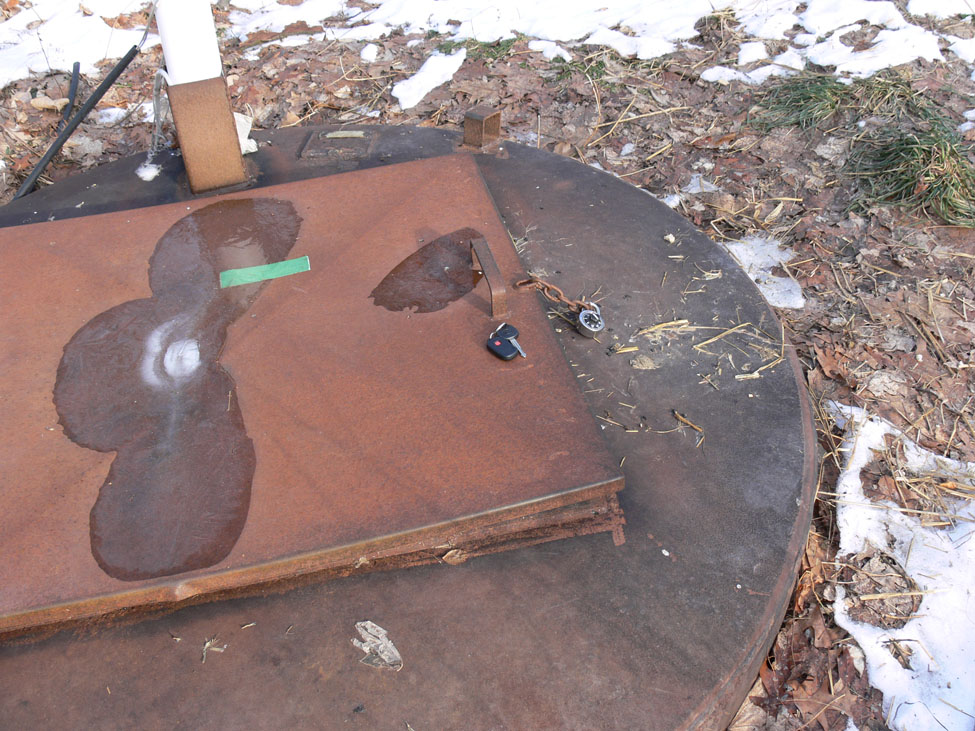
The regulation requires vessels to have at least one duct that is large enough to allow flies and other insects to enter the vessel and to allow air movement in and out of the vessel. Locate this duct above the surface of the ground (and expected snow levels) so it is exposed to air at all times. Except for this duct, the vessel must be impervious and leakproof when the hatch is closed. Further, the vessel must protect the deadstock from scavengers, rodents and pests other than insects.
Sizing
Every deadstock has a different shape and weight. The mass of deadstock in a disposal vessel has an effective density defined as “the weight of deadstock placed over time, divided by the volume they take up in the disposal vessel over time.” Because of the exodus of flies, other insects, moisture and gases, the actual weight of materials remaining in the vessel will be less than what was added, so the effective density rises over time.
Ontario research
Under the regulation, individual disposal vessels can be no larger than 10 m3 (353 ft3 or 2,200 Imperial gallons, or 2,642 U.S. gallons). However, the top 10% of the vessel will remain unfilled due to the filling/settling process. When designing the vessel, assume only 90%, or 9 m3, is available for receiving deadstock, and try to plan to fill it no sooner than 5 years before decommissioning. So, 9 m3 × 1,600 kg/m3 = 14,400 kg to fill the vessel (31,680 lb). Assuming 5 years to fill, this is about 55 kg/week (121 lb), which should work for a sheep herd of about 400 ewes with typical death losses.
Excavating
It is beyond the scope of this factsheet to describe all the safe excavation steps for installing a disposal vessel. However, be aware that regardless of the type of material a disposal vessel is made of (even concrete) it can float like a boat under the right (or wrong) water table conditions.
O. Reg. 106/09 specifies that the bottom of the disposal vessel be at least 0.9 m (3 ft) above the top of the uppermost identified bedrock layer or aquifer. Excavate one or two test pits in the vicinity of the proposed disposal vessel site to confirm groundwater/bedrock conditions. If test pits show discoloured “mottled” subsoil, there might be a seasonal high water table, even if there is no water present in the hole during excavation.
Backfill the soil uniformly, compact it around the vessel in layers, then slope it against the vessel so surface water does not run down the outside shell of the vessel and cause the vessel to float. Keep excavated soil stockpiled nearby for eventual decommissioning.
Add sandy potting soil, or similar loose soil (not clay), in a ring at least 1 m (3.3 ft) wide and 10 cm (4 in.) deep outside and around the disposal vessel to give a place for escaping larvae to pupate. For a 2-m (6.5-ft) diameter, vertically oriented vessel, this would be at least 1 m3 (1.3 yd3) of soil (Figure 7).
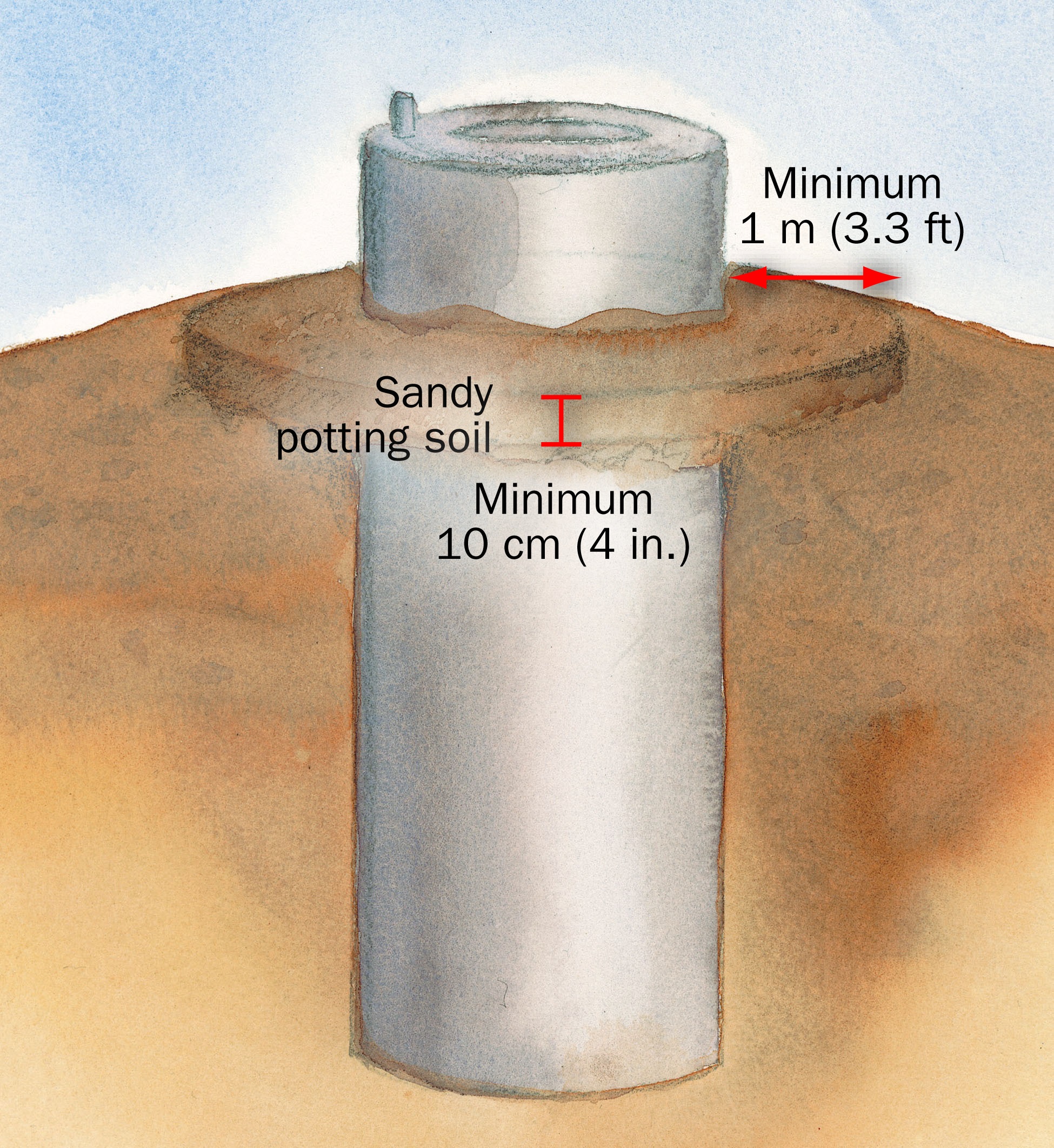
Filling
The recipe for filling the disposal vessel is simple:
- open the secured hatch
- place deadstock inside
- close and secure hatch
- let natural processes proceed
Place deadstock in a vessel carefully. Once placed, it should not be moved. Never enter a disposal vessel to move deadstock. Vessels are filled with noxious gases, odours, flies, maggots and beetles.
To reduce odours and keep the disposal vessel area clean:
- Keep the hatch closed and locked between uses and clean up the area after placing deadstock.
- Locate vessels at least 100 m from neighbours. Stay further away if possible. There will be strong odours within 25 m (82 ft) of vessels. Anecdotal evidence suggests that wildlife avoid going near disposal vessels, probably because the odour warns them there is something inside they should not eat.
Decommissioning
O. Reg. 106/09 states that a disposal vessel must be promptly closed once it is no longer used for the disposal of dead farm animals.
Use as much of the originally excavated soil as possible, then open the hatch to allow filling the remainder of the vessel with soil (Figure 8).
Burying the entire vessel allows its contents to continue to decompose and settle over time, while the soil settles with it. Burying also puts the vessel out of sight and makes the area safer to work nearby. Compact that soil if possible. Add another layer of at least 0.6 m (2 ft) of soil on top.
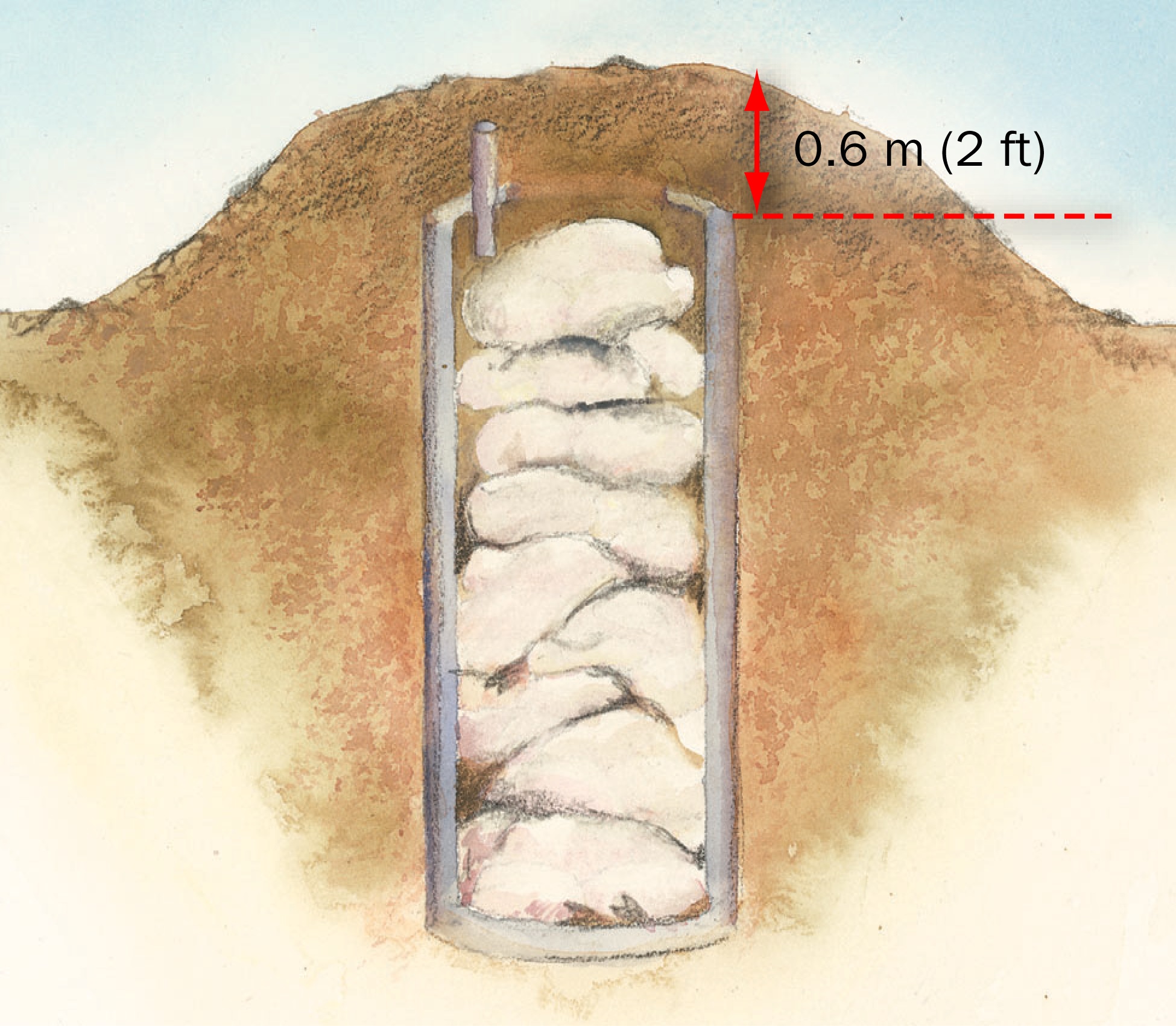
Taper the soil away from the vessel steeply to:
- create a steep “hill” to help prevent tractors and other equipment from getting too close in future (barriers such as large stones would also help)
- allow for settling both into and around vessel
- help prevent any scavenging
- encourage rapid surface drainage of clean rainfall away from the disposal vessel
The higher the vessel was originally installed above grade, the higher the resulting final pile, so this is one reason to install as much of the vessel below grade as possible in the first place (Figure 9).
Where much of the vessel has been installed high above ground, there is unlikely to be enough soil from the original excavation, so additional soil will be needed.
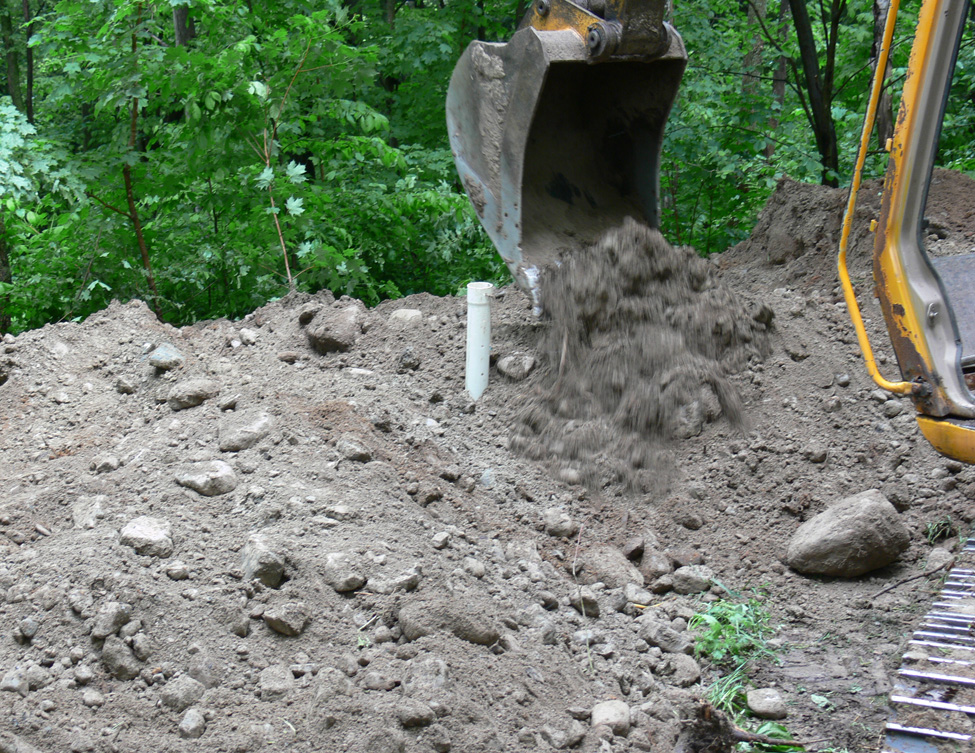
Soil from excavating a hole for your next vessel could be used to decommission the current vessel, and so on. Place topsoil as a top-dressing on the decommissioned pile then plant quick-growing grasses to help stabilize the soil.
What remains after decommissioning is a mass of essentially biologically inactive organic materials not unlike cured compost, but with many bones, all inside a vessel that may deteriorate over a long period of time, depending on material.
Some people may question why the vessel contents wouldn’t simply be removed, spread on the land like compost, then the disposal vessel reused. This would be difficult, especially for vessels below ground:
- The vessel contents will be tightly packed inside and cannot be pumped or dug out.
- The vessel contents will contain a lot of bones, which will not spread particularly well.
- The vessel will be extremely heavy and virtually impossible to lift and tip over to dump the contents.
- Unless the access hatch is large, dumping contents will be like shaking pennies out of a piggy bank.
On sheep farms, doing this runs the risk of transmitting scrapie disease.
Example: disposal vessel costs
Additional information on the requirements of specific disposal methods is available from deadstock management of farm animals in Ontario.
Disclaimer
The information in this fact sheet is provided for informational purposes only and should not be relied upon to determine legal obligations. To determine your legal obligations, consult the relevant law. If legal advice is required, consult a lawyer. In the event of a conflict between the information in this factsheet and any applicable law, the law prevails.
This fact sheet was updated by Dan Ward, P. Eng., engineering specialist, poultry structures and environment and other livestock housing and equipment, Ministry of Agriculture, Food and Rural Affairs (OMAFRA). It was originally written by Hugh Fraser, P. Eng., agricultural engineer, OMAFRA (retired) and reviewed by Dan Ward, P. Eng., engineering specialist, poultry structures and environment and other livestock housing and equipment, OMAFRA, John and Eadie Steele, sheep producers and Chris Kennedy, sheep producer, Ontario.
Footnotes
- footnote[1] Back to paragraph Ritter, W.F., Chirnside, A.E.M., Harris, J.R. 1988. Impact of dead bird disposal on groundwater quality. Paper #88-2546, American Society of Agricultural Engineers, 1988.
- footnote[2] Back to paragraph Ritter, W.F., Chirnside. 1995. Impact of dead bird disposal pits on groundwater quality on the Delmarva Peninsula. Bioresource Technology, 53: 105-111.
- footnote[3] Back to paragraph Fraser, H.W. 2009. Disposal vessels revisited: Low-cost option for daily livestock mortalities under 75 kg in size. Paper # 09-5616, American Society of Agricultural and Biological Engineers, 2009.