Hydrogen sulphide in agricultural biogas systems
Learn to manage hydrogen sulphide gas found around agricultural biogas systems. This technical information is for Ontario producers.
ISSN 1198-712X, Published October 2022
Introduction
Hazardous gases are found in many locations on farms where organic material is present. These areas may contain dangerous levels of gases, such as hydrogen sulphide (H2S), if the gases are not managed properly. This fact sheet focuses on H2S found around agricultural biogas systems and recommends safety precautions for protecting farm workers.
Dangers of H2S
When biogas is produced for renewable energy production, 50%–70% of the gas volume is made up of methane (CH4). Biogas also contains a large proportion of carbon dioxide (CO2), 30%–50% by volume, and traces of gases such as ammonia (NH3), hydrogen (H2) and nitrogen (N2) along with H2S. Input feedstocks and output digestate materials (including manure) can produce these gases when stored, mixed or handled in biogas systems. These gases are considered dangerous and can create a hazardous atmosphere if ventilated improperly. H2S is considered the most dangerous of the gases.
Exposure to elevated concentrations of H2S is extremely harmful. H2S interacts immediately with the blood’s hemoglobin to block oxygen from being carried to the body’s vital organs and tissues. Table 1 describes the effects of H2S on human health.
Concentration of H2S | Effects on humans |
---|---|
4–10 ppm | Detectable moderate odour (rotten-egg smell), eye irritant |
11–100 ppm | Unpleasant odour, eye irritation, coughing, loss of smell after an exposure of 2–15 minutes |
101–500 ppm | Eye inflammation, irritation of respiratory tract |
501–1,000 ppm | Rapid loss of consciousness and death |
>1,000 ppm | Instantaneous death on first breath |
Source: American Society of Agricultural and Biological Engineering Standards, Manure Storage Safety ASABE EP470.1 OCT2011 (R2016).
A major concern with the detection of H2S is that the human nose loses its ability to detect the gas when exposed to dangerous levels or for prolonged periods of time. This results in a false sense of security. Never rely on the sense of smell to detect H2S; instead, use a personal gas monitor to monitor levels.
H2S is heavier than air, so it is found just above the surface of the organic material undergoing decomposition. Presently, there are no standards for H2S exposure limits in the farm workplace, but employers must take all reasonable precautions to protect the health and safety of workers. A current best management practice in Ontario is to set the minimum alarm level at 10 ppm for H2S on gas monitoring devices in areas where H2S is present.
Sources of H2S around agricultural biogas systems
Locations where H2S is found around agricultural biogas systems are divided into three categories:
- storage of input materials (feedstock) prior to digestion
- equipment that handles biogas
- storage of output (digestate) materials after digestion
The following sections describe the potential sources of H2S gas in these areas and the best management practices for reducing associated risks.
Storage of input (feedstock) materials prior to digestion
Agricultural source input materials
The most common agricultural source input material is manure, either in a liquid, semi-solid or solid form. Liquid manure is often stored in below-ground concrete/earthen storages where H2S and other hazardous gases can develop. In contrast, solid manure is stored outside in the open where the potential to accumulate H2S is minimal. Other solid materials, such as feeds for livestock, are stored in a sealed environment or in structures where air circulates.
Dangerous levels of H2S, methane or nitrogen dioxide (NO2, commonly known as silo gas) are present in these structures and can cause serious health problems. See the OMAFRA fact sheet, Hazardous gases on agricultural operations, for information on how to recognize and manage these common hazards associated with agricultural operations.
Liquid nutrient transfer systems
Liquid nutrient transfer systems are used to transfer liquid manure from the livestock operation to the anaerobic digester. Sump-like pits are located inside (floor transfer system, Figure 1) or outside the livestock barn to collect liquid manure from the livestock operation. Both of these systems have the potential to generate and accumulate dangerous levels of H2S.
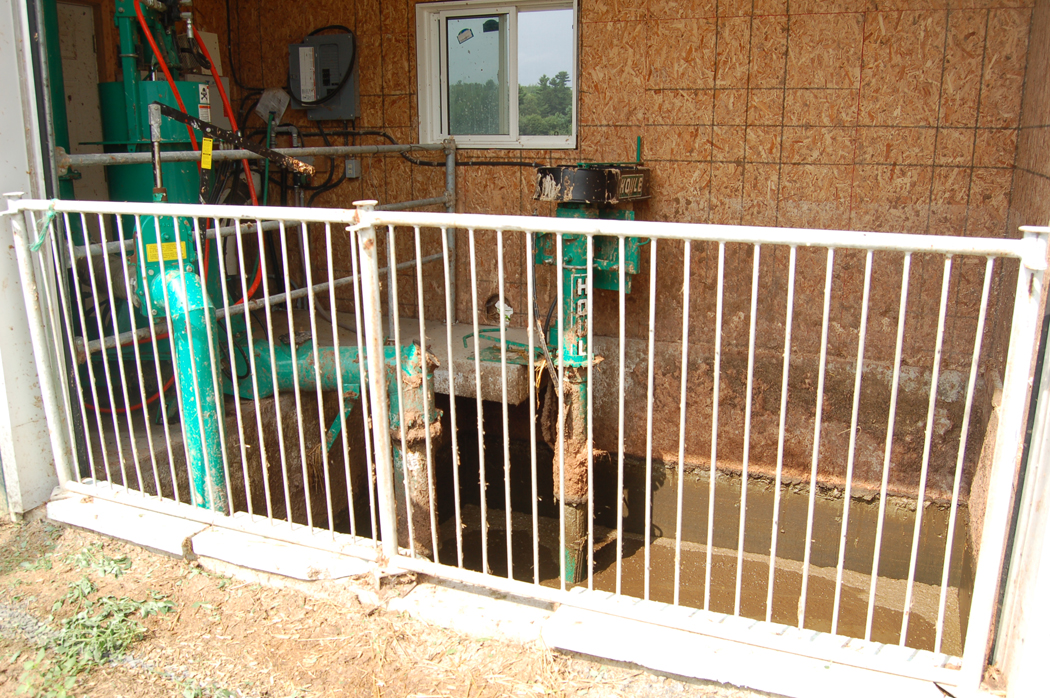
An agricultural biogas system may use nutrient transfer systems located in a partially enclosed facility to pump liquid manure from the barn and to mix in drier agricultural source materials. This practice represents a higher risk of producing and releasing H2S in enclosed areas, where it can get trapped, and increases the risk of exposure to unsafe levels of H2S.
Past research demonstrates that mixing liquid hog manure stored in sub-floor slurry storage pits immediately releases a rapid surge of H2S (Patni and Clarke, 2003). The following management suggestions are provided to reduce the risk of exposure to H2S around nutrient transfer systems:
- Use pit exhaust fans to reduce the risk of animal and farm worker exposure to high H2S concentrations above the floor slats.
- Prevent the slurry from free falling and splashing into the pumping pit or the nutrient transfer system (Patni and Clarke, 2003).
- Build the structures out in the open and rely on a design that uses fully open natural ventilation concepts or large mechanical ventilation (for example a pit exhaust fan) to remove H2S directly from the pit (Manure Storage Safety. ASABE EP470.1 OCT2011 (R2016)).
- Pump liquid input materials stored in the structure to the digester regularly to reduce the risk of accumulation of H2S trapped in the liquid.
- Keep access doors and other entries fully opened or have mechanical ventilation systems operating while pumping during winter months to reduce the risk of H2S exposure and accumulation. During winter, do not be tempted to keep doors closed while pumping to reduce the risk of freezing.
Off-farm input materials: co-substrate input tank
Using off-farm materials to boost biogas production is a popular practice for agricultural biogas systems. Materials such as grease from restaurants and residues from agri-food processing are co-digested with livestock manure generated on the farm. If the dry matter content (DM) of these off-farm materials is less than 18% or is easily pumped, they must be stored in a sealed tank called a co-substrate input tank (Figure 2). Gas production by active bacteria can accumulate inside the sealed co-substrate tank.
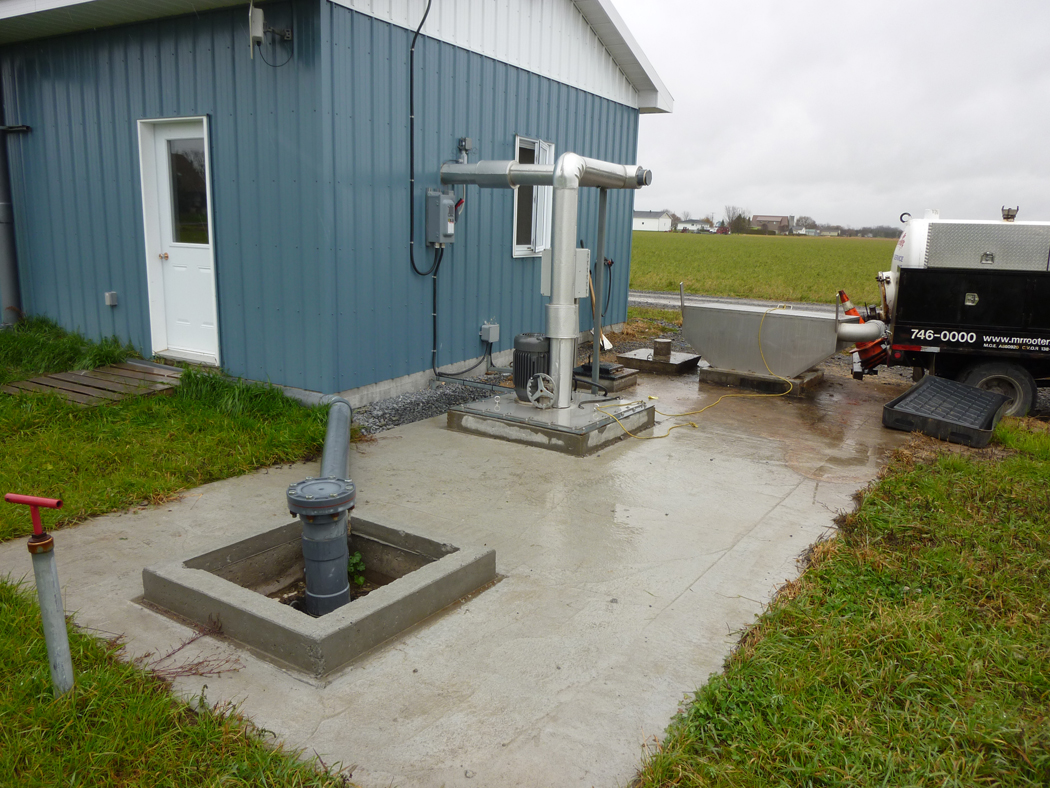
The following management practices and design features are recommended to minimize the risk of exposure to generated gases:
- Verify that the tank design incorporates an exhaust air pipe. As liquids are added to the tank, the exhaust air pipe allows the gases to escape and prevents exhaust from being expelled near the operator of the co-substrate tank. There is no room for the gases to remain in the tank.
- Verify that the design and operation of the co‑substrate input tank avoids unnecessary entry.
- Select equipment that is removable from outside the tank (for unplugging or repair).
- Choose off-farm materials with low levels of grit, debris and plastic contaminants.
- Use pumping equipment that minimizes settling of solids and is resistant to plugging.
- Install tanks capable of heating up their contents to reduce solidification of fats, oils and greases (FOG) right before pumping or mixing to minimize maintenance or entry.
Off-farm input materials: dry co-substrate storage
Dry off-farm materials, typically greater than 30% dry matter, are commonly ensiled on the farm in partially enclosed horizontal silos (Figure 3). H2S and NO2 can be trapped inside the materials and released when handled or mixed. Also, the pile can heat up if left unattended for an extended period of time.
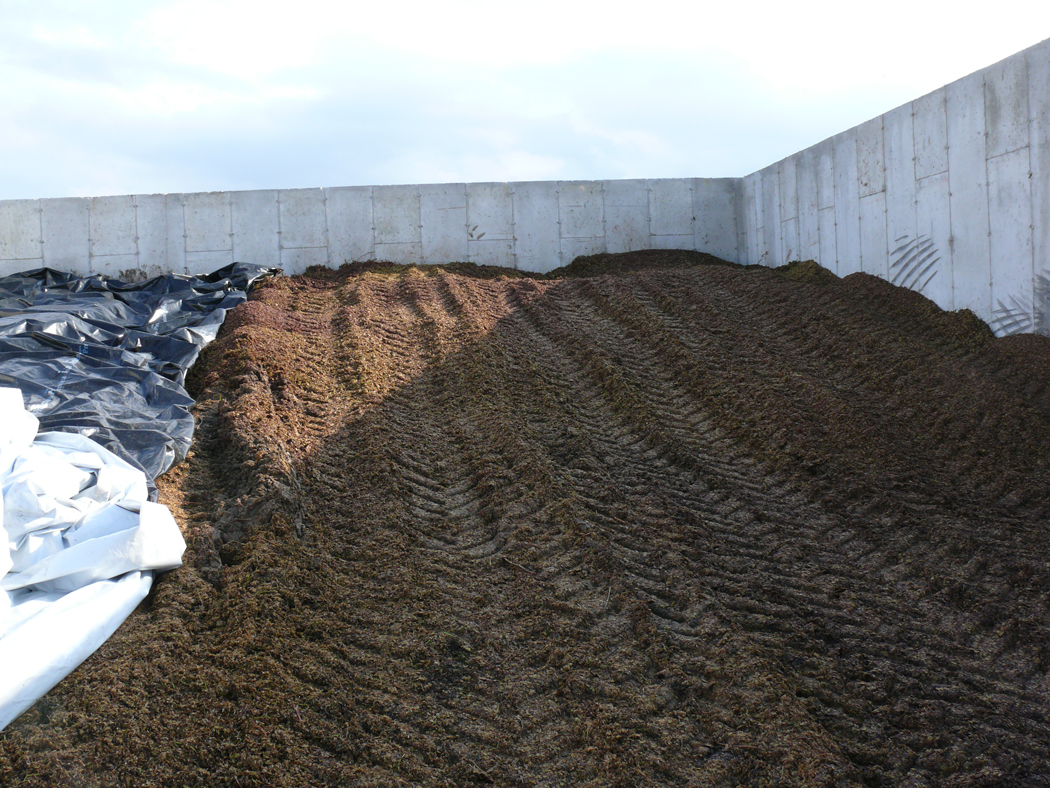
Best management practices to safely store these materials and reduce risk of exposure to H2S include:
- keeping materials out of the rain and manage seepage produced from fermentation
- monitoring pile temperatures for materials sensitive to moisture and fermentation
- storing materials in an open structure to allow for ample natural ventilation
- keeping the operator of the loader outside the storage structure
Biogas equipment
Anaerobic digester with over-under pressure relief valve
The vessel where biogas production occurs is called the anaerobic digester. It is equipped with a safety valve called the over-under pressure relief valve to avoid unsafe gas pressure levels (negative or positive) in the tank. During normal operating conditions, consider the following best practices and design features to minimize risk of exposure to H2S gas:
- Keep ignition sources at least 3 m (10 ft) away from the over-under pressure relief valve to prevent risks of fire or explosion in case of emergency release of raw biogas.
- Regularly inspect the concentration of anti-freeze fluid in the over-under pressure relief valve for liquid sealed valves during freezing conditions due to the possibility of accumulating condensation.
- Minimize the emergency release of biogas through the over-under pressure relief valve by controlling the amount of input material fed to the digester, especially during winter.
- Consider upgrading to a freeze-proof over-under pressure relief valve as shown in Figure 4, as they are easier to maintain and operate.
- At all times, restrict access near the over-under pressure relief valve and post appropriate safety signage.
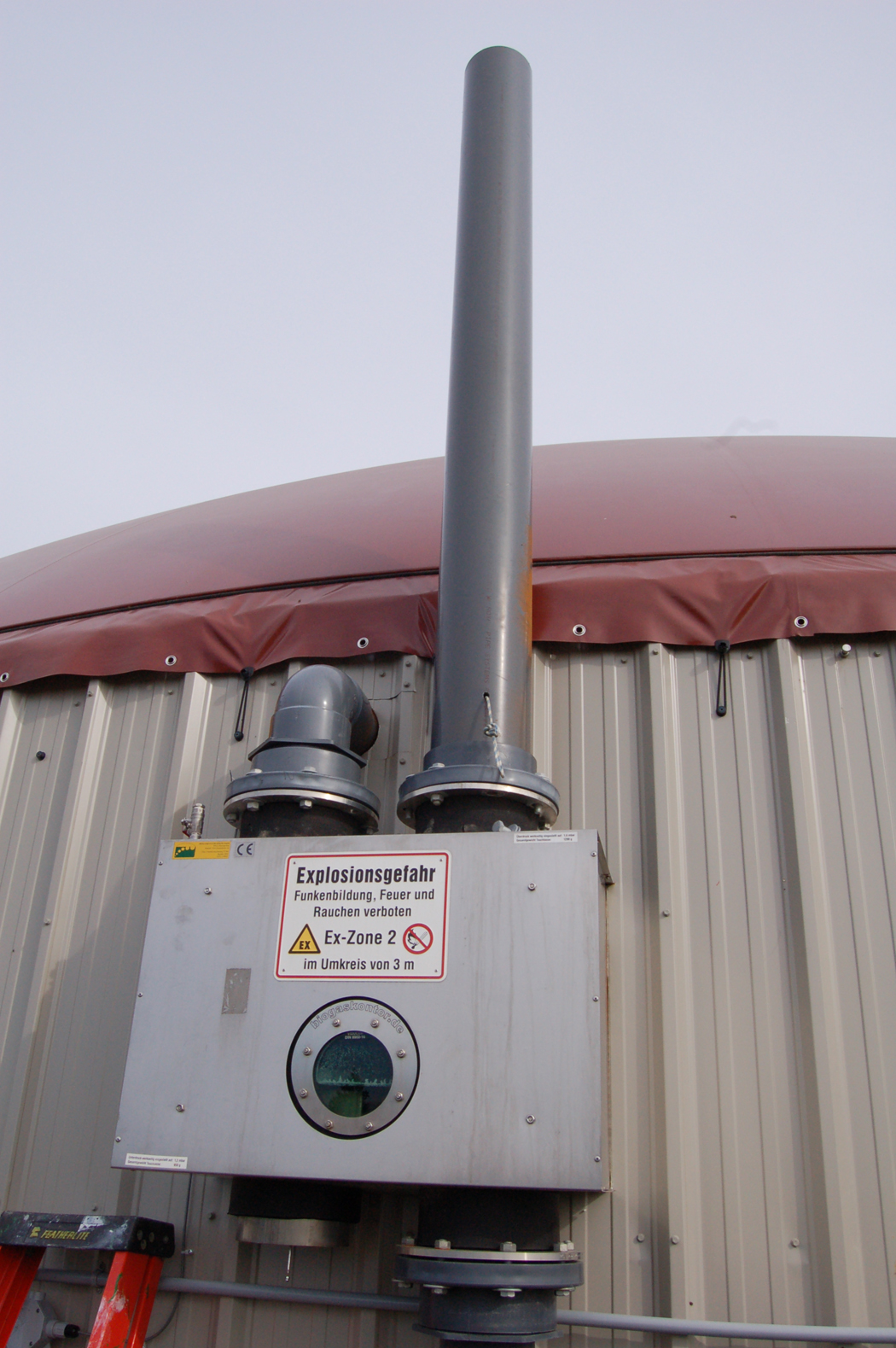
Operators may have to remove the inflatable gas storage membrane or cover to repair equipment inside the anaerobic digester, during certain maintenance procedures. It is essential that operators follow the safety procedures learned in their training due to the hazards encountered.
The anaerobic digester contents continue to produce biogas and H2S even when the cover or gas storage membrane is removed. It is dangerous to enter an anaerobic digester that has recently been emptied. H2S and other dangerous gases will linger at the bottom of the tank and inside the tank’s sediments.
To minimize exposure to H2S and hazardous gases during maintenance procedures:
- Hire contractors who are familiar with H2S and the associated risks, have the appropriate training, have experience with biogas systems, and understand the risks of working in and around confined spaces.
- Hire contractors who have completed training associated with confined spaces and the occupational health and safety regulations.
- Use properly calibrated and fitted personal protective equipment (such as gas monitors, self‑contained breathing apparatus) when conducting maintenance and repairs.
Condensation trap (condensate collection or drip trap)
In most agricultural biogas systems, moisture in the biogas is removed by passing it through an underground network of cooling pipes. The moisture cools and condenses, and is collected at the lowest point in a structure, called a condensation trap (Figure 5). The trap has a high probability of containing H2S, other hazardous gases and low levels of oxygen. Access to this structure must be restricted, as the condensation trap is considered a confined space.
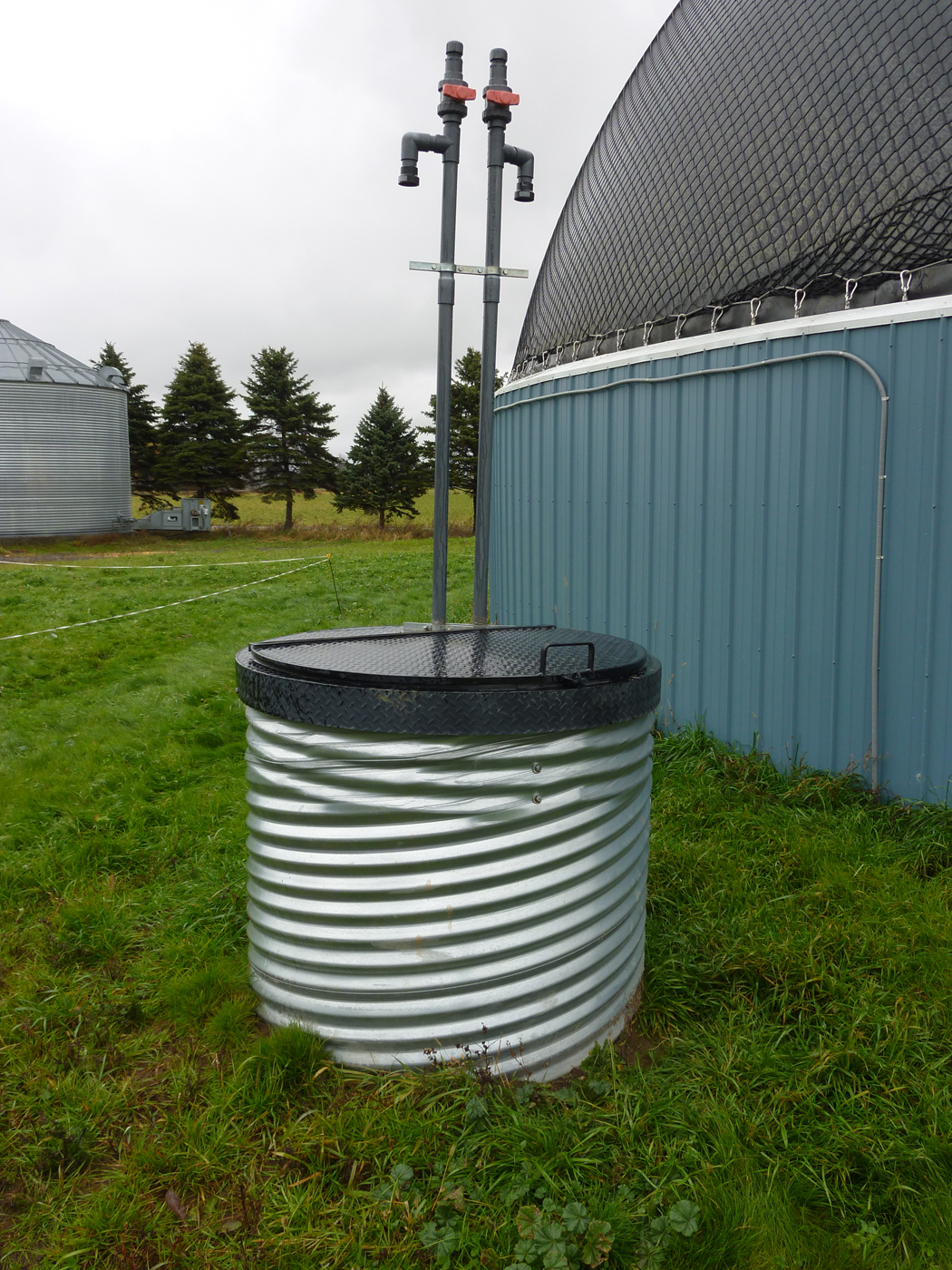
Storage of output (digested) materials after digestion
Liquid digestate storage
Handling liquid digestate for land application is as dangerous as handling undigested manure. Fresh digestate from the anaerobic digestion tank contains active bacteria and will release H2S and other hazardous gases. Although a high fraction of the organic matter is converted to biogas, other organic materials (such as straw and sawdust) decompose slowly during long-term storage and trap H2S in the liquid digestate. Hire an engineer to design the liquid digestate storage (Figure 6) and ensure that H2S and other hazardous gases are:
- vented to the open environment to prevent all possible accumulation and exposure to humans or livestock following the Manure Storage Safety ASABE EP470.1 OCT2011 (R2016)
- contained in a sealed digestate storage and connected to the biogas pipe network of the anaerobic digester
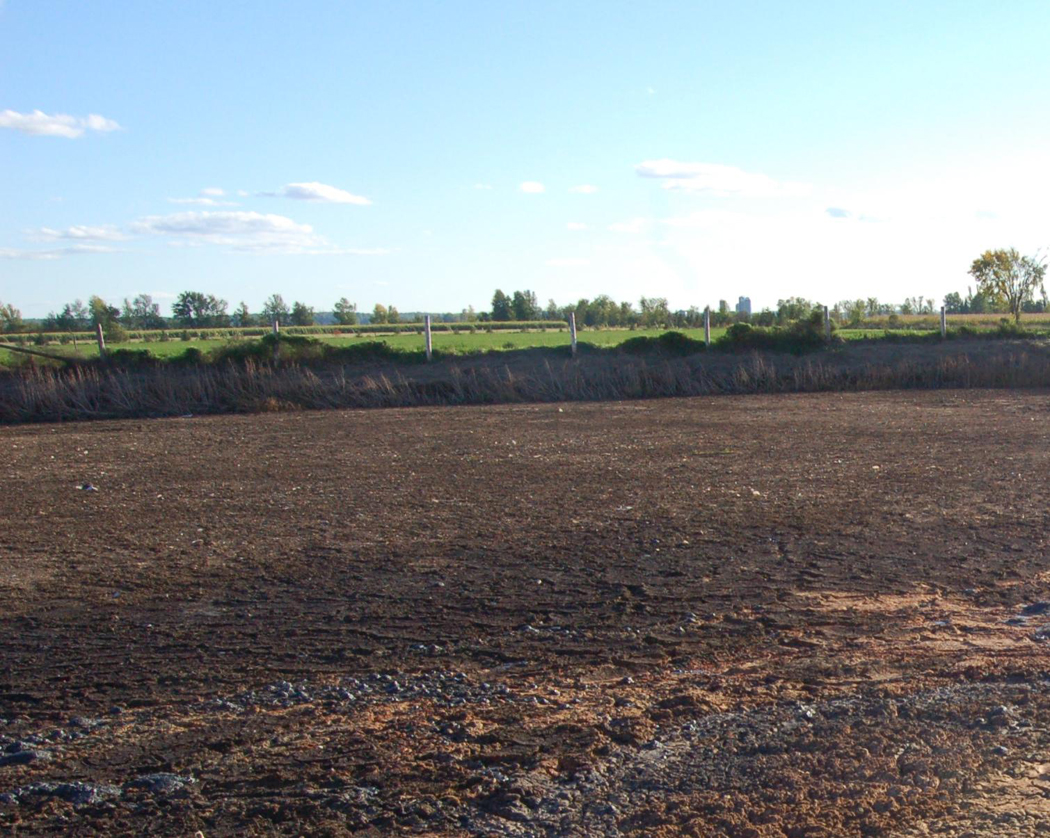
Storing digestate in an under-barn storage, unless it is designed by a professional engineer for that purpose, is not a recommended practice for several reasons:
- H2S and ammonia gases corrode the metallic supports and concrete holding the slats and floor components.
- Methane accumulates in the air space below the slats if not vented safely by a system designed by a professional engineer.
- It is difficult to completely stop biogas production in the storage during maintenance procedures (for example anaerobic digester clean-out or repairs) if it cannot be emptied somewhere else, such as into an open storage tank.
- Off-farm materials cannot be disposed of in the under-barn storage as the fresh organic material present represents a source of food for active bacteria in the digestate. The bacteria will produce H2S and hazardous gases under the floor components.
- Any agitation or removal of digestate from the under-barn storage can create a sudden release of H2S and hazardous gases.
Separated manure solids
Some biogas operators process output digestate materials using a solid manure separator. The separated solid materials are used for bedding, compost or even as a surface cover over feedstock materials. They typically do not sit in the same location for long and are kept away from precipitation; otherwise, the solids may start to ferment. H2S can be trapped in the solids, and exposure must be managed.
To minimize this hazard:
- use the materials for their final purpose as soon as they are produced
- minimize the enclosed area at the separator by allowing ample natural ventilation to occur, ideally outside or in a very open area (Figure 7)
- monitor the temperatures of the piles
- keep moisture out of separated manure solids
- turn compost piles and monitor for adequate moisture, aeration and nutrients
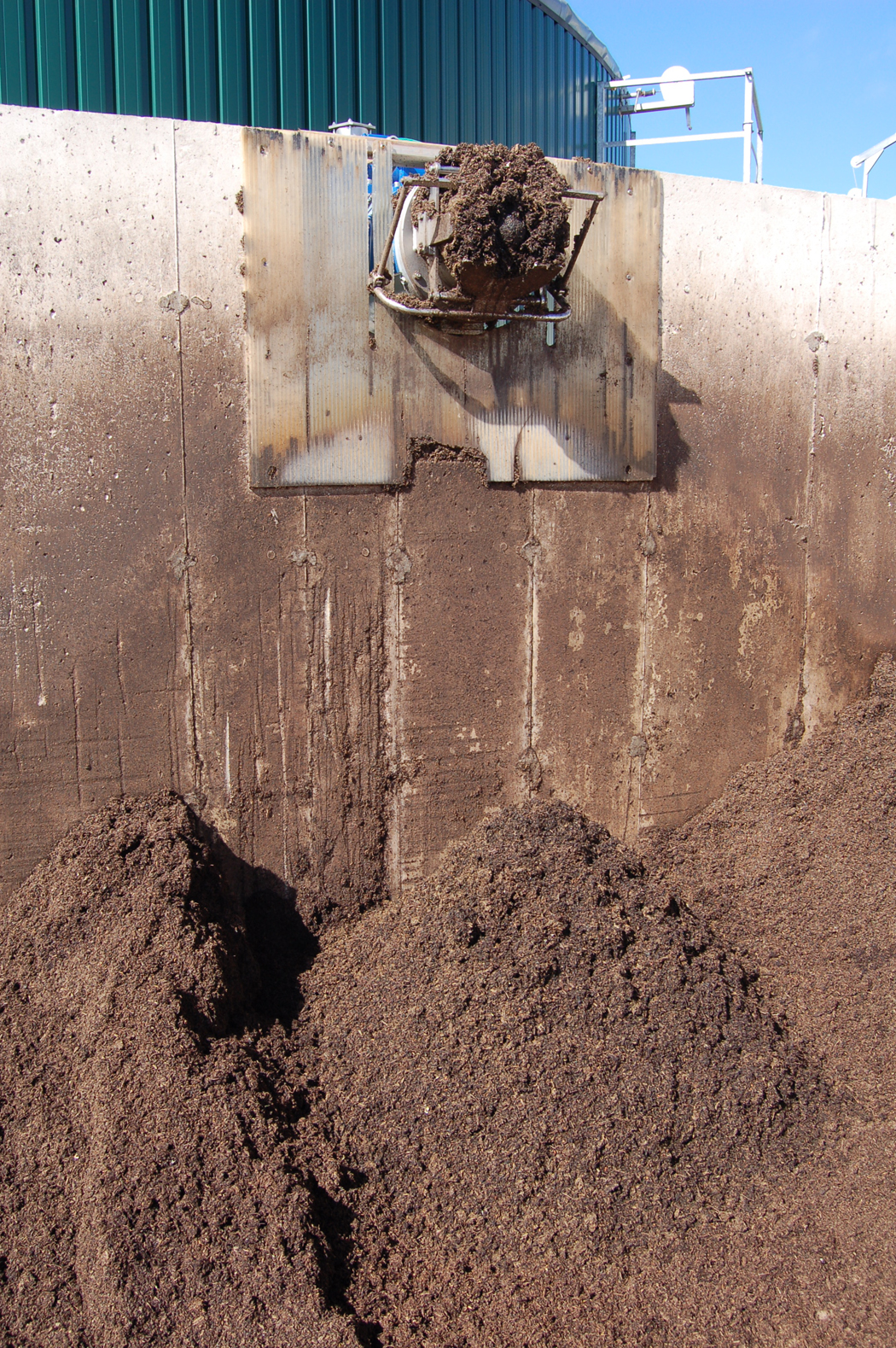
Reducing risk
Certain activities can generate an increased risk of exposure to H2S. These activities include:
- receiving new off-farm materials that the operator has no previous experience with
- mixing new off-farm materials with a different type of off-farm material
- handling off-farm materials that have been stored for a long period of time (especially if they are contained in a sealed unit such as a tanker truck, manure tanker or other sealed/enclosed structure)
To reduce these risks:
- store off-farm materials in structures open to the atmosphere or in vented tanks
- test the materials for chemical and physical properties and be aware of reactivity when mixing the materials
- test the methane potential and determine how quickly it is released when fed to the anaerobic digester
H2S monitors
Hazardous gases are measured with commercial handheld monitors available from safety and scientific equipment suppliers (Figure 8). Gas monitors measure environmental gases constantly, are compact in size and sound an alarm when a dangerous gas level is detected. When purchasing a gas monitor for H2S, verify whether the unit can be calibrated at the farm or has to be serviced. Certain units will stop working if the calibration has expired. Operating the calibrating equipment can be done with minimal training. Prices for H2S gas monitors can range from $350 to $600.
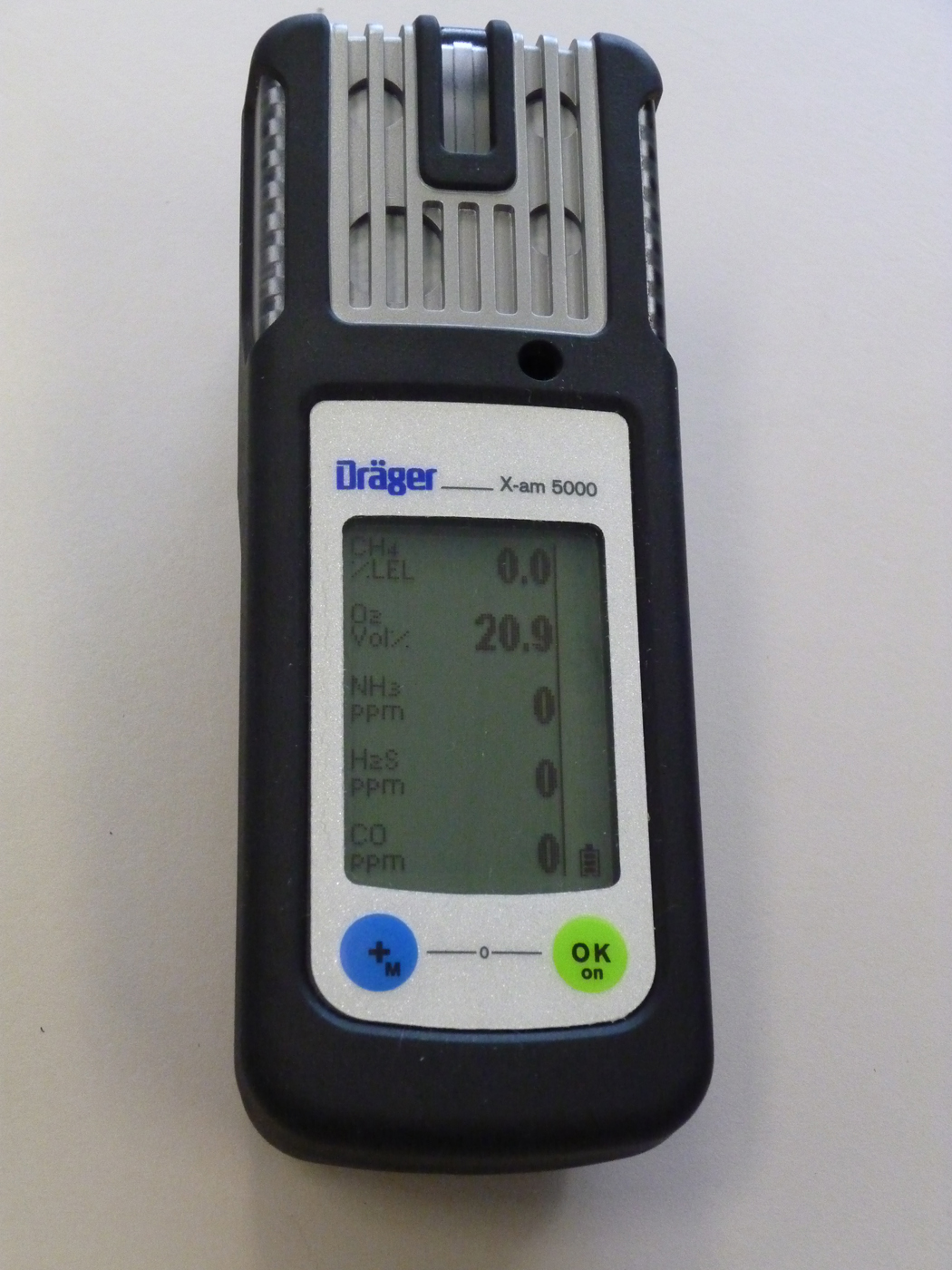
Guidelines to manage H2S exposure
There are many confined spaces on the farm where hazardous gases are a risk. See Section 7 of Health and safety in farming operations. Section 7 lists requirements for confined spaces in agricultural operations and offers sample procedures to minimize exposure.
Conclusion
H2S is considered a very dangerous gas that is generated as a by-product in agricultural anaerobic digester systems and other manure storage systems, such as storage under fully slatted barns. Keep the following tips in mind when approaching a situation where H2S is found:
- H2S sinks to the ground and the bottom of tanks and may go unnoticed. Do not rely on the sense of smell to detect dangerous levels of H2S.
- The release of H2S is relatively low when manure remains undisturbed. However, H2S levels can reach dangerous levels very quickly when a tank is agitated, especially if splashing or surface agitation occurs.
- When working around sources of H2S, wear a properly calibrated H2S gas monitor with an alarm. Certain gas monitors may need to be “bump tested” daily before use. Set the alarm at 10 ppm. Vacate the premises immediately if the alarm sounds and assess the risk with other trained workers before taking next steps.
- Post a “Danger, Deadly Gases” warning sign in sites where H2S is present and in a visible location. These signs are available from most retail or online safety supply shops. Control and restrict access to structures where H2S is present.
- When working around input (feedstock) and output (digested) material structures, ensure access doors remain fully open to provide maximum natural ventilation. Work from the outside of the structure as much as possible. Operators should not mix input and output materials in an enclosed structure without adequate ventilation for H2S and other hazardous gases.
- Multiple deaths have occurred when workers have entered manure storages or a room above them due to gas exposure. Do not attempt to save someone who has been overcome by H2S. Instead, provide ventilation to the victim and call for emergency services immediately.
- Preparing a health and safety policy and program at each farming operation will help reduce exposure to H2S and prepare for emergencies. Contact Workplace Safety and Prevention Services (formerly known as Farm Safety Association) toll-free, at
1-800-361-8855 , if you are located in Ontario.
This fact sheet provides basic awareness information on H2S found on agricultural operations with biogas systems. This document does not intend to provide assurance of compliance with occupational health and safety regulations in Ontario. Contact a biogas system’s engineer for specific technical questions.
References
Enform Canada. 2007. H2S Alive Hydrogen Sulphide Safety Training. Sixth Edition.
This fact sheet was written by Terrence Sauvé, P. Eng., farmstead optimization and safety, OMAFRA and reviewed by Anna Crolla, P. Eng., energy and crop systems, OMAFRA, Chris Duke, biogas program analyst, OMAFRA and Jake Debruyn, P. Eng., new technology integration, OMAFRA.