Using less energy on dairy farms
Learn about how to use less energy on dairy farms. This technical information is for Ontario dairy farmers.
ISSN 1198-712X, Published September 2010
Introduction
OMAFRA recommends alternative designs to tie-stalls for new construction. Producers should exercise caution when considering the construction of a new tie-stall barn. We continue to recommend using available information and best practices to improve cow comfort and efficiencies within existing tie-stall barns. However, given the depreciation period and lifespan of a new barn, consider investigating alternative housing systems for long-term viability.
Dairy farms use a lot of energy, but there are many opportunities on a dairy farm to reduce energy use and save money.
Energy benchmarking
Research on dairy farms in Ontario found that, on average, dairy farms used 800 – 1,400 kWh/cow/year.
These values are used to compare overall energy use between farms and establish a benchmark for evaluation. All energy benchmark values in Table 1 are significantly higher for the tie stall farms.
The wide span of energy-use-per-cow values in each category of farm indicates that there is the potential to conserve energy and push the top values down. For comparison, the average Ontario household uses around 12,000 kWh per year – the equivalent to what 10 dairy cows use per year on an average farm.
There are many ways to further reduce energy use on a dairy operation. The Ontario study found five areas of dairy operations that accounted for almost 90% of the electrical energy used:
- milk cooling
- vacuum pumps
- water heating
- lighting
- ventilation
Free stall dairy | kWh/cow/year | kWh/hectolitre |
---|---|---|
Maximum | 1,009 | 14 |
Average | 837 | 8 |
Minimum | 571 | 5 |
Tie stall dairy | kWh/cow/year | kWh/hectolitre |
---|---|---|
Maximum | 1,946 | 20 |
Average | 1,417 | 14 |
Minimum | 668 | 7 |
Consider reducing energy use in these areas. Energy is used mostly for milk production (milk cooling, vacuum pumps and water heating) and lighting, the second-largest reason for energy consumption on dairy farms. Figure 1 shows an overall average energy use profile for audited dairy farms in Ontario.
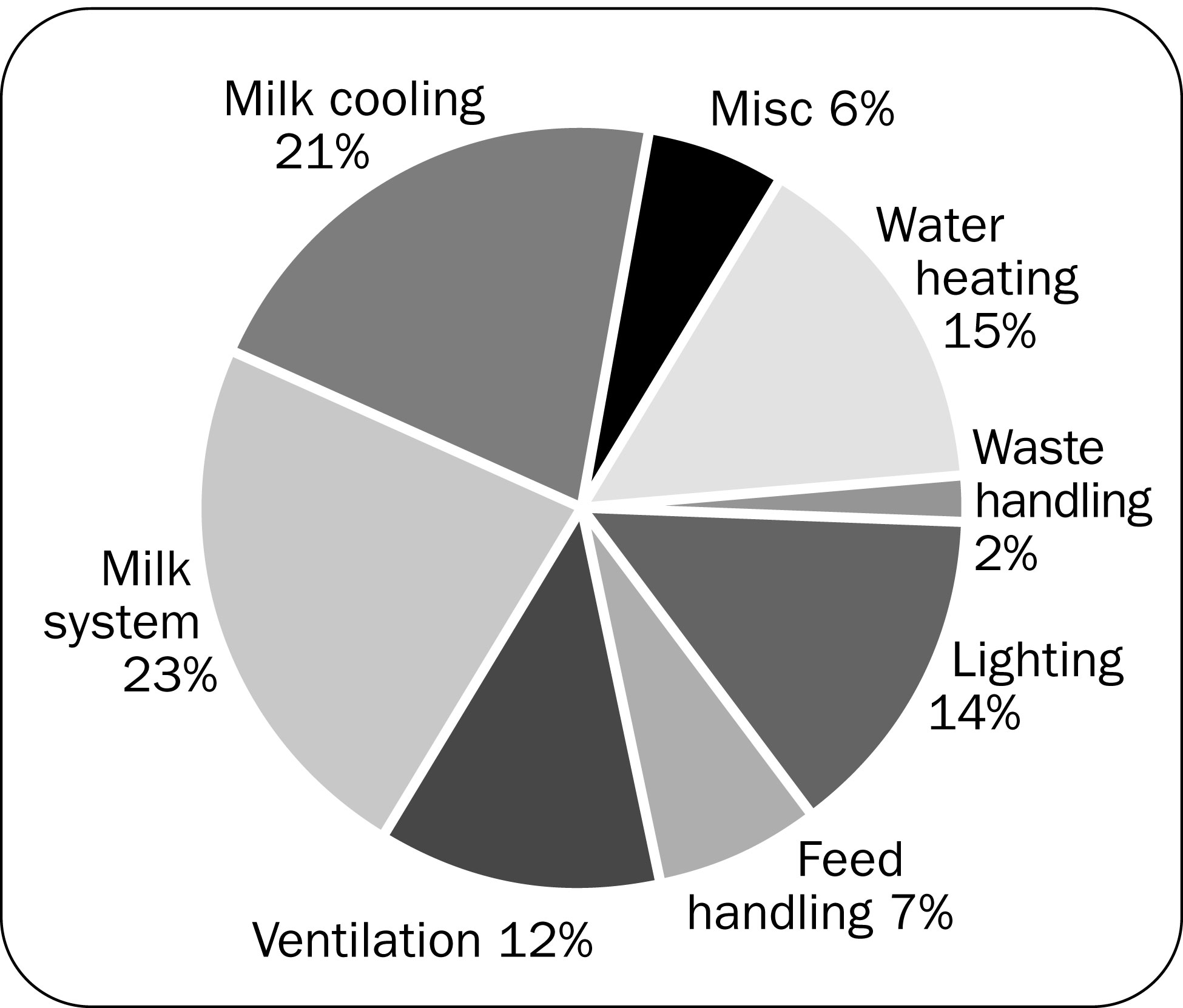
- Milk system - 23%
- Milk cooling - 21%
- Water heating - 15%
- Lighting - 14%
- Ventilation - 12%
- Feed handling - 7%
- Misc - 6%
- Waste handling - 2%
Milk cooling
Cooling milk is where most of the energy is used. Fresh milk must be cooled from 37˚C to 4˚C within 1 hour of the end of milking, so it can be stored until it is picked up by the milk truck. This means that the bulk tank condenser unit must extract a lot of heat, quickly, to make the process efficient. This process uses a lot of energy and produces a lot of heat. There are real potential energy savings if the heat can be recovered and used again.
Milk pre-cooler systems
Milk pre-cooler or well water pre-cooler systems remove heat from the milk before it enters the bulk milk tank (Figure 2). Pre-coolers are installed on the milk line and operate as heat exchangers through which water flows to partially cool the milk.
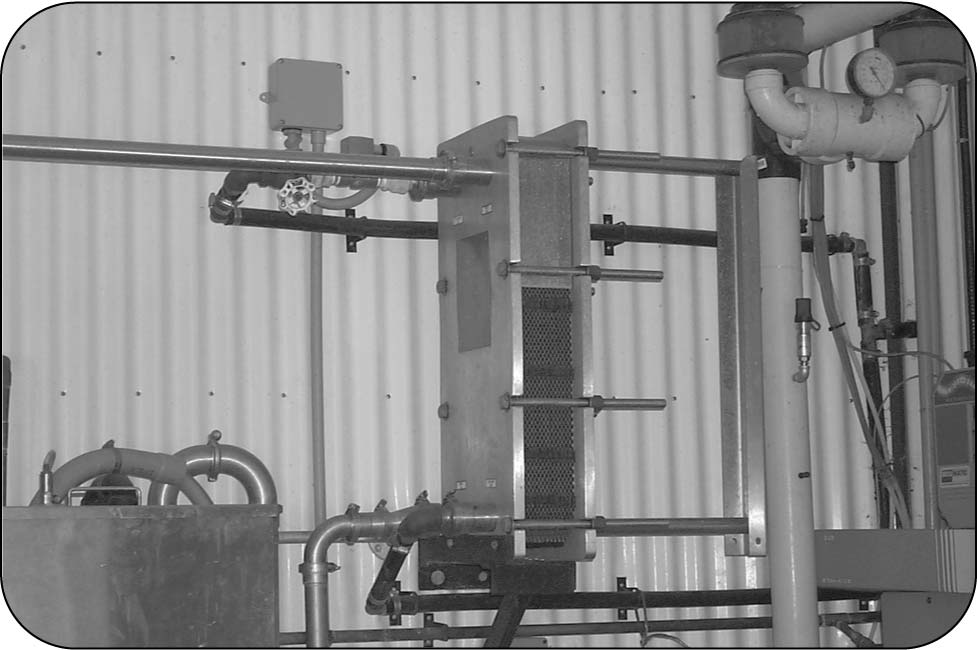
The most common type of pre-cooler consists of a series of stainless steel plates separated by gaskets that form flow channels on opposite sides of each plate. Cool well water flows down the channel on one side, while warm milk flows up the other side. The milk's temperature drops as it transfers its heat to the cool water on the opposite side of the plate. The plate heat exchanger is extremely efficient for fast pre-cooling.
When properly installed, a pre-cooling system that uses a 2:1 flow rate (two parts water to each part of milk) can get the milk temperature to within 2˚C of the water temperature. Lower well water temperatures result in additional cooling. Higher water temperatures do not give as good results.
The well water, which warms up 7˚C–9˚C, can be used for watering the cows – in warm weather, cows will drink 3–4 L of water for every litre of milk produced. Otherwise, it can be discarded or used for washing equipment or washing down the parlour and holding area floor.
The pumping rate for water depends upon the milking rate. If the 2:1 ratio is selected, the water pump and well must supply water at twice the milking rate, measured in litres or gallons per minute. It is important to make sure that the well can supply water at this rate.
By using milk pre-coolers, bulk tank condensers run for a shorter time to cool the milk at higher pumping rates, resulting in electricity savings. However, it may be difficult to justify the costs of the pre-cooling system based on these savings alone.
The money saved by installing an in-line cooler depends on several factors such as herd size, number and size of compressors, type of refrigerant used and the age of the bulk tank. It is estimated that the investment will pay for itself in as little as 2 years.
Milk heat reclaimers
Once the milk enters the bulk milk tank, it must be cooled to preserve its quality. The air-cooled condensers typically used for this process are not as energy efficient as water-cooled condensers, which can recover 20%–50% of the heat removed from the milk.
There are two types of water-cooled condensing systems:
Total water-cooled condensing system. Water is used to cool the condenser and the condenser motor, then fed into the hot water system. In general, 1 L of milk will produce 1 L of hot water at approximately 46˚C. Large amounts of warm water are produced by this system. Excess warmed water may be fed to the livestock or discarded. The compressor can be designed to switch to air cooling when the cooling water reaches a certain temperature, making the system more energy efficient.
Refrigeration heat recovery unit (RHR). RHR is an add-on recovery unit that is connected to the refrigerant line of an existing or new air-cooled system (Figure 3). These systems remove much of the superheat from the compressed gaseous refrigerant; however, the air-cooled condenser must remove the residual heat. The pre-warmed water is stored in a tank. The storage tanks range in size from 190–450 L. Common brand names are Therma-Stor, Heat-Bank, Fre-Heater, Century-Therm, SuperHeater.
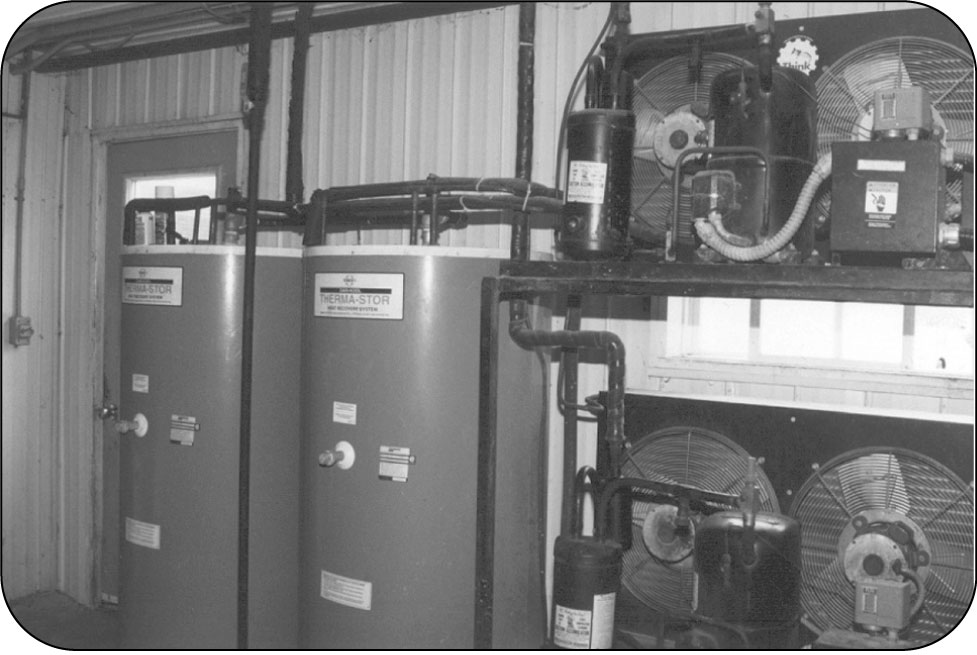
Pros and cons of a milk pre-cooler system
If you use electricity to heat water, heat recovery may help reduce water heater expenses. However, a number of factors dictate whether a milk pre-cooler can be incorporated into a system.
The water well's capacity to provide water (flow and amount) is important. For a constant-speed milk pump, use a water-to-milk volume ratio of 2:1. Milk flow rates are shown in Table 2.
For a 1-hp milk pump, the milk flow rate is 160 L/min (35 gpm) and the water flow rate is 320 L/min (70 gpm), using the 2:1 ratio.
Horsepower | Typical flow rate L/min (gpm) | 2:1 Water flow rate L/min (gpm) |
---|---|---|
½ | 110 (25) | 230 (50) |
¾ | 135 (30) | 270 (60) |
1 | 160 (35) | 320 (70) |
2 | 205 (45) | 410 (90) |
3 | 270 (60) | 540 (120) |
Existing water pipe size may also limit the water flow rate. Table 3 shows the maximum flow rate, at 275 kPa (40 psi) water pressure, for water pipes of various diameters.
Table 3 shows the minimum water pipe diameter as 32 mm (1¼ in.) for a 30-m (100-ft) pipe and a flow rate of 320 L/min (70 gpm). If these physical conditions cannot be met or would incur large expenses to achieve, a pre-cooler may not be cost-effective.
Pipe diameter mm (in.) |
Flow rate L/min (gpm) 15-m (50-ft) Length of pipe |
Flow rate L/min (gpm) 30-m (100-ft) Length of pipe |
---|---|---|
13 (½) | 40 (9) | 30 (6) |
19 (¾) | 120 (27) | 80 (18) |
25 (1) | 250 (55) | 180 (39) |
32 (1¼) | 450 (100) | 320 (70) |
Heat reclamation from the compressor is almost always a worthwhile investment because of the lower water heating costs, which are normally reduced by up to 50%. Disadvantages of heat reclaimers include the need for regular maintenance for optimal performance and the loss of heat to keep the milk house warm in the winter, although there is usually more heat available than is needed to heat water.
Pre-coolers and RHR units are competing technologies. Heat removed with a pre-cooler cannot be used for water heating. Typically, either an RHR unit or a pre-cooler will be economical for farms with less than 100 cows, but not both. For farms with more than 150 cows, usually both will be economical, although this depends on energy costs.
Variable speed drives
Milking equipment is one of the biggest energy users on dairy farms. Variable speed drives (VSDs, also known as variable frequency and adjustable speed drives) may be used on the vacuum pump and milk pump.
Vacuum pumps
The VSD attaches to the existing vacuum pump to constantly monitor the vacuum level and change the motor speed accordingly. On the vacuum pump, savings for existing systems of at least 50% (65%–70% is typical) can be achieved. For designs based on the new specification, savings can be as low as 30%. This system maintains the vacuum level by adjusting the motor speed (Figure 4).
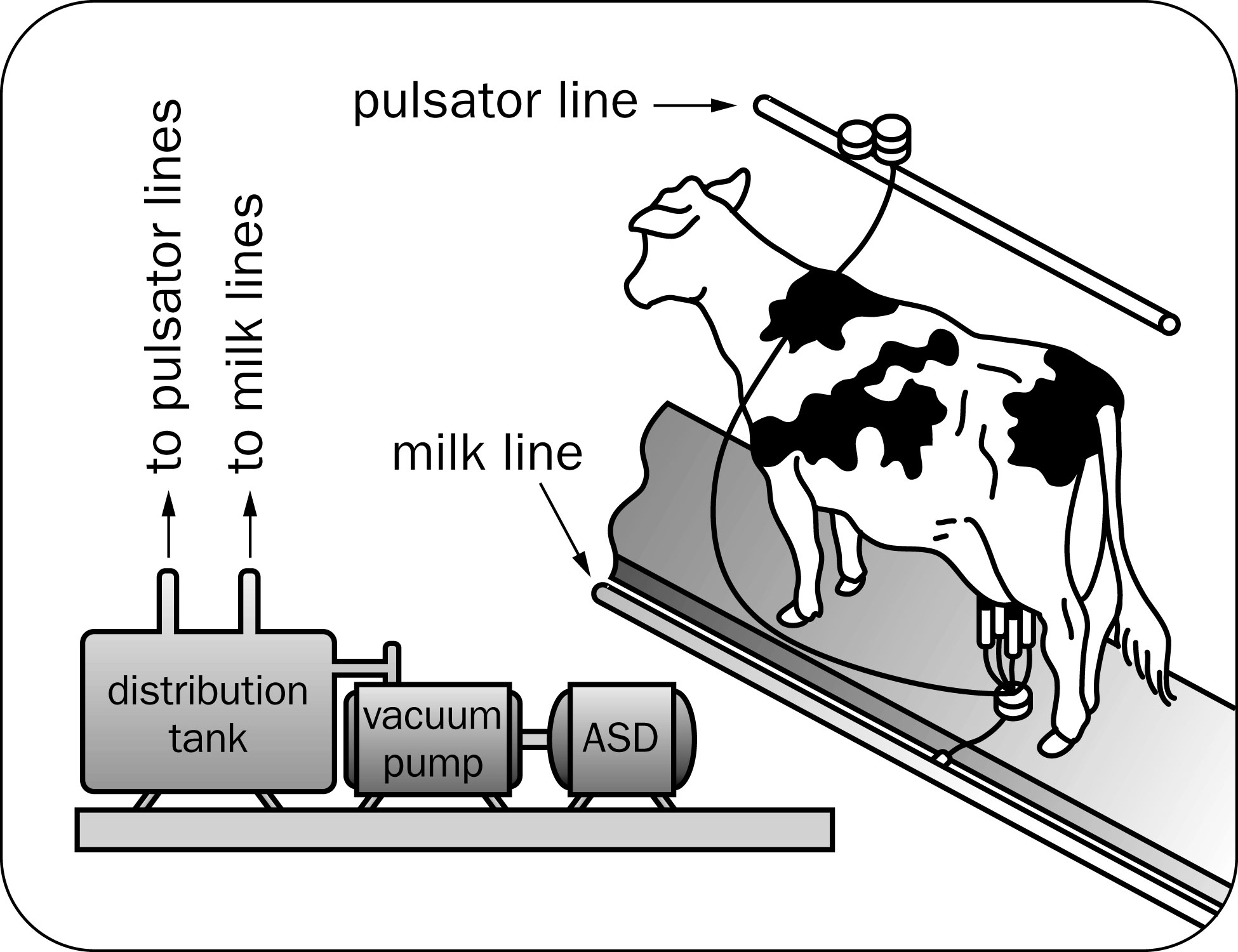
In a vacuum pump upgrade, a farmer changed from two vacuum pumps with a 7.5-hp motor each (Figure 5) to a vacuum pump with a 10-hp motor and vari-speed control (Figure 6). This switch resulted in a 5-hp upfront savings and an additional saving on the vari-speed control. The second vacuum pump with a 7.5-hp motor was kept for back-up.
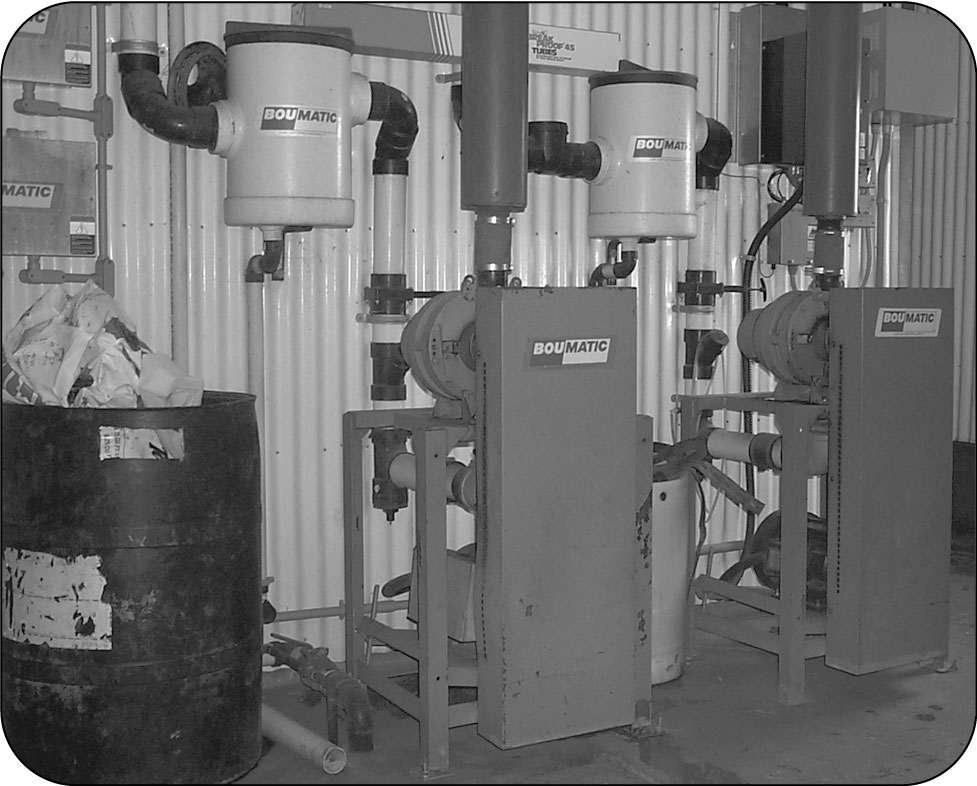
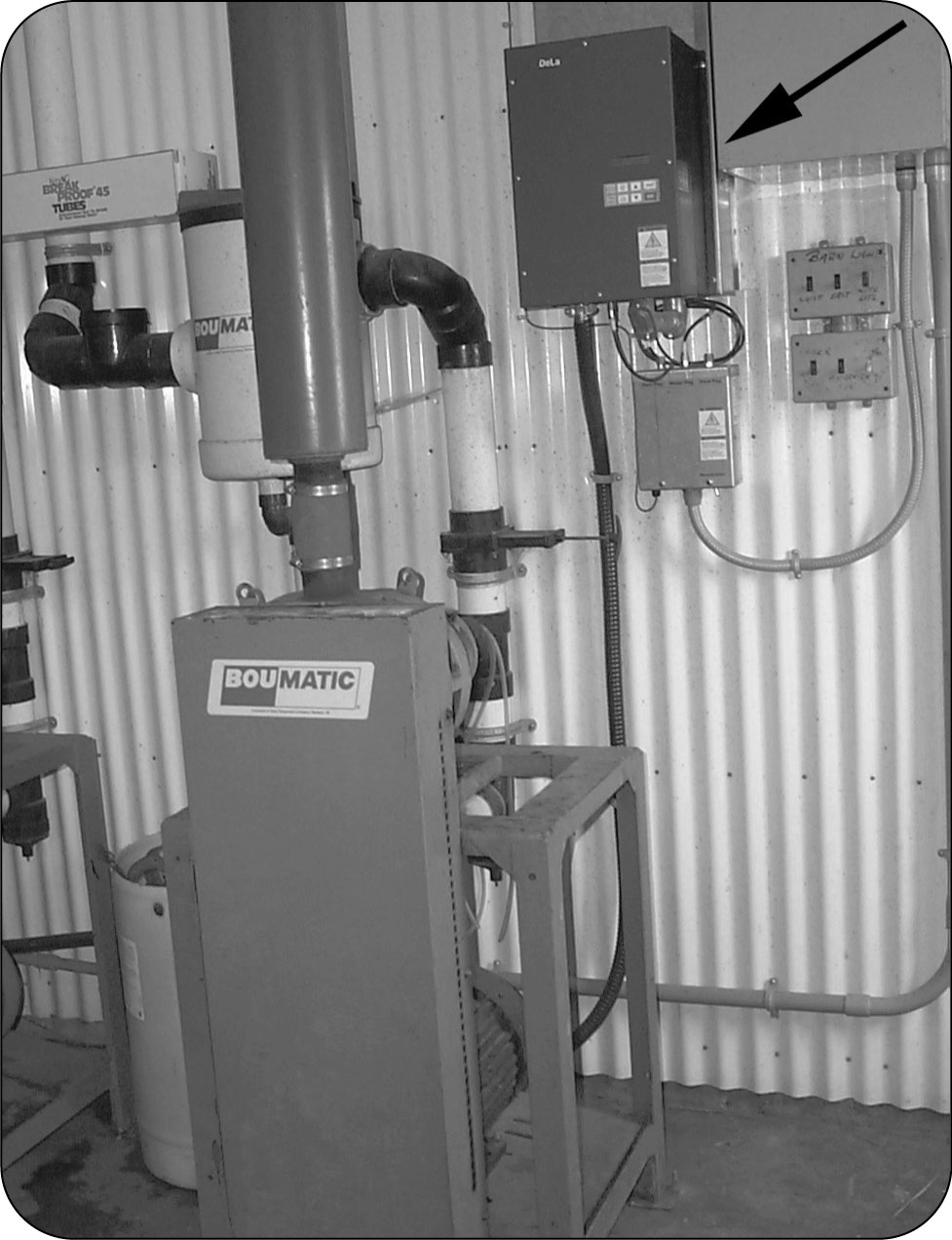
When to use a variable speed drive
Table 4 provides a general guideline on daily hours of use of the vacuum pump to give the variable speed drive a reasonable payback period of 5 years. Actual payback varies depending on conditions on the farm, the price of electricity and the capital cost of the VSD.
Milk pumps
A variable-speed milk pump is used as an accessory to a pre-cooler or well water–cooled heat exchanger. A variable–speed milk pump slows the milk flow through the plate cooler, which results in a higher water-to-milk flow ratio and more cooling of the milk in the pre-cooler. Refrigeration compressor run time is reduced. The variable speed feature replaces the standard on/off liquid level controller. It allows the milk level in the receiving jar to be maintained by turning the milk pump speed up or down. The energy savings associated with this type of system vary with pump size and hours of use per day.
Vacuum pump size (hp) |
Minimum operating (hours per day) |
---|---|
5 | 12 |
7.5 | 8 |
10 | 6.5 |
15 | 5 |
20 | 3.5 |
Note:It is very important to have variable speed controllers wired and installed correctly to avoid problems with transient voltage.
Scroll compressors
The scroll compressor is a simple design of two scrolls – one that oscillates and another that is fixed – that compress and move refrigerant more efficiently and reliably than traditional compressors. Gas refrigerant is compressed when one spiral travels around a second standing spiral, creating smaller and smaller gas pockets and higher gas pressures. By the time the refrigerant is released, it is fully pressurized. Suction is continuous and pulse-free because all gas pockets are in various stages of compression at all times.
A scroll compressor can result in reduced energy costs. Scroll compressors require less current than regular compressors and can run on single-phase electricity. A scroll compressor runs at a lower decibel level and vibrates less than a reciprocating compressor. Scroll compressors last longer than conventional compressors. With only one moving part and no metal-to-metal contact, there are no seals to tear and no lubrication needed.
Scroll compressors use 15%–20% less electricity than standard compressors. Additional benefits of scroll compressors in today's dairies include:
- quieter
- fewer breakdowns
- longer life
Tip: Keeping air-cooled condensing units clean can result in a 3%–5% reduction in energy use.
Electric water heater
Connect the water heater to a timer to ensure water is not heated unnecessarily. Purge 9–14 L (2–3 gal) twice yearly from the drain tank of the water heater. Convert to a high-efficiency gas, oil or propane heater/boiler system. Insulate the water heater and at least the first 6 m (20 ft) of pipe from the water heater. Consider installing a solar hot water system.
Lighting systems
Lights that operate daily for long durations year-round have faster paybacks than lights that are only turned on for a few minutes a day. The quicker the payback, the more appealing an energy-efficient lighting system is for most farm owners and managers.
The best type of system depends on a number of factors including room temperature, mounting height, size of area to be lit and payback period. Energy costs from light systems can be reduced by 15%–75%.
An easy way to switch to a more energy-efficient lighting system is the replacement of incandescent bulbs with compact fluorescent lamps (CFLs) with equivalent light output. The compact fluorescent system is screwed into the existing socket; no rewiring is needed.
Some CFLs have a rated life of 10,000 hours. Other energy-efficient lighting systems require more effort. Installation of the tube fluorescent or high-intensity discharge (HID) lamp systems requires rewiring and a lighting design to ensure that the area is evenly lit at the right light intensity.
CFLs come in a range of power ratings, from 5–42 W screw-in versions and up to 55 W in hard-wired models. As a guide, a 4:1 ratio, incandescent-to-CFL wattage, yields equivalent light output. Generally, compacts are a good, low-cost retrofit. CFLs for barns need to be approved for damp locations (Figure 7).
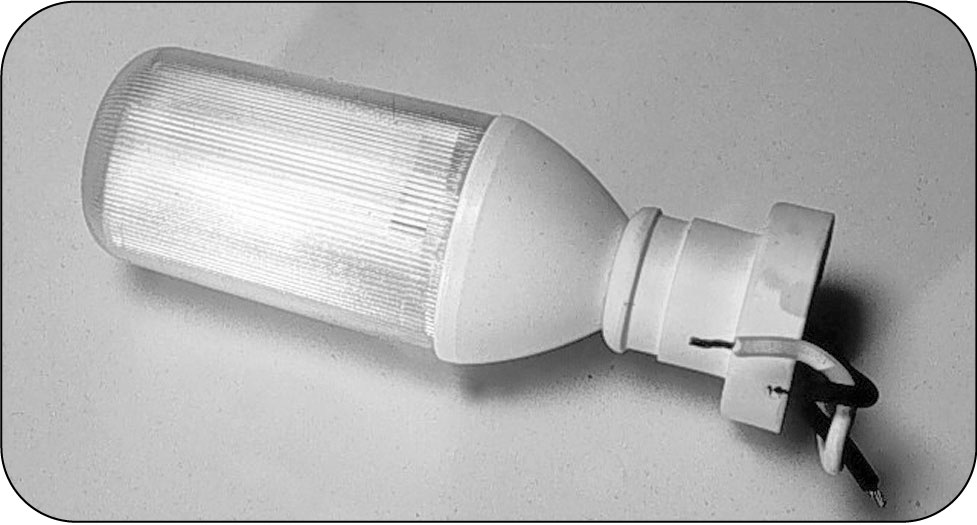
Incandescent lamps are cost-effective where lights are only turned on occasionally, such as in storage rooms. Fluorescent tube systems are well suited to areas such as tie stall, free stall or loose housing barns and some parlours with high ceiling heights
Fluorescent tubes come in a variety of lengths and diameters and are typically rated for 20,000 hours. Typically, farms use 1.2-m (4-ft) lengths. Tube diameter is measured in multiples of an eighth of an inch. T12s (3.8 mm (1.5 in.) diameter) – the old standard – are being replaced by T8 and T5 tubes.
The new recommendation for barns where the ceiling height is less than 3.6 m (12 ft) is the T8 fluorescent fixture with electronic ballast, mounted in weatherproof fibreglass or plastic housing with a continuous gasket between the lens and the fixture (Figure 8). These units are more than four times as efficient as regular incandescent lights and up to 30% more efficient than T12 fluorescent tubes.
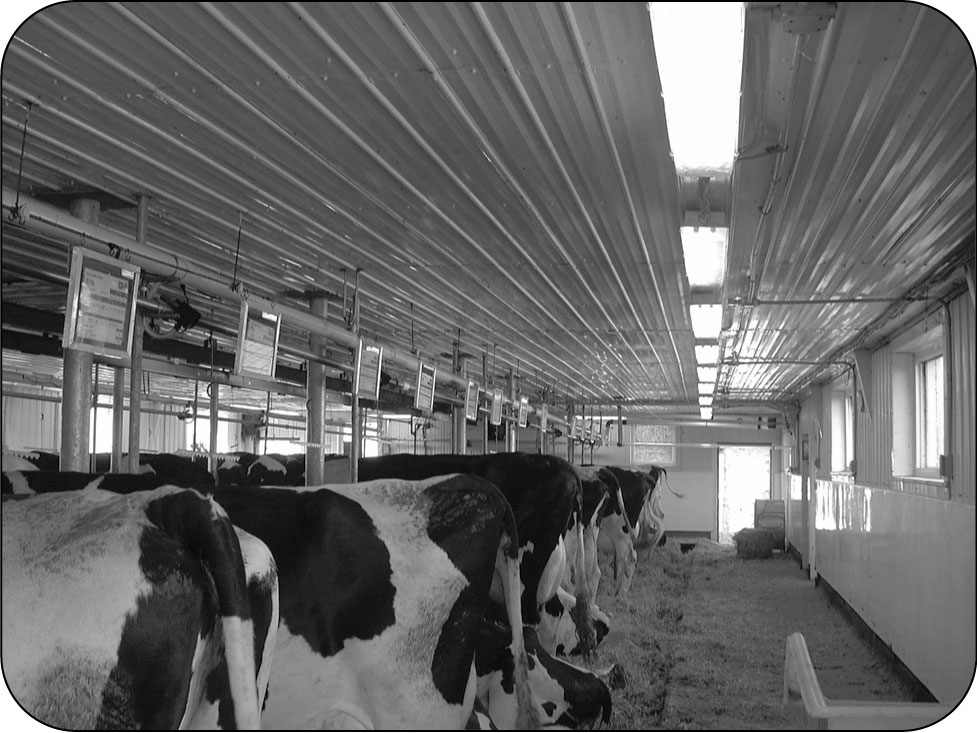
The lamps last at least 20 times longer than regular-life incandescent lamps and are an ideal energy-efficient alternative to incandescent, compact fluorescent and T12 fluorescent systems. T5 is more efficient than T8 and is commonly installed in barns where the ceiling height is greater than 3.6 m (12 ft).
In areas requiring high-pressure washing, waterproof fixtures are required to prevent moisture from getting into the T8 and T5 fixtures.
Ventilation
In a dairy facility, the best way to reduce energy used for ventilation is to maximize natural ventilation whenever possible. In barns ventilated by fans, choose high efficiency fans. Always look for AMCA (Air Movement and Conditioning Association), University of Illinois BESS–tested fans or independent fan performance data. Buy rated fans and properly size the fans and corresponding air inlets based on good design principles. A recent innovation for hot weather cooling in dairy barns is the high-volume, low-speed (HVLS) ceiling fan (Figure 9).

These fan units may be up to 7.2 m (24 ft) in diameter and are operated by a 1–2-hp motor. While the units are expensive to purchase, the payback period falls into the 4–5-year range, depending on the electricity prices and installation costs at the time.
Regular maintenance and cleaning of the whole ventilation system will pay off with reduced energy costs in the range of 15%–50%. Regular maintenance and cleaning will also reduce repair and replacement costs – for instance, dirty fan blades and louvers can reduce fan capacity by more than 40% (Figure 10). Regular ventilation inspection will ensure that fans will operate at full capacity. Figure 11 shows a fan with blades broken off; the fan is exhausting little or no air.
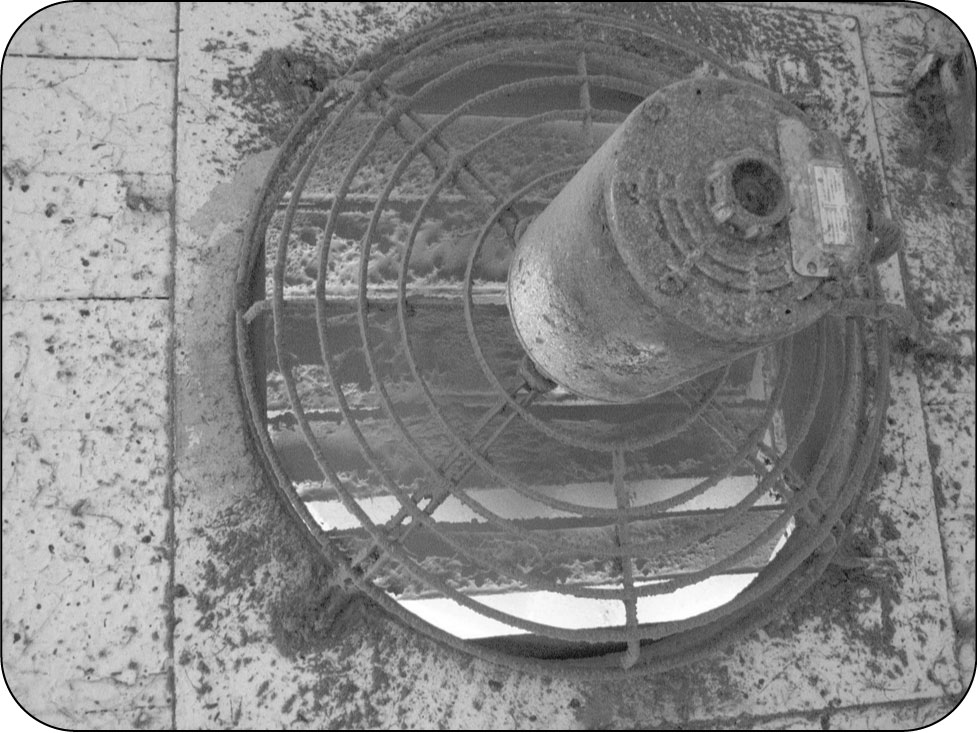
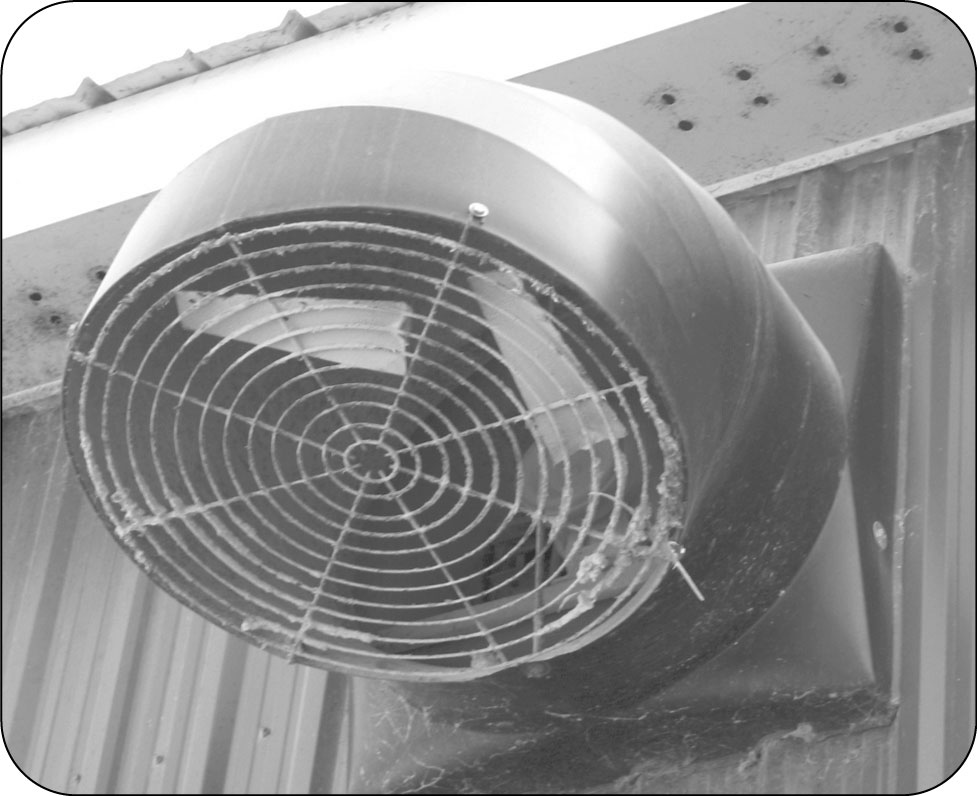
Energy-efficient waterers
Keeping livestock drinking water from freezing is an important task on a dairy farm. In the winter, protect water bowls from freezing unless they are in a heated area. Water bowls can be electrically heated (Figure 12) or frost- (energy-) free (Figure 13) in dry cow/heifer barns.
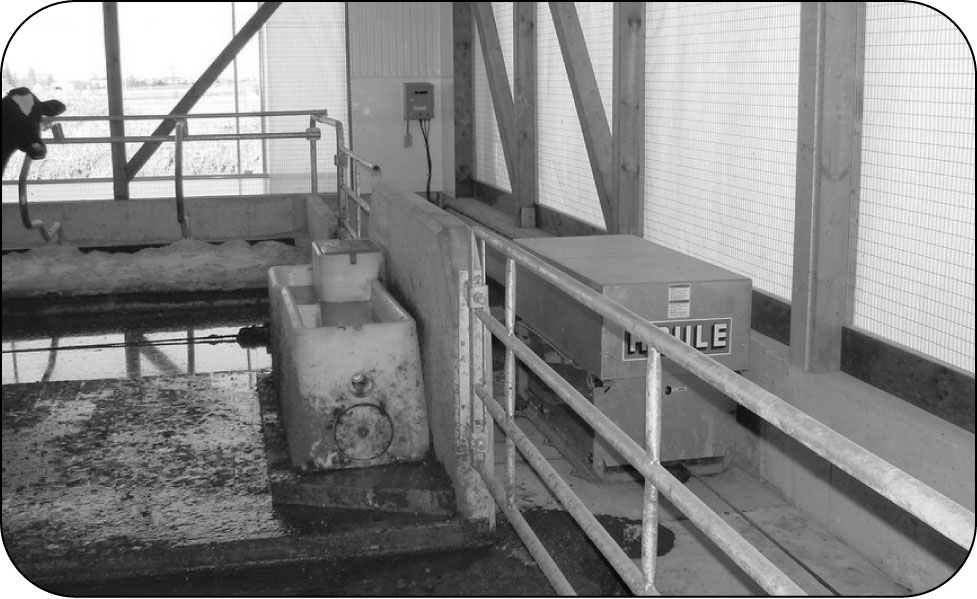
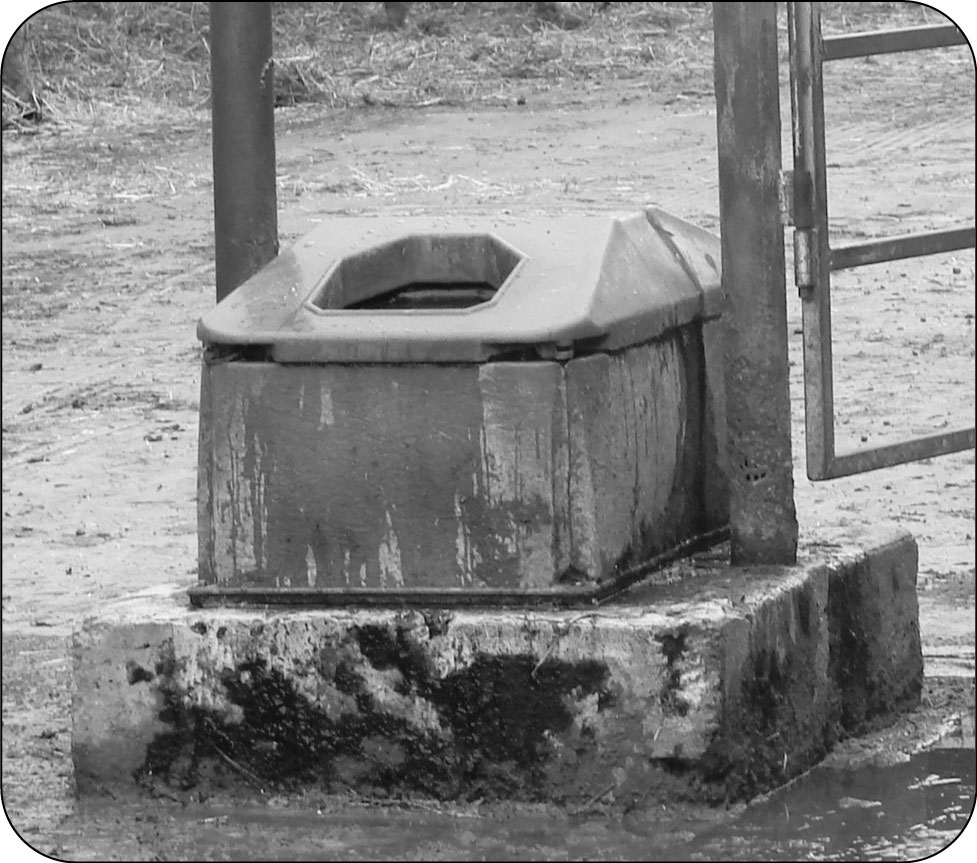
Heated systems rely on a power source (electric, natural gas, propane, solar, etc.) to heat the pipe and water in the tank. The use of insulation contains the heat and improves the energy efficiency.
Energy-free systems make use of geo-thermal energy to keep the water from freezing. A dry well or riser pipe surrounds the water supply pipe. The dugout, which holds the water, is well insulated. The circulation of fresh water through the pipe and tank keeps the system from freezing. Size this system properly to ensure adequate circulation of the water. If there are not enough cattle, circulation may be inadequate and freezing can occur.
Cows prefer to drink from open surfaces. Therefore it is preferable to use an insulated, heated waterbowl, than one where the water surface is protected with an insulated lid or ball. For cold, dry cow or heifer housing where the animals are not drinking as much water, the energy-free water bowls are a good alternative to adding heat.
Conclusion
This Factsheet outlines areas on dairy farms where energy can be saved. In particular, upgrading milking equipment such as milk pre-coolers and using vacuum pump technology and scroll compressors can result in a 30%–50% savings. Maintaining, cleaning or using energy-efficient ventilation systems can result in a 15%–50% savings, and using energy-efficient lighting systems can resulting in a 15%–75% savings.
Check with local electrical utilities to see if there are any financial incentives for any of these energy-saving technologies
This factsheet was written by S. Clarke, P. Eng., (retired), Energy and Crop Systems Engineer, OMAFRA, Kemptville and H. House, P. Eng., (retired), Dairy and Beef Housing and Equipment Engineer, OMAFRA, Clinton.