Item 2: Safeguarding of machinery
Overview of Item 2
Item 2 in the Table deals with the safeguarding of machinery. A PSR is triggered when any of the following are used as protective elements with an apparatus:
- safeguarding devices that signal the apparatus to stop (including but not limited to those listed in the Table).
- barrier guards that use interlocking mechanical or electrical safeguarding devices.
Protective element means a shield, a guard, an operating control acting as a guard, a locking device or any other device preventing access
. Apparatus means equipment or a machine or device
. See subsection 7(1) of the Industrial Establishments Regulation for details.
The reviewer must consider the following sections of the Industrial Establishments Regulation:
- section 24 (exposed moving part)
- section 25 (in-running nip hazards)
- section 26 (shielding of product, waste)
- section 28 (operating control as a guard)
- section 31 (centrifugal extractor, separator, dryer)
- section 32 (tumbling mill or tumbling dryer)
While not specific to a PSR for Item 2, the following related sections of the Industrial Establishments Regulation may affect design criteria:
- section 40 (electrical equipment, insulating materials and conductors)
- section 75 (blocking of equipment to prevent movement)
- section 76 (lockout of equipment)
The following are examples of equipment or devices that may trigger a PSR if a protective element that meets the circumstances listed in Item 2 of Table is used with them:
- robots integrated with machines (including replacement of the robot) – for example use of a robot to move items to a conveyor on a production line
- collaborative robots if part of a work cell with electronic safeguards
- autonomous vehicle – for example electronic safeguards
Replacing a light curtain with a two-hand control would be considered a new installation of a protective element. As the two-hand control meets the circumstances described in the Table, a PSR would be required.
The integration of a protective element for the system, such as interlock perimeter fencing, would trigger a circumstance in the Table and require a PSR for the entire system. If the integration triggers a circumstance only for a specific machine in the system, then the PSR would only be required for that specific machine.
Out of scope
The following examples of devices do not require a PSR, even if they replace one of the protective elements listed in Item 2 that would have triggered a PSR:
- emergency stop buttons and pull cords
- fixed barrier guards
- holdback devices
- pullback devices
PSR for Item 2
A PSR must include details of the measures to comply with sections 24, 25, 26, 28, 31 and 32 of the Industrial Establishments Regulation, as applicable.
Reviewer for a PSR for Item 2
A reviewer for Item 2 must be an engineer.
Exemptions for Item 2
The term “manufactured” used in the Exemption column of the Table generally means manufactured by the original equipment manufacturer or manufactured in-house.
An exemption from the PSR for Item 2 can be claimed when:
- The protective element was installed at the time the apparatus was manufactured, and:
- the apparatus and the protective element were manufactured in accordance with, or have been modified to meet, current applicable standards and
- the apparatus has been installed in accordance with current applicable standards, if any, and the manufacturer’s instructions
- The protective element was not installed at the time the apparatus was manufactured, and:
- the apparatus and the protective element were manufactured in accordance with, or have been modified to meet, current applicable standards and
- the apparatus and the protective element have been installed in accordance with current applicable standards, if any, and the manufacturer’s instructions
Documents for establishing an exemption
Protective element was installed at the time the apparatus was manufactured
The following would support an exemption when the protective element was installed at the time the apparatus was manufactured, either:
- a written document or certificate from the manufacturer declaring that the apparatus and protective element have been manufactured or modified to meet current applicable standards
- procurement or purchase documentation verifying that the apparatus and protective element have been manufactured or modified to meet current applicable standards
In order to fully establish an exemption for Item 2 when the protective element was installed at the time of manufacture, there must also be a written document or certificate from the installer stating that the apparatus was installed in accordance with current applicable standards, if any, and the manufacturer’s instructions.
Protective element was not installed at the time the apparatus was manufactured
In order to establish an exemption for Item 2 when the protective element was not installed at the time of manufacture, there must be documentation showing that the apparatus was manufactured or modified to meet current applicable standards and that it was installed in accordance with current applicable standards, if any, and the manufacturer’s instructions.
In addition, there must be documentation showing that the protective element was manufactured or modified to meet current applicable standards and that it was installed in accordance with current applicable standards, if any, and the manufacturer’s instructions.
This includes situations in which the existing protective element is replaced with a new and improved safety device.
European Union (EU) Directive 2006/42/EC (Machinery Directive)
When claiming an exemption for a machine designed to this directive, the EU declaration of conformity must both:
- indicate that the machine complies with EU Directive 2006/42/EC (Machinery Directive)
- explicitly state which standards were used to achieve compliance with the Machinery Directive (such as ISO 12100 – Safety of machinery – General principles for design – Risk assessment and risk reduction). In order to claim an exemption, the standards used to prove compliance to this directive must be current applicable standards listed in this guide
Although complying with this directive means the machine was manufactured to meet certain machine guarding standards, a declaration of conformity that does not cite the specific standards is not acceptable as documentation to support the exemption.
A document in writing from the installer stating that the machine was installed in accordance with current applicable standards, if any, and the manufacturer’s instructions is also required for establishing an exemption.
Safeguarding of machinery standards
Standards can be used to claim an exemption from a PSR for Item 2 or to support compliance with the applicable sections of the Industrial Establishments Regulation if completing a PSR for Item 2.
The first list of standards below, marked with an asterisk, are considered to be “current applicable standards” and can be used to claim an exemption.
The second list of machine-specific standards can be used to support compliance with the applicable sections of the Industrial Establishments Regulation when conducting a PSR. These standards have not been reviewed by the Ministry of Labour, Training and Skills Development.
It is recommended that an engineer using CSA-Z432 (2014) – Safeguarding of Machinery for a PSR also reference these machine-specific standards in addition to the general machine guarding standard, where applicable.
Standards for claiming an exemption
- CAN/CSA Z142 (2010)* – Code for Punch Press and Brake Press Operation: Health, Safety, and Guarding Requirements
- CSA-Z432 (2014)* – Safeguarding of Machinery
- CAN/CSA-Z434 (R2013)* – Industrial Robots and Robot Systems-General Safety
- ANSI/B11.02 (2013)* – Hydraulic Power Presses
- ANSI/B11.03 (2012)* – Power Press Brakes (OSHA-CPL 2-1.25)
- ANSI/B11.04 (2003)* – Shears
- ANSI/B11.06 (2001)* – Lathes
- ANSI/B11.08 (2001)* – Drilling, Milling, and Boring
- International Organization for Standardization (ISO) - 12100-1* and 2* – Safety of machinery: basic concepts, general principles for design
- ISO 13857* – Safety of machinery – Safety distances to prevent hazard zones being reach by upper and lower limbs
- ISO-13854* – Minimum gaps to avoid crushing of parts of the human body
- ISO-13851* – Two hand control devices
- ISO-14120* – General requirements for the design and construction of guards
- ISO-14119* – Interlocking devices with and without guard locking
- ISO 13856* (4 parts) – Pressure sensitive protective devices
- ISO 4414* – Safety requirements for fluid power systems and components – pneumatics
- IEC/European Standards (EN) 61496 Parts 1* and 2*
- Part 1: Electro sensitive protective equipment – sensing safeguards
- Part 2: Active opto-electronic protective devices – light curtains
- BS EN ISO 19085-6:2017* - Woodworking machines. Safety - Single spindle vertical moulding machines ("toupies")
- BS EN ISO 19085-3:2017* - Woodworking machines. Safety requirements - Numerically controlled (NC) boring and routing machines
- BS EN ISO 19085-7:2019* - Woodworking machines. Safety - Surface planing, thickness planing, combined surface/thickness planing machines
- BS EN ISO 19085-11:2020* - Woodworking machines. Safety - Combined machines
- BS EN ISO 19085-12:2021* - Woodworking machines. Safety - Tenoning/profiling machines
Standards for supporting compliance
- ANSI/B11.9-1975 (R97) – Grinding Machines
- ANSI/B11.10-1990 (R98) – Sawing Machines
- ANSI/B11.11-1985 (R94) – Gear Cutting Machines
- ANSI/B11.12-1996 – Roll Forming and Roll Bending
- ANSI/B11.13-1992 (R98) – Automatic Screw/Bar and Chucking Machines
- ANSI/B11.15-1984 (R94) – Pipe, Tube, and Shape Bending Machines
- ANSI/B11.16-1988 – Metal Powder Compacting
- ANSI/B11.17-1996 – Horizontal Hydraulic Extrusion Presses
- ANSI/B11.18-1997 – Coil Processing Systems
- ANSI/B11.5-1988 (R94) – Iron Workers
- ANSI/B11.7-1995 (R00) – Cold Headers and Cold Formers
- ANSI/01.1-1992 – Woodworking Machinery-Safety Requirements
- ANSI/Z244.1-2003 – Lockout/tagout of Energy Sources
- ANSI/SPI B151.27-1998 – Robots Used with Horizontal Injection Moulding Machines
- ANSI/Z245.5-1990 – Baling Equipment
- International Electrotechnical Commission (IEC) - 61508 (parts 1, 2, 3, 4, 5) – Functional safety of electrical/electronic/programmable electronic safety related systems
- ISO-13855 – Hand/arm speed – approach speeds of the human body for positioning protective equipment
- ISO 14118 – Prevention of unexpected start up
- IEC 60947 5; 5-1; 5-2; 5-3 – Low voltage switch gear and control gear; Electromechanical control circuit devices; Proximity devices; Proximity devices with defined behaviour under fault conditions
- ISO 4413 – Safety requirements for fluid power systems and components – hydraulics
Machines for cold working of metals
- EN 693 – Hydraulic presses, press-brakes, pneumatic presses
Rubber and plastic machines
- EN 289 – Compression and transfer moulding presses
- EN 422 – Blow moulding machines intended for the production of hollow articles
- EN 1114 – Extruders and extrusion lines
- EN 1417 – Two roll mills
Packaging machines
- EN 415-1 – Common requirements
- EN 415-2 – Machines for preformed rigid packaging
- EN 415-3 – Form, fill and seal machines
- EN 415-4 – Palletizers and depalletizers
- EN 415-5 – Wrapping machines
- EN 415-6 – Machines to form collective packaging
- EN 415-7 – Machines to ensure cohesion of load units
Food processing machines
- EN 1978 Vegetable cutting machines
- EN 1974 Slicing machines
Machines fed by chain(s)
- EN 1218-4 – Tenoning machines – part 4: edge banding machines fed by chain or chains
- EN 1870-13 – Safety of woodworking machines – circular sawing machines - horizontal beam panel sawing machines
- EN 12750 – Four sided moulding machines
Tannery machines
- EN 972 – Reciprocating roller machines
- EN 930 – Roughing, scouring, polishing, and trimming machines
- EN 931 – Footwear manufacturing machines. Lasting machines
- EN 1035 – Moving plate machines
- EN 1845 – Footwear moulding machines
Miscellaneous
- EN 10472 – Industrial laundry machinery
- EN 11111 – Textile machinery
- ANSI B56.5 – Safety standard for driverless, automatic guided industrial vehicles and automated functions of manned industrial vehicles
Flow Chart 3 – Item 2 guarding exemption
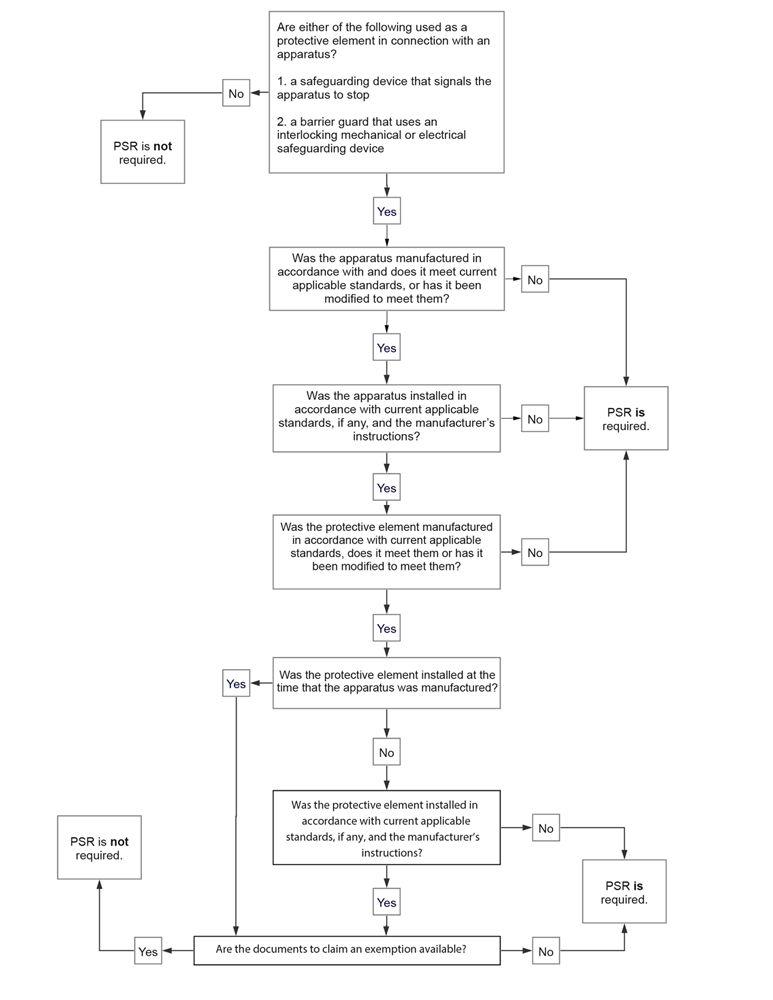