Pre-start reviews (PSRs)
PSRs may be required in a factory before new apparatus, protective elements, structures or processes are installed, used or modified. A formal or informal evaluation of new or modified equipment or processes can determine whether a PSR is required and whether an exemption might apply.
Owners, lessees and employers should have a procedure in place to determine whether a PSR is required:
- when buying new equipment
- when modifying equipment
- before setting up new processes
- before restarting modified equipment
This procedure should be in writing and integrated with pre-purchase and procurement processes.
Persons carrying out the evaluation do not need to be engineers. However, they should have the knowledge (including knowledge of the OHSA and Industrial Establishments Regulation), training, and experience to carry out the evaluation. If it is determined that a PSR is required, the owner, lessee or employer must ensure that a PSR is completed for the apparatus, structure, protective element or process before it is operated or used. This includes testing, commissioning and start up after modifications.
What a PSR is
- An in-depth examination of the apparatus, structure, protective element or process.
- Carried out by a person or persons who have the qualifications set out in the Industrial Establishments Regulation.
- Documented in a written report that includes all the elements required by the Industrial Establishments Regulation.
- Ideally undertaken at the design stage.
What a PSR is not
- A job-task analysis of the interaction between a worker and their tasks at the workplace.
- A review of compliance with all the requirements under the Industrial Establishments Regulation, other than the applicable provisions in the Table.
- An equipment/process inspection or engineering review undertaken after an apparatus, structure, protective element or process has been constructed, added or installed and operated, started or used for the first time.
- An equipment/process inspection or engineering review undertaken after an apparatus, structure, protective element or process has been modified and any new or modified engineering controls and/or other new or modified measures have been used.
- Documents that specify the apparatus or protective element meets current applicable standards. These could form the basis of an exemption.
Where a PSR is required
PSRs are only required in factories. The definition of factory in the OHSA covers a variety of workplaces. Some questions to consider when determining if the workplace is a factory:
- Is there a manufacturing process that produces goods or products?
- Is there an assembly process, such as an assembly line, to make goods or products? Do we use machinery or devices in these processes?
- Is machinery or device(s) used to warehouse products?
- Is machinery or devices(s) used to inspect, finish, repair, clean or adapt products to sell them?
- Is this a facility for the maintenance of transportation vehicles (for example, planes, trains, buses or cars)?
The following are examples of factories:
- manufacturing facilities, for example automotive and automotive parts, chemical, rubber and plastics
- warehouses, for example where machinery or equipment—such as forklifts—are used to move or store products
- laundry facilities, in certain circumstances
- water treatment plants
- maintenance facilities for public transit vehicles
- recycling facilities
If it is unclear as to whether the workplace is a factory, please contact your legal counsel. Although a logging operation may meet the definition of factory, PSRs are not required at logging operations.
When PSRs must be conducted
If a circumstance described in the Table will exist and a listed provision of the Industrial Establishments Regulation applies in a factory other than a logging operation, the owner, lessee or employer must ensure that a PSR is conducted in each of the following situations:
- When a new process will be used or new apparatus, structure or protective element will be constructed, added or installed.
- When an existing apparatus, structure, protective element or process will be modified, and the modifications will require one of the following changes to remain in compliance with the applicable provisions of the Industrial Establishments Regulation:
- new or modified engineering controls
- other new or modified measures
Refer to subsection 7(2) of the Industrial Establishments Regulation and the Table for more details.
The PSR must take all the relevant circumstances and applicable provisions into account when more than one circumstance in the Table exists.
Flow Chart 1 - Determining when a PSR is required
When a PSR is required for a new or existing apparatus, structure, protective element or process, an exemption set out in the Table may apply.
Flow Chart 1, subsection 7(2) and the Table will assist in determining if a PSR is required.
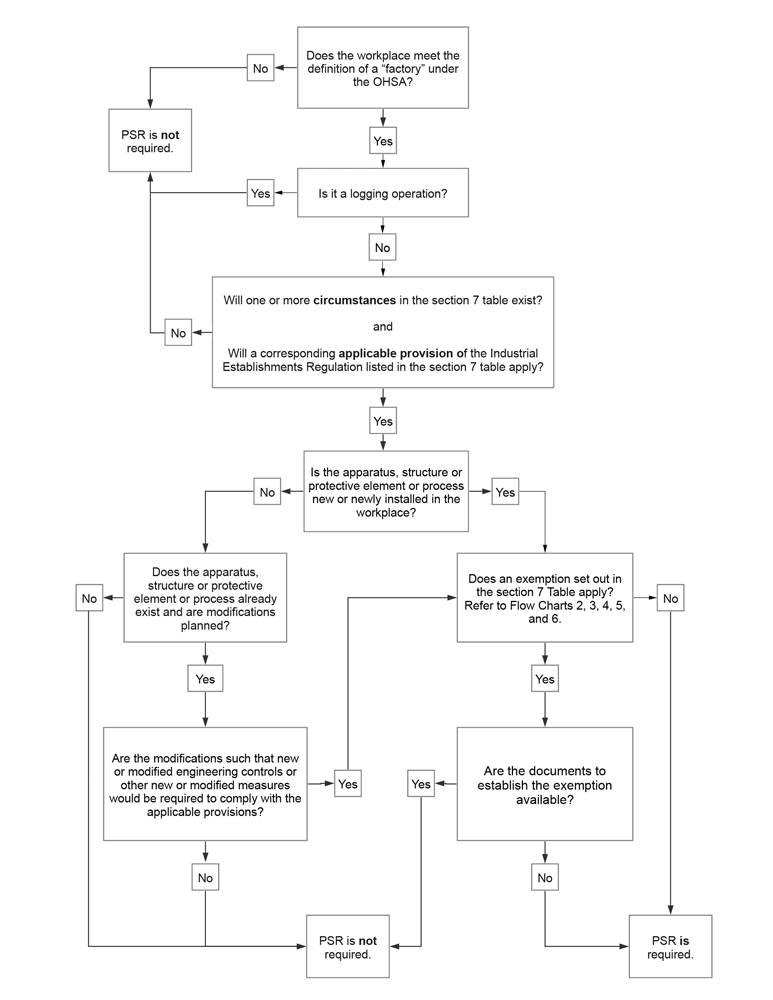
Section 7 table
This table appears in section 7 of the Industrial Establishments Regulation. It lists circumstances where a PSR is required and exemptions to each requirement.
Item | Circumstances | Applicable provisions of this regulation | Exemptions |
---|---|---|---|
1. | Either of the following apply with respect to flammable liquids:
|
Subsections 22 (1), (2) and (4) | All of the following requirements are met:
|
2. | Any of the following are used as protective elements in connection with an apparatus:
|
Sections 24, 25, 26, 28, 31 and 32 |
|
3. | Material, articles or things are placed or stored on a structure that is a rack or stacking structure. | Clause 45 (b) | The rack or stacking structure is designed and tested for use in accordance with current applicable standards. |
4. | A process involves a risk of ignition or explosion that creates a condition of imminent hazard to a person’s health or safety. | Section 63 | The process is conducted inside a spray booth that has been manufactured and installed in accordance with current applicable standards. |
5. | The use of a dust collector involves a risk of ignition or explosion that creates a condition of imminent hazard to a person’s health or safety. | Section 65 | None. |
6. | A factory produces aluminum or steel or is a foundry that melts material or handles molten material. | Sections 87.3, 87.4, 87.5 and 88, subsections 90 (1), (2) and (3), and sections 91, 92, 94, 95, 96, 99, 101, and 102 | None. |
7. | Any of the following are used:
|
Sections 51 and 53 |
|
8. | A process uses or produces a hazardous biological or chemical agent and uses a ventilation system to limit the exposure of a worker in accordance with any exposure limit set out in Regulation 833 of the Revised Regulations of Ontario, 1990 (Control of Exposure to Biological or Chemical Agents) made under the Act. | Sections 127 and 128 | A portable device that extracts smoke, fumes or other substances and that does not exhaust to the outdoors is used. |
Additional considerations
Maintenance, repair and replacement of parts
A PSR is not required for maintenance tasks, such as the replacement of one part with an identical part or “like for like” (for example, changing a broken interlock switch or actuator with a similar interlock switch or actuator).
However, replacement of a part with a part that has different specifications is a modification under the Terms section of this guide that could trigger a PSR.
If there are additional components that must be installed along with the replacement part, they could trigger a PSR.
Series of equipment connected to each other
When a production line or process is formed by the connection of multiple pieces of equipment, a requirement for a PSR for one piece of equipment would not automatically trigger a PSR of all the equipment. Assess each piece of equipment to determine if a PSR would be required.
For example, if a production line with multiple machines that have interlocked gates are connected to each other by conveyors, only the machines with interlocked gates would require a PSR. The conveyors, however, would have to comply with sections 24 and 25 of the Industrial Establishments Regulation, as well as other sections applicable to conveyors.
Changing equipment location
When changing location of an apparatus, structure or process, a PSR would not be required if all of the following apply:
- The location change is within the same workplace.
- There are no modifications to the apparatus, structure or process that would trigger a PSR under subsection 7(2).
- There are no new or modified engineering controls and/or new or modified measures to deal with hazards introduced by changing the location.
If all three of the requirements above are not met, then a PSR must be conducted for the apparatus, structure or process in the new location.
PSR after installation or set-up
If a PSR was not carried out at the design stage and the equipment or process has been installed or set-up, a PSR must be completed or an exemption documented before the equipment is operated or the process is used.
Broader safety and compliance issues
To ensure the safety of their workers and workplace, employers have a broad duty to comply with:
- the OHSA
- the Industrial Establishments Regulation
- any other applicable legal requirements
In some instances, a workplace may have a process in place to assess a broad range of safety and compliance issues and incorporate them into the design of equipment, structures and processes. Other workplaces may not have such processes in place and may ask the person undertaking the PSR to broaden the scope of work beyond the applicable provisions of the Table, to bring the entire system into regulatory compliance.
When writing the PSR report the recommendations for compliance with the applicable provisions in the Table should be clearly separated from other recommendations that are not part of the PSR process.
A design review versus an “as-built” review
A PSR is intended to be a design review prior to installation, not an “as-installed” review. There is no requirement in section 7 to have the installed equipment or process examined by the same person who completed the PSR report, although it would be a best practice.
Persons who can undertake a PSR
Generally, a PSR must be conducted by an engineer. In addition, a person with special, expert or professional knowledge or qualifications could conduct a PSR for Item 8 of the Table (hazardous biological or chemical agents). See subsection 7(4) of the Industrial Establishments Regulation for details.
Engineers licensed in Ontario
Subject to any prescribed requirements or restrictions, an engineer is defined in the Occupational Health and Safety Act as a person who is licensed as a professional engineer or who holds a limited licence under the Professional Engineers Act.
The Ontario Professional Engineers Act (PEA) and its regulations include requirements for the practice of engineering in Ontario. The PEA is administered by Professional Engineers Ontario (PEO), a self-governing organization that grants licenses to qualified individuals, enforces compliance with the licensing requirements and disciplines license holders who are found guilty of incompetence or misconduct. Engineers must follow the Code of Conduct as set out in the Professional Engineers Act and its regulations.
The PEO also provides practice guidelines for engineers, including a Pre-Start Health and Safety Review Guideline.
An employer, lessee or owner may contract out a PSR to a third-party engineer or consulting engineering firm or use in-house or company engineers, provided that the engineer meets the requirements of the Professional Engineers of Ontario (PEO).
Engineers from other jurisdictions
An engineer from another jurisdiction can only conduct the PSR if they are granted a license by Professional Engineers Ontario (PEO) to practice in Ontario.
Person who possesses special, expert or professional knowledge
A PSR for item 8 of the Table must be conducted by an engineer or by a person who possesses special, expert, or professional knowledge or qualifications appropriate to assess any potential or actual hazards. This person may have a specific qualification (for example, a Certified Industrial Hygienist (CIH) or Registered Occupational Hygienist (ROH).
Multi-disciplinary teams
A multidisciplinary team approach can be taken for a PSR where more than one discipline, may take part in the review, for instance an engineer and an industrial hygienist. In other cases, a team of engineers may conduct the review.